In the rapid progression of global industrialization, environmental issues have become increasingly prominent, particularly the severe challenges posed by global warming. In this context, the emergence of CO₂ Capture and Utilization (CCU) technology provides a new approach and direction for addressing environmental problems and promoting a green economic transformation.
Carbon dioxide capture and utilization technologies include amine adsorption, cryogenic separation, pressure swing adsorption (PSA), and membrane separation. Amine adsorption is used for capturing high-concentration CO₂, where the gas is absorbed by an amine solution and then released through heating for recovery. Cryogenic separation involves cooling CO₂ to a liquid or solid state to achieve separation and recovery. PSA leverages the adsorption characteristics of gases under varying pressures to separate CO₂ by adjusting the pressure. Membrane separation relies on the selective permeability of specialized membrane materials to separate CO₂ from other gases.
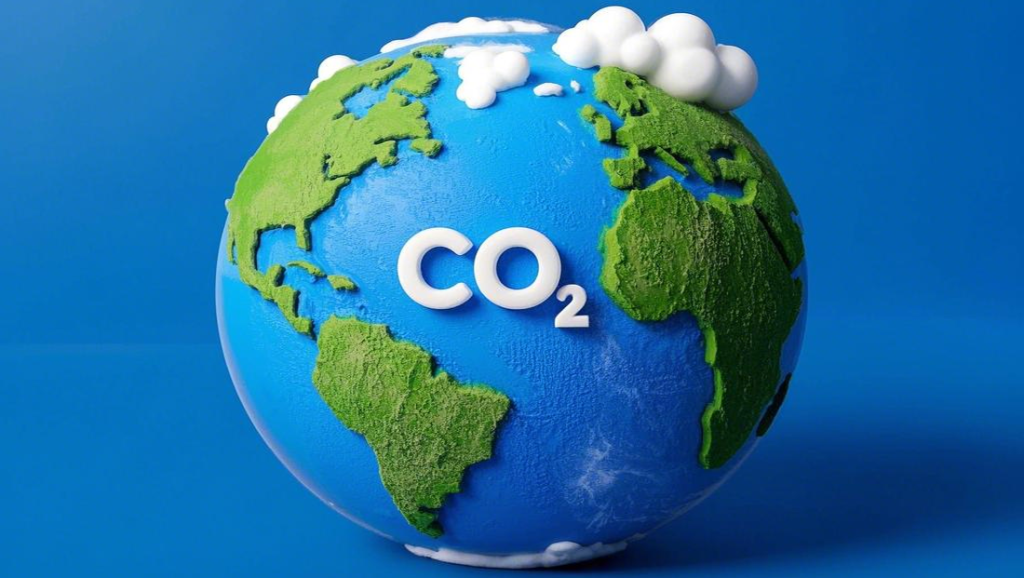
1. Background of CO₂ Capture and Utilization
In recent years, the trend of global warming has become more evident, with accelerated glacier melting, rising sea levels, and frequent extreme weather events, all of which seriously threaten human survival and development. Scientific research indicates that excessive CO₂ emissions are one of the main causes of global warming.According to data from the International Energy Agency (IEA), global carbon dioxide emissions reached 36.8 billion tons in 2022, of which industrial emissions accounted for more than 40%.
To combat climate change, the international community has reached a series of agreements, and countries have introduced strict carbon emission regulations. The European Union has implemented carbon taxes and carbon market trading mechanisms, imposing strict constraints on high-carbon-emitting enterprises and prompting them to seek effective emission reduction measures. China has also proposed the “Dual Carbon” goals, aiming to peak CO₂ emissions by 2030 and achieve carbon neutrality by 2060.
2. Benefits of CO₂ Capture and Utilization
(1) Economic Benefits
By capturing and utilizing CO₂, enterprises can avoid hefty fines for excessive emissions, thereby reducing their financial burden. Additionally, CO₂ has wide applications in the food and beverage industry, agriculture, and petroleum extraction. Enterprises can convert captured CO₂ into usable products, such as for carbonated beverage production, fertilizer manufacturing, and enhanced oil recovery, achieving resource reuse and creating additional revenue. Moreover, some regions offer subsidies and incentives to enterprises engaged in CO₂ capture and utilization, further enhancing economic benefits.
(2) Environmental Responsibility
Capturing and utilizing CO₂ can significantly reduce its direct emissions, mitigating atmospheric pollution and contributing to the alleviation of global warming. In today’s world, where the concept of sustainable development is deeply rooted, enterprises actively engaged in CO₂ capture and utilization are more likely to gain recognition and support from society, establishing a positive social image and enhancing their competitiveness.
3. CO₂ Capture Technologies
Currently, CO₂ capture technologies mainly include amine scrubbing and cryogenic separation.
(1) Amine Scrubbing
Amine scrubbing holds a significant position in the current field of CO₂ capture, especially suitable for industrial emission sources with high CO₂ concentrations.
A.Basic Principle
This method utilizes the chemical adsorption properties of amine solutions (such as monoethanolamine MEA) to react CO₂ molecules with the amine solution, forming stable carbamate compounds, thereby separating CO₂ from the mixed gas. Subsequently, by heating the amine solution, the carbamate decomposes, releasing high-purity CO₂ and allowing the amine solution to be recycled.
B.Technical Process
- Preliminary Filtration: Before the gas enters the adsorption stage, it is first passed through specialized filtration equipment to remove impurities such as sulfides and nitrides. These impurities not only affect the reaction efficiency between CO₂ and the amine solution but may also cause corrosion to subsequent equipment, making preliminary filtration a crucial step to ensure the smooth progress of the recovery process.
- CO₂ Adsorption: The preliminarily filtered gas enters the absorption tower, where it fully contacts the amine solution. Inside the absorption tower, CO₂ molecules react with amine molecules to form carbamate, achieving CO₂ capture.
- Solution Regeneration: The amine solution saturated with adsorption is transported to the regeneration tower, where heating causes the carbamate to decompose, releasing CO₂ and regenerating the amine solution, which can then return to the absorption tower to continue the adsorption process.
- Gas Compression and Storage: The CO₂ gas separated from the regeneration tower undergoes multi-stage compression to reach a suitable pressure state, facilitating storage and subsequent utilization. The compressed CO₂ can be transported via pipelines to storage facilities or directly to enterprises utilizing CO₂.
C.Technical Advantages
- High Capture Efficiency: For high-concentration CO₂ emission sources, amine scrubbing has high capture efficiency, effectively reducing enterprise carbon emissions.
- Strong Flexibility: This technology can be customized and optimized according to different enterprise production processes and exhaust emission characteristics, with strong adaptability and the ability to be flexibly integrated into existing production lines, minimizing the impact on normal production.
(2) Cryogenic Separation
Cryogenic separation has unique advantages in treating low-concentration CO₂ emission sources.
A.Basic Principle
This method utilizes the physical property changes of CO₂ at low temperatures, deeply cooling the mixed gas to below the critical temperature of CO₂, causing it to undergo a liquid phase change, thereby achieving separation from other gases.
B.Technical Process
- Pre-cooling: The mixed gas first enters a pre-cooling device, where it undergoes heat exchange with a cooling medium (such as liquid nitrogen, refrigeration cycle coolant, etc.), gradually lowering the temperature in preparation for subsequent deep liquefaction.
- Gas Liquefaction: The pre-cooled gas enters the low-temperature liquefaction unit, where at extremely low temperatures, the intermolecular forces of CO₂ strengthen, gradually condensing into a liquid state, achieving gas-liquid separation.
- Compression and Recovery: The separated liquid CO₂ is appropriately compressed according to actual needs to increase its pressure for storage, transportation, or direct use in other processes.
C.Technical Advantages
- High Separation Efficiency: For low-concentration CO₂ emission sources, cryogenic separation can achieve efficient separation and recovery, breaking through the efficiency bottleneck of traditional technologies under low-concentration conditions.
- High Purity: Due to the physical phase change separation principle, the liquid CO₂ produced by this technology has extremely high purity and low impurity content, suitable for fields with strict CO₂ purity requirements, such as food, electronics, and pharmaceuticals.
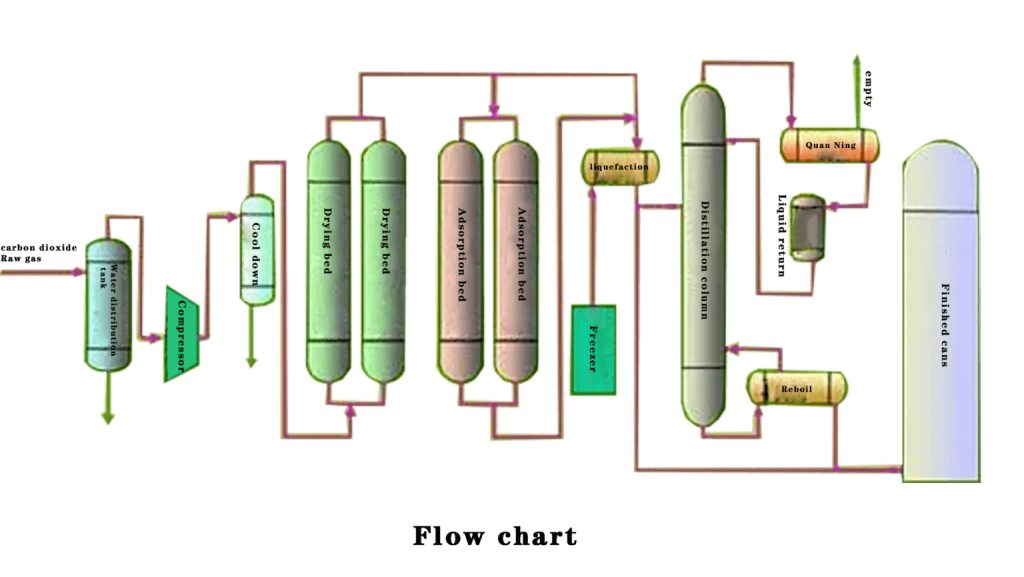
(3) PSA Adsorption
Pressure Swing Adsorption (PSA) is a gas separation technology based on the differential adsorption capacity of adsorbents for different gases under varying pressures.
A.Basic Principle
At higher pressures, the adsorbent exhibits a strong adsorption capacity for carbon dioxide (CO₂), allowing it to selectively adsorb CO₂ from a gas mixture while other gases pass through the adsorption bed and are discharged. Once the adsorbent becomes saturated, the pressure is reduced to desorb the CO₂ from the adsorbent, thereby regenerating the adsorbent for reuse.
B.Technical Process
- Pressurized Adsorption: The gas mixture enters the adsorption tower at a certain pressure. CO₂ is adsorbed by the adsorbent, while the unadsorbed gases are discharged as purified gas.
- Depressurized Desorption: After the adsorbent is saturated, the pressure in the adsorption tower is reduced to desorb the adsorbed CO₂, yielding a high-concentration CO₂ product gas. Desorption is typically achieved through pressure reduction or vacuum extraction.
- Cyclic Operation: Multiple adsorption towers alternate between adsorption and desorption processes to ensure continuous gas input and CO₂ product output.
C.Technical Advantages
- Low Energy Consumption: Compared to methods requiring significant energy for chemical reactions or refrigeration, PSA achieves adsorption and desorption through pressure changes, resulting in relatively low energy consumption.
- Simple Operation: The equipment structure is relatively simple, with a high degree of automation, making it easy to operate and maintain. It is suitable for CO₂ recovery needs of various scales.
(4) Membrane Separation
Membrane separation is a technology that utilizes specialized membrane materials to separate CO₂ based on the differences in permeation rates of different gas molecules.
A.Basic Principle
Driven by the pressure difference across the membrane, gas molecules in the mixture permeate through the membrane at different rates due to variations in size, shape, and chemical properties. CO₂ molecules permeate the membrane more quickly, while other gas molecules permeate more slowly, achieving the separation of CO₂ from other gases.
B.Technical Process
- Gas Separation: The gas mixture enters the membrane separation unit under pressure. CO₂ preferentially permeates through the membrane and becomes enriched on the other side, while the non-permeating gases are discharged as tail gas.
- Multi-Stage Separation: To improve the purity and recovery rate of CO₂, a multi-stage membrane separation process is typically employed. The CO₂-rich gas from the previous stage undergoes further separation to gradually increase its concentration.
C.Technical Advantages
- Compact Equipment: Membrane separation units have a small footprint and a compact structure, making them easy to integrate into existing industrial production systems. They also have relatively low investment costs.
- No Phase Change: The separation process does not involve phase changes, eliminating the need for additional heating or cooling, thereby reducing energy consumption and equipment complexity.
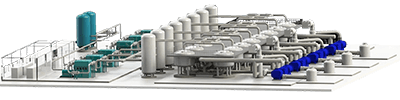
4. CO₂ Capture Equipment
CO₂ capture equipment is the core device for achieving CO₂ capture and utilization, and its performance directly affects the capture efficiency and utilization effectiveness. A complete set of CO₂ capture equipment typically integrates various technologies and devices to meet different capture needs.
(1) Amine Scrubbing-Based Recovery System
Primarily consists of an absorption tower, regeneration tower, heat exchangers, pumps, and valves. The absorption tower is the key equipment for CO2 adsorption, featuring an internal structure designed to ensure thorough gas-liquid contact and enhance adsorption efficiency. The regeneration tower is used for the regeneration of the amine solution and the release of CO2. Heat exchangers are employed to recover heat and reduce energy consumption. Pumps and valves control the flow of solutions and gases, ensuring stable operation of the entire recovery process.
- Main Applications: Primarily used in large industrial enterