With industrialization advancing, Pressure Swing Adsorption (PSA) has become a widely used, energy-efficient gas separation method; this article explores key factors affecting nitrogen generator purity standards and offers targeted solutions for improving non-compliant nitrogen purity.
The causes of nitrogen generator purity not meeting the standards include high flow rates, carbon molecular sieve aging, electromagnetic valve failure, and issues with regulation valves. High flow rates increase the load on the adsorption system, while aging and contamination of the molecular sieve reduce its adsorption capacity. Failures in electromagnetic and regulation valves impact gas flow, which in turn reduces purity. To ensure nitrogen purity, users should follow the equipment’s standard operating procedures, regularly inspect and replace molecular sieves, ensure air quality, and maintain key components such as electromagnetic and regulation valves.
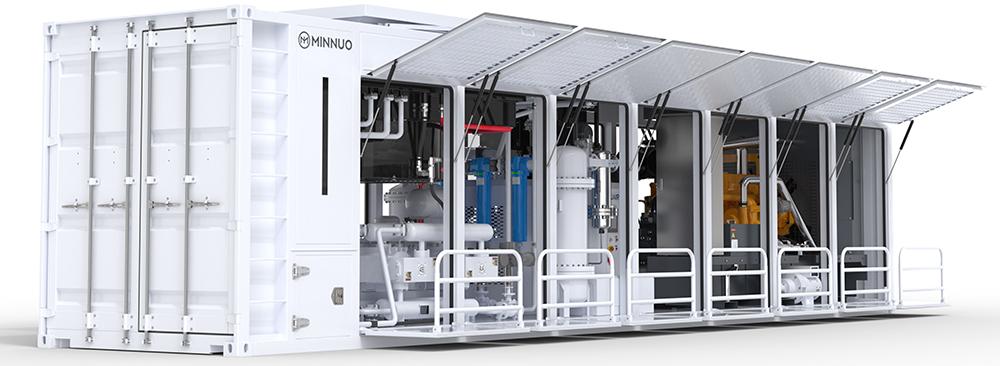
1. What is Nitrogen Generator Purity?
1.1 Definition of Nitrogen Generator Purity
The purity of a nitrogen generator refers to the percentage of nitrogen in the produced gas. Air contains 21% nitrogen, and the purity of nitrogen produced by PSA molecular sieve technology typically ranges from 97% to 99.9995%. Nitrogen purity is one of the key indicators for evaluating the performance of a nitrogen generator, directly affecting the application of the gas and the safety of the production process. For instance, in the chemical, pharmaceutical, and food industries, nitrogen purity is crucial for product quality and production safety.
1.2 Measurement of Nitrogen Purity
To ensure that the nitrogen purity meets design standards, PSA nitrogen generators are usually equipped with oxygen analyzers for real-time monitoring. The oxygen analyzer evaluates the purity of nitrogen by measuring the oxygen content in the nitrogen gas. If the oxygen content exceeds the preset safety threshold, the oxygen analyzer will trigger an alarm, prompting the operator to troubleshoot. Such systems typically use both visual and audible alarms to notify the operator when nitrogen purity is out of specification, allowing for timely corrective actions to avoid disrupting the production process.
2. Causes of Nitrogen Generator Purity Non-Compliance
The causes of nitrogen generator purity not meeting the standards can be analyzed from multiple perspectives, including equipment design, operational practices during use, and the aging or damage of components. Below are common reasons affecting nitrogen purity.
2.1 High Flow Rate
The purity of nitrogen produced by a PSA nitrogen generator is closely related to the gas flow rate. The equipment design specifies both purity and flow rate standards, but in practice, users often adjust the gas flow rate due to various factors. High flow rates increase the load on the nitrogen generator’s adsorption system, reducing its adsorption capacity and, consequently, lowering nitrogen purity.
Solution:
2.2 Carbon Molecular Sieve Aging
The carbon molecular sieve is the core component of PSA nitrogen generators, responsible for separating nitrogen and oxygen in the air. Over time, the adsorption capacity of the sieve gradually decreases, especially in environments with high humidity or excessive oil and gas content, leading to contamination or aging of the sieve, which reduces nitrogen purity.
Solution:
2.3 Electromagnetic Valve Failure
The electromagnetic valve in a PSA nitrogen generator controls the gas flow and switching during the adsorption process. If the electromagnetic valve malfunctions, such as failing to activate or responding slowly, it can cause abnormalities in the adsorption process and affect nitrogen purity.
Solution:
2.4 Regulation Valve Issues
Regulation valves control the gas flow rate and outlet pressure, directly influencing nitrogen production and purity. If the regulation valve is unresponsive or improperly adjusted, it may lead to excessive or insufficient nitrogen flow, thus affecting nitrogen purity.
Solution:
2.5 System Aging and Insufficient Maintenance
Over time, the components of a PSA nitrogen generator naturally age, particularly seals and pipes. An aging system can lead to gas leaks, reduced adsorption capacity, or other faults, ultimately affecting nitrogen purity.
Solution:
- Follow equipment design standards: Users should strictly adjust flow rates according to the equipment manual and avoid arbitrary adjustments.
- Professional adjustments: If flow rate adjustments are necessary, it is advisable to perform them under the guidance of a qualified technician to ensure proper equipment operation.
- Regular molecular sieve replacement: It is recommended to inspect the molecular sieve annually. If aging or a decrease in adsorption capacity is detected, replacement should be done promptly.
- Ensure air quality: During operation, controlling the moisture, oil, and other impurities in the air is critical to avoid contaminating the molecular sieve.
- Install a filtration system: Ensure that an efficient air filtration system is in place before compressed air enters the PSA nitrogen system to remove contaminants.
- Periodic inspection of electromagnetic valves: Regularly inspect the operational status of the electromagnetic valve to ensure it works flexibly and reliably. Using high-quality valves can reduce the likelihood of failures.
- Timely replacement of faulty components: When electromagnetic valve failures occur, timely replacement or repair should be done to prevent impacting the entire nitrogen generation process.
- Accurate regulation: Operators should precisely adjust the outlet flow rate to ensure nitrogen purity meets design requirements.
- Regular inspection of regulation valves: Regulation valves should be regularly inspected and maintained to avoid issues like sticking or leaks, which affect nitrogen quality.
- Regular maintenance: Users should schedule periodic inspections and maintenance to ensure all components are in optimal working condition.
- Timely replacement of aging components: Replace aging parts, especially seals, valves, and pipes, to maintain system integrity.

3. MINNUO Tips: How to Improve the Reliability and Lifespan of Nitrogen Generators
3.1 Improve Air Quality
To ensure long-term effective operation of the molecular sieve, maintaining air quality is crucial. Moisture, oil, and other contaminants in the air can reduce the sieve’s adsorption capacity and even poison the sieve.
3.2 Regular Molecular Sieve Inspection and Replacement
The lifespan of the molecular sieve directly affects nitrogen purity, so regular inspection and replacement are critical.
3.3 Maintenance of Electromagnetic and Regulation Valves
Electromagnetic and regulation valves are core control components of PSA nitrogen generators, and their good working condition must be maintained.
3.4 Professional Maintenance and Operational Training
Users must undergo professional training when operating nitrogen generators to understand the working principles and maintenance points of the equipment. Additionally, regularly hiring professional technicians for equipment maintenance and upkeep can enhance the long-term stability of the nitrogen generator.
- Air compressor inspection: Ensure that the air compressor operates oil-free and regularly inspect the oil separator and filter system.
- Install an air dryer: Equip a high-efficiency air drying system, such as a refrigerated dryer, to ensure dry air with no moisture.
- Filter inspection: Regularly inspect nitrogen exhaust filters to ensure no contaminants accumulate.
- Regular inspection of molecular sieve wear: Periodically check the wear of the molecular sieve and replace it if necessary.
- Monitor molecular sieve usage environment: Ensure that the air’s moisture and oil content meet specified standards to avoid contamination of the sieve.
- Periodic calibration of electromagnetic and regulation valves: Ensure that the valves operate sensitively and are free from leaks.
- Regular cleaning and replacement: Clean electromagnetic and regulation valves regularly to prevent clogging, and replace them when necessary.
4. Conclusion
To meet nitrogen generator purity standards, high-quality equipment is key—but daily operation details like air quality, sieve checks, and timely part replacement are just as vitalAs a professional gas equipment manufacturer, MINNUO has an experienced engineering team, and we welcome you to consult with us!