In modern industrial manufacturing, the ability to generate oxygen on-site has become increasingly vital across sectors such as metallurgy, glass processing, wastewater treatment, and ozone generation. Among the many oxygen supply solutions available, industrial oxygen concentrators—particularly those based on Pressure Swing Adsorption (PSA) technology—stand out for their reliability, modularity, and cost-effectiveness.
Compared to traditional oxygen delivery methods such as liquid oxygen tanks or high-pressure cylinders, industrial oxygen concentrators offer significant advantages: reduced logistics costs, lower safety risks, continuous supply capability, and easier integration into automated systems. These benefits are particularly important for facilities aiming to minimize downtime and reduce dependence on external gas vendors.
This article aims to provide a comprehensive understanding of how industrial oxygen concentrators work, focusing on their core mechanisms, such as PSA-based selective adsorption, key components like compressors and molecular sieves, and optimization strategies involving control systems and energy efficiency. Whether you’re planning a new oxygen generation setup or looking to upgrade an existing one, this guide will help you evaluate performance, ensure safety, and enhance operational sustainability.
I. What Is an Industrial Oxygen Concentrator?
An industrial oxygen concentrator is a machine designed to extract oxygen from ambient air and supply it at a controlled flow rate and purity for continuous industrial applications. Unlike small-scale medical units, industrial systems are engineered for high-volume output, long-term operation, and integration into automated processes.
1. Core Function and Key Applications
Industrial oxygen concentrators typically produce oxygen at concentrations between 90% and 95%, depending on the system type and pressure conditions. They are widely used in industries where a stable and on-demand oxygen supply is required, including:
Metal processing (e.g., cutting, welding, brazing)
Glass manufacturing (supports high-temperature furnaces)
Ozone generation systems (as a pure oxygen feed gas)
Aquaculture and fish farming (water oxygenation)
Wastewater treatment (activated sludge and odor control)
Paper and pulp industry, gold leaching, and more
These systems are especially useful in remote sites or regions where regular delivery of bottled or liquid oxygen is expensive, unreliable, or unsafe.
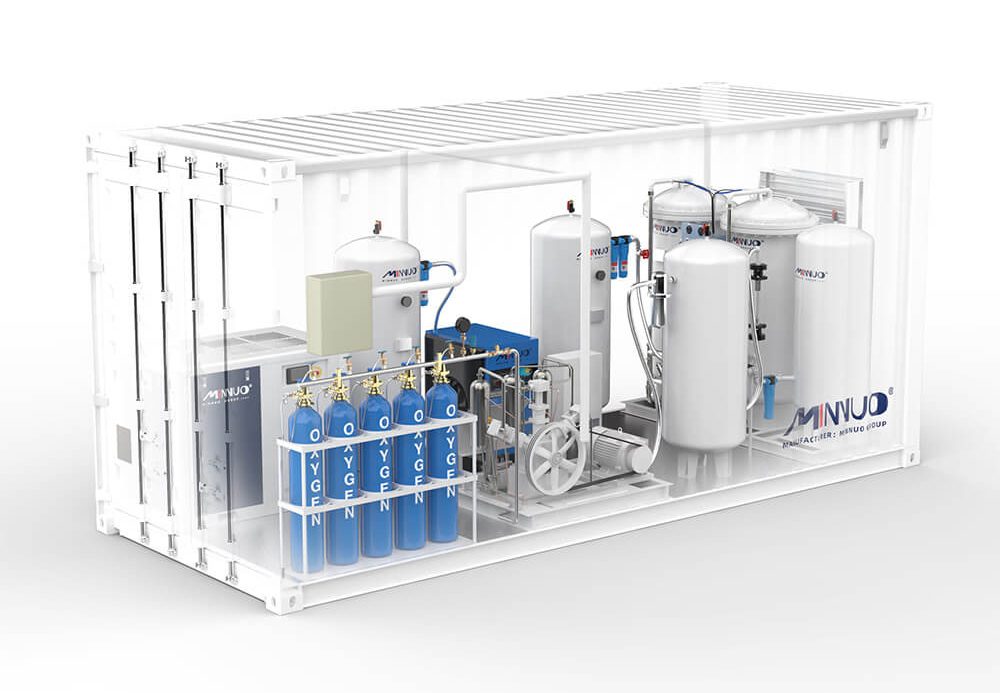
2. Differences from Medical/Industrial Oxygen Concentrators
While both types rely on the same PSA (Pressure Swing Adsorption) principle, industrial oxygen concentrators differ significantly in the following ways:
Feature | Medical Oxygen Concentrator | Industrial Oxygen Concentrator |
Oxygen Output | 1–10 L/min | 10–300 Nm³/h or more |
Run Time | Intermittent, for short durations | 24/7 continuous operation |
Structure | Compact, portable units | Modular skid-mounted or cabinet-type |
System Integration | Standalone | Integrates with PLC, compressors, etc. |
