In the field of industrial gases, nitrogen is widely used for its stability and versatility, with nitrogen generation equipment serving as a critical tool for efficient supply. Among the many factors influencing system performance, compressed air quality is paramount. This article provides a brief overview of the requirements, treatment processes, technical principles, and quality control of compressed air for nitrogen generators, helping users enhance system stability and economic efficiency.
Nitrogen generation equipment primarily requires compressed air to meet three criteria: cleanliness, dryness, and stable pressure. To ensure the adsorption efficiency of carbon molecular sieves and the purity of the produced nitrogen, the air entering the system must undergo rigorous multi-stage purification, including dehydration (dew point between -20°C to -60°C), oil removal (oil content ≤ 0.01 ppm), and dust removal (filtration accuracy down to 0.01 μm), while maintaining a stable pressure of 0.6–1.0 MPa. Depending on working conditions, equipment such as refrigerated dryers, desiccant dryers, precision filters, and activated carbon filters should be used to meet ISO 8573.1 standards.
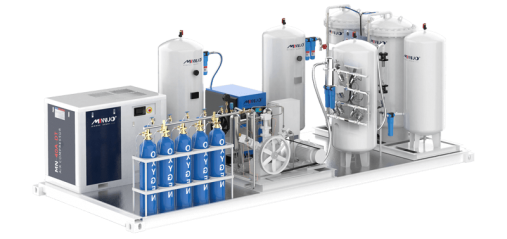
1. Overview of the Working Principle of Nitrogen Generation Equipment
Currently, the most common industrial method for nitrogen production is Pressure Swing Adsorption (PSA). This technology separates nitrogen from oxygen in the air based on their different adsorption properties, allowing for continuous nitrogen production.
The core component of a PSA nitrogen generation system is the adsorption tower, which is filled with carbon molecular sieve (CMS). When compressed air enters the tower, oxygen is preferentially adsorbed, while nitrogen passes through, thus achieving nitrogen separation.
However, this process requires extremely clean air. Contaminants such as oil, water, and solid particles not only reduce the adsorption efficiency of the CMS but also significantly impact equipment lifespan and nitrogen purity. Therefore, compressed air must be professionally purified before entering the nitrogen generation system.
2. Basic Requirements for Compressed Air Purification
(1) Dehydration Requirements
If moisture in the air is not removed before entering the adsorption tower, it can reduce the capacity of the molecular sieve and may condense into liquid water, blocking pipelines and damaging the adsorption structure. Thus, dryers are necessary to control dew point levels.
- General requirement: Dew point of compressed air should be controlled between -20°C and -40°C.
- High-demand scenarios (e.g., electronics, chemicals): Dew point must be below -60°C.
- Equipment used: Typically refrigerated dryers or desiccant dryers.
(2) Oil Removal Requirements
During air compression, lubricating oil mist and vapor inevitably mix into the air. Oil deposits on the molecular sieve surface can deactivate its adsorption function.
- Treatment standard: Compressed air must pass through high-efficiency oil removers and multi-stage filters to remove oil mist and vapor. Recommended oil content: below 0.01 ppm.
- For special applications: Activated carbon filters can be used for further purification.
(3) Dust Removal Requirements
Solid particles in the air can cause valve jamming, pipe abrasion, and filter blockage, and also degrade the molecular sieve’s performance. Typically, a 3–4 stage filtration system is employed:
Filter Type | Filtration Accuracy | Function Description |
Coarse Filter | ≥5 μm | Traps large particle impurities |
Precision Filter | ≥1 μm | Removes fine particles and part of the oil mist |
Ultra-precision Filter | ≥0.01 μm | High-precision filtering to protect the molecular sieve |
Activated Carbon Filter (optional) | — | Removes odors and gaseous organics |
3. Typical Compressed Air Treatment Process
To ensure the stable operation of nitrogen generation equipment, compressed air must undergo the following treatment steps before entering the system:
- Air Compressor: Compresses air to approximately 0.8 MPa (system design pressure).
- Air Receiver Tank: Stabilizes airflow and settles large particles.
- Pre-filter: Removes liquid water and coarse particles.
- Refrigerated Dryer: Reduces water vapor content and controls dew point.
- Precision Filter: Eliminates oil mist and fine particles.
- Desiccant Dryer (if required): Provides further drying to meet lower dew point requirements.
- Activated Carbon Filter (if required): Further oil and odor removal.
- Post-filtered Air Tank: Buffers air pressure and stabilizes air supply.
- Nitrogen Generator: Purified compressed air enters the adsorption tower for nitrogen production.
4. Air Pressure Control Requirements
Nitrogen generation equipment requires a stable inlet pressure, typically between 0.6–1.0 MPa, with 0.8 MPa being optimal. Instability in pressure can lead to poor adsorption, fluctuations in nitrogen output, or system shutdowns due to alarms.
- Stabilization measures: Pressure regulators and sensors should be installed, and a reasonable air tank capacity should be configured based on air consumption to avoid frequent start-stop cycles that affect system longevity.
5. Why Compressed Air Quality Matters
- Improved Nitrogen Generation Efficiency: Clean air enhances the adsorption and separation speed of the carbon molecular sieve.
- Extended Equipment Life: Reduces system corrosion and blockages caused by contaminants.
- Lower Operating Costs: Minimizes frequency of sieve replacement and maintenance expenses.
- Ensured Nitrogen Purity: Prevents moisture and oil from entering the final product and compromising process quality.
- Reduced Downtime: Increases system stability and uptime.
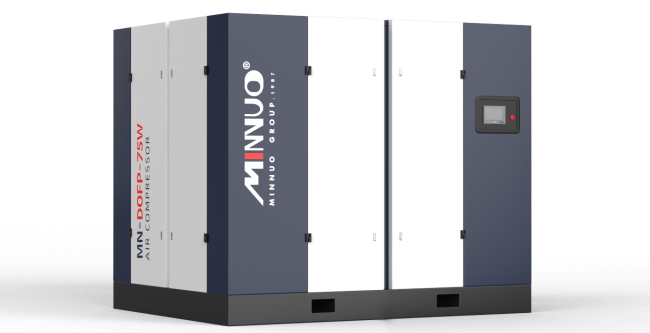
6. Customized Air Treatment Recommendations for Different Conditions
Based on varying requirements for nitrogen purity, dew point, and pressure across industries, pre-treatment for nitrogen systems should be customized:
- Food Industry: High standards for dew point and oil content—recommend desiccant dryers and a four-stage filtration system.
- Pharmaceutical Industry: Requires sterile and oil-free air—suggest installing high-efficiency sterilizing filters and oil vapor filters.
- Metal Heat Treatment Industry: Needs low dew point nitrogen for high-temperature applications—uses twin-tower desiccant dryer systems.
7. Reference for Compressed Air Quality Standards (ISO 8573.1)
The international standard ISO 8573.1 clearly classifies levels of compressed air purity for industrial use:
- Oil Content Classes: From Class 0 (strictest, ≤0.01 mg/m³) to Class 4 (typical, ≤25 mg/m³).
- Particle Classes: Defined by particle size range (e.g., Class 2: particle size ≤1 μm, concentration ≤1 mg/m³).
- Moisture Classes: Dew point ranges from -70°C (Class 1) to +10°C (Class 6).
8. MINNUO’s Air Purification Solutions for Nitrogen Systems
As a professional nitrogen generation equipment manufacturer, MINNUO has extensive experience in system integration. We offer not only high-performance PSA nitrogen generators but also comprehensive air pre-treatment solutions, including:
- Low energy consumption refrigerated and desiccant dryers;
- Multi-stage filters and high-efficiency oil removers;
- Automatic drain devices and dew point monitoring systems.
All equipment can be customized according to site conditions, achieving optimal configurations for various applications and ensuring long-term, stable, and efficient system operation.
9. Conclusion
Compressed air quality is the foundation of nitrogen generation system performance. For users seeking high quality, high efficiency, and long service life, investing in a scientific and well-designed compressed air treatment system is key to maximizing returns. MINNUO remains committed to providing high-standard nitrogen solutions to customers worldwide, supporting your industrial production to reach new heights.