Target Use | Individual patient care | Industrial-scale oxygen consumption |
3. Benefits of Using Industrial Oxygen Concentrators
On-site production reduces dependency on bottled oxygen
Lower long-term cost and avoids logistics for refilling
Increased safety—no need to store high-pressure cylinders
Modular and scalable—output can be expanded as needed
Environmentally friendly, especially when paired with energy-saving compressors
4. Typical System Output Specs
Oxygen Purity: 90%–95%
Flow Rate: 5–300 Nm³/h (depending on model and configuration)
Output Pressure: 0.3–0.6 MPa (adjustable or matched with booster)
Optional: Buffer tank, flowmeter, oxygen analyzer, and remote monitoring module
II. Core Working Principle: Pressure Swing Adsorption (PSA)
Pressure Swing Adsorption (PSA) is the foundational technology behind most industrial oxygen concentrators. It utilizes the difference in adsorption properties of gases under varying pressure to separate oxygen from air. By cycling between high and low pressure, the system alternately adsorbs and desorbs nitrogen, delivering oxygen-enriched gas as the final product.
1. Working Mechanism: What Is PSA?
PSA leverages adsorbent materials like Zeolite molecular sieves, which have a stronger affinity for nitrogen molecules than oxygen under pressure. When air is compressed and passed through an adsorption column filled with zeolite:
Nitrogen is captured on the surface of the adsorbent.
Oxygen remains in the gas phase and flows out as the product gas.
By lowering the pressure, the adsorbed nitrogen is released (desorbed), regenerating the adsorbent and making it ready for the next cycle.
2. Dual-Tower PSA Cycle Breakdown
Industrial PSA systems commonly use a dual-tower design to ensure continuous gas production while alternating between adsorption and desorption phases. The full cycle includes the following steps:
Step | Description | Purpose |
Air Compression & Pretreatment | Air is compressed and dried using a dryer and filters to remove moisture, oil, and dust | Protects the molecular sieve and ensures stable operation |
Pressurized Adsorption Phase | Compressed air enters Tower A; nitrogen is adsorbed, oxygen passes through | High-purity oxygen (>90%) is collected from the top of the tower |
Depressurization & Desorption Phase | Tower A reduces to atmospheric pressure or below; adsorbed nitrogen is released | Regenerates the zeolite for next cycle |
Tower Switch-over | Tower B now begins adsorption while Tower A regenerates | Achieves uninterrupted operation |
Cycle Duration: Typically 30–90 seconds per tower, optimized based on flow rate and oxygen demand.
3. Purity Monitoring & Valve Control
For stable performance and safety, PSA systems employ:
Oxygen analyzers to monitor purity in real-time (e.g., maintain >93%)
Automated valve manifolds driven by PLC to precisely control:
Inlet pressure
Timing of adsorption/desorption
Synchronization between towers
Buffer tanks to store and smooth the oxygen output between cycles
This ensures consistent pressure, flow, and purity even under varying downstream demand.
4. Advantages of PSA Technology in Industrial Settings
On-demand generation—no cylinder logistics or delivery delays
Energy-efficient at medium-high flows
Scalable by increasing bed volume or adding towers
Safe—low-pressure oxygen output, no cryogenic risks
Reliable—continuous 24/7 operation with proper maintenance
III. Key Components of an Oxygen Concentrator
A PSA-based industrial oxygen concentrator operates as a system of integrated components. Each part plays a vital role in ensuring efficient air separation, oxygen purity, and stable performance. Below is a breakdown of the key subsystems:
1. Air Compressor
Role: Provides the initial compressed air feedstock necessary for oxygen separation.
Function: Converts ambient air into high-pressure air (typically 6–10 bar) suitable for adsorption towers.
Type: Oil-free screw compressors are widely used to prevent contamination.
Design Consideration: Stable output, energy efficiency, and continuous duty cycle.
Importance: Inadequate air supply or pressure fluctuations directly impact oxygen flow rate and purity.
✅ Note: Often paired with a buffer tank to stabilize pressure and extend compressor life.
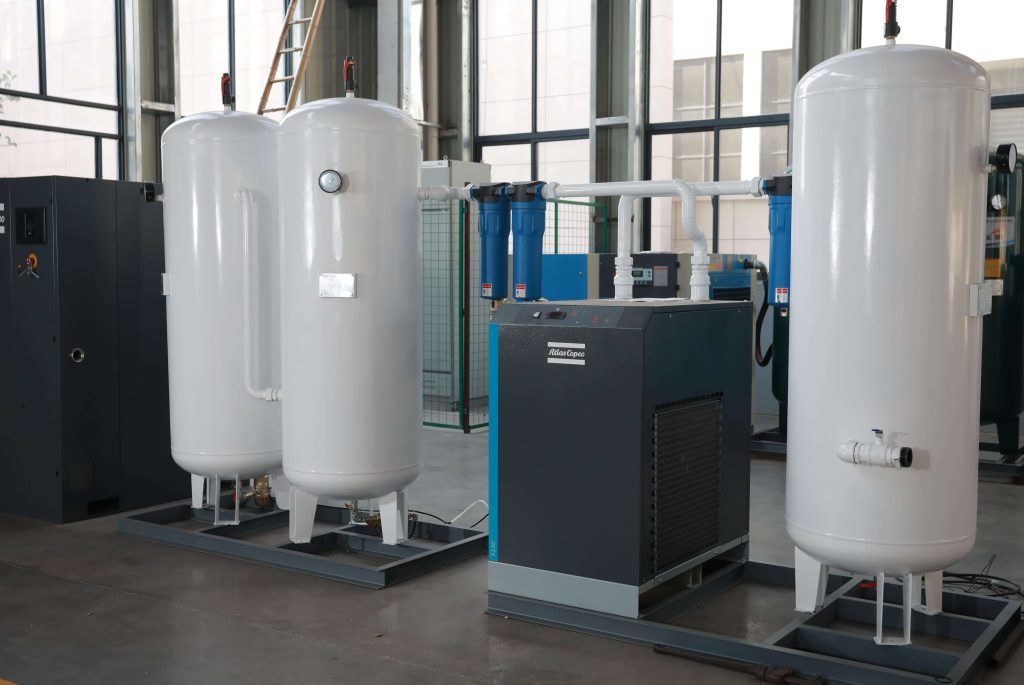
2. Filtration System
Role: Pre-treatment of compressed air to protect downstream equipment.
Stage 1: Coarse particulate filter (≥5μm) – removes dust and large debris.
Stage 2: Coalescing oil mist filter – captures fine oil aerosols and mists.
Stage 3: Refrigerated dryer or adsorption dryer – lowers dew point to avoid moisture-related molecular sieve degradation.
Stage 4 (Optional): Activated carbon filter – removes hydrocarbons or odor.
Key Point: Clean, dry air significantly extends the lifespan of molecular sieves and improves oxygen purity stability.
3. Adsorption Towers & Molecular Sieves
Role: The heart of PSA separation – where nitrogen is adsorbed and oxygen is separated.
Material: Zeolite 13X (for oxygen generation) selectively adsorbs nitrogen from air.
Structure: Dual-tower alternating configuration—while one adsorbs, the other regenerates.
Loading Strategy: Proper filling density and packing method avoid channeling and ensure uniform flow.
Key Parameters:
Adsorption cycle time (5–60s based on purity)
Bed temperature (higher temperatures lower performance)
Adsorption pressure (optimal 6–8 bar)
Maintenance Tip: Replace molecular sieves every 3–5 years depending on system hours and air quality.
4. Automatic Valves & PLC Control System
Role: Coordinates timing and sequencing of adsorption, desorption, and pressure equalization.
System: Electrically-actuated or pneumatic solenoid valves.
Controller: PLC (Programmable Logic Controller) adjusts timing based on pressure sensors and purity readings.
Functionality:
Synchronizes tower switching
Tracks oxygen concentration with online sensors
Provides alarms for pressure drop, impurity spikes, or flow irregularities
Value: Smart controls improve response time, reduce energy consumption, and ensure consistent O₂ purity.
5. Oxygen Buffer Tank & Pressure Regulation
Role: Stabilizes final oxygen output and adapts delivery pressure to application needs.
Buffer Tank: Absorbs flow fluctuations, supports system decoupling.
Pressure Regulator: Ensures downstream process receives oxygen at constant pressure (commonly 0.2–0.4 MPa).
Enhancements:
Flow meters
Oxygen purity analyzers (typically zirconia or electrochemical sensors)
Backflow prevention valve
Target Applications: Especially critical in industries like laser cutting, steel annealing, or filling oxygen cylinders where output flow and pressure stability are vital.
IV. Factors Affecting Performance and Efficiency
Industrial PSA oxygen concentrators are designed for high reliability and performance, but their actual efficiency and output depend on multiple operational and design parameters. This section outlines key factors that influence system effectiveness.
1. Adsorption vs Desorption Pressure Ratio
Core Principle:
The efficiency of PSA depends on creating a large enough pressure differential to enable selective nitrogen adsorption and effective oxygen release.
Typical Pressure Range:
Adsorption: 5–8 bar (0.5–0.8 MPa)
Desorption: atmospheric pressure or vacuum
Design Target: Maintain a 4:1 to 6:1 pressure ratio between adsorption and desorption phases
Impact: A higher pressure ratio improves nitrogen removal efficiency, but also increases compressor load and energy consumption.
✅ Optimization Tip: Use variable-speed compressors and pressure-regulated blowback to maintain optimal cycling energy use.
2. Temperature and Environmental Humidity
Effect on Adsorption:
Temperature Rise → decreases adsorption capacity (due to exothermic nature of adsorption)
High Humidity → degrades molecular sieves over time, especially zeolite 13X
Control Strategies:
Integrate heat exchangers or air-cooled pre-chillers to keep intake air <35°C
Install refrigerated or adsorption dryers to maintain dew point ≤ -20°C
Field Note: Oxygen concentrators installed in hot and humid climates (e.g., Southeast Asia, Africa) require upgraded air treatment units for consistent output.
3. Adsorbent Material Characteristics
Key performance indicators of molecular sieves include:
Adsorption Rate: Influences cycle frequency and output flow stability
Service Life: Typically 10,000–20,000 hours; deteriorates faster if exposed to oil or water
Contamination Resistance: Ability to resist fouling from oil vapors, dust, and acidic gases
Material Advancements:
Lithium-based zeolite (LiX): Higher oxygen yield at shorter cycles, often used in high-purity units
Hybrid or nano-porous adsorbents: Extend lifespan, lower regeneration temperature
Best Practice: Choose sieve type based on desired O₂ concentration vs throughput trade-off. Use inlet gas analyzers to track early sieve performance decline.
4. Control System Logic and Valve Response
The PLC and control valve actuation logic directly influence oxygen output quality and system responsiveness.
Key Parameters:
Tower switch timing
Equalization delay
Pressure stabilization time
Advanced Controls:
Adaptive cycle optimization based on flow rate
Alarm triggers for low oxygen concentration (<90%)
Real-time SCADA interface for remote monitoring
Result: Smart PLC programming can reduce energy use by 8–15% and improve long-term system uptime.
5. Purity vs Flow Rate Trade-off
There’s always a balancing act between maximizing oxygen purity and maximizing flow rate:
Parameter | Effect at Higher Value |
Purity (>95%) | Lower output volume, longer cycle, more energy use |
Flow rate | Reduced retention time, lower purity, faster sieve wear |
Decision-Making Guidance:
Choose 90–93% purity for combustion, wastewater, ozone systems
Choose >95% purity for medical oxygen, gas cylinder filling, electronic-grade applications
Dynamic Optimization: Install a purity-flow selector that automatically adjusts sieve cycling based on downstream sensor feedback.
V. Emerging Technologies and Enhancements
As industrial applications demand higher efficiency, smarter control, and enhanced adaptability, oxygen concentrator technology is evolving rapidly. New materials, modular design concepts, and hybrid process integration are redefining system performance benchmarks. This section explores key innovation frontiers.
1. Advanced Adsorbent Materials
Next-generation adsorbents significantly enhance separation performance by increasing adsorption capacity, selectivity, and lifespan.
Lithium-based Zeolite (LiX):
Higher nitrogen adsorption capacity than traditional 13X
Enables shorter cycles, lower energy consumption
Particularly useful in high-purity medical and electronic-grade oxygen systems
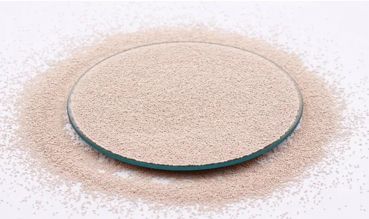
Metal–Organic Frameworks (MOFs):
High surface area (up to 7000 m²/g), tunable pore sizes
Enhanced selectivity and faster mass transfer
MOF-ZIF materials can improve O₂ throughput by 30–40% in pilot systems
Challenge: cost and moisture stability
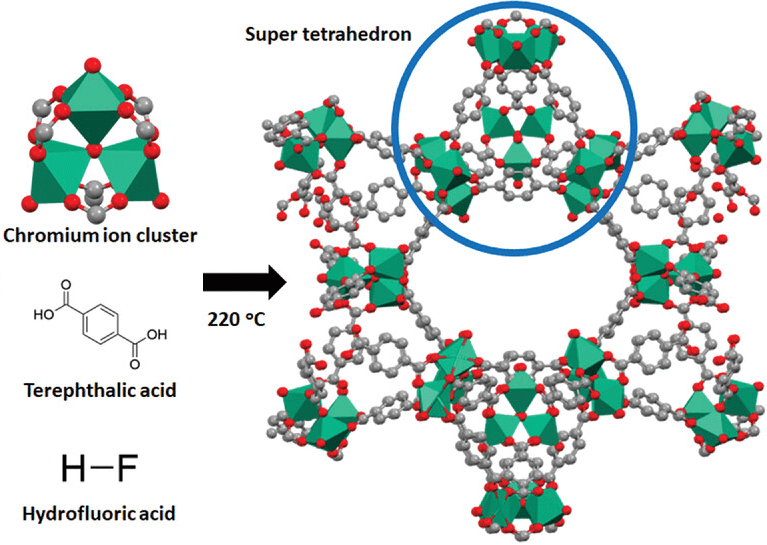
Hybrid Composites:
Combine zeolites or MOFs with graphene oxide, metal oxides, or nanoclays to resist moisture and heat
Improve thermal stability and reduce regeneration energy demand
Impact: Improves efficiency by 10–20%, lowers energy usage, and extends molecular sieve life.
2. Smart Control Systems and AI Integration
Advanced oxygen generators are now equipped with AI-based controllers that continuously adapt to usage patterns, environment, and equipment wear.
Core Functions:
Load sensing and automatic pressure regulation
Real-time purity monitoring with feedback loops
Cycle optimization based on demand fluctuations
Predictive maintenance via sensor analytics
Energy-Saving Algorithms:
Switch to “low power standby” during non-peak hours
Extend sieve cycle under stable load to reduce compressor duty cycles
Benefit: Reduce energy costs by 15–25%, reduce fault rates, extend equipment service intervals.
3. Modularization and Scalable Architectures
Modular design enables easy expansion, maintenance, and transportability, making it suitable for growing facilities or sites with varying gas demands.
Skid-Mounted Modules:
Each module contains its own compressor, dryer, sieves, and PLC
Can be expanded from 10Nm³/h to 1000Nm³/h without reconfiguring entire system
Plug-and-Play Deployment:
Rapid integration into mobile systems (e.g., trailers, containers)
Ideal for construction sites, field hospitals, and remote industrial hubs
Benefits:
Faster installation (days vs. weeks)
Easier component replacement
Supports redundancy and uninterrupted upgrades
Engineering Insight: Adopt modular PSAs with standardized inlet/output to streamline long-term scaling.
4. Hybridization with Other Separation Processes
To overcome PSA limitations in extreme purity, moisture, or energy scenarios, many OEMs are integrating complementary separation technologies:
TSA (Temperature Swing Adsorption):
Pre-drying or high-selectivity stage before PSA
Eliminates deep chillers or complex desiccant towers
Improves PSA consistency in humid climates
Membrane Separation + PSA:
Stage 1 membrane removes O₂ and H₂O to achieve ~95% purity
Stage 2 PSA upgrades to >99% for electronic or medical oxygen
Cuts PSA workload and compressor runtime
Deep-Chilled Pre-Conditioning:
Used before PSA for applications requiring ultra-dry or ultra-pure gas (e.g., aerospace, metallurgy)
Future Trend: Convergence of PSA + TSA + Membrane into unified control platform for dynamic gas blending.
Summary Table – Innovation Drivers and Benefits
Technology Frontier | Problem Solved | Value Delivered |
MOF / LiX / Hybrid Adsorbents | Slow cycles, low purity | 20–40% throughput boost, energy reduction |
AI-Based Controls | Load fluctuations, manual tuning | 15–25% energy savings, predictive uptime |
Modular PSA Design | Expansion bottleneck, downtime risk | Fast deployment, easy scalability |
PSA + TSA/Membrane | Moisture, high purity, cost tradeoff | Tailored supply curve, wider application |
Conclusion
Industrial oxygen concentrators, based on the Pressure Swing Adsorption (PSA) principle, offer a reliable and scalable method for on-site oxygen generation. By understanding their core components, working cycles, and performance-affecting parameters—such as pressure ratio, adsorbent material, and system controls—users can optimize for purity, energy efficiency, and operational longevity. These systems are vital for industries ranging from metal cutting and glass manufacturing to ozone generation and wastewater treatment, where continuous and controllable oxygen flow is critical.
For those seeking tailored oxygen generation solutions, MINNUO offers advanced industrial PSA oxygen systems with modular design, intelligent control, and high-performance adsorbents such as Zeolite 13X. Whether you require high purity, compact footprint, or automation-ready configurations, MINNUO’s engineering expertise can help you deploy efficient, cost-effective oxygen concentrators built for long-term industrial reliability and safety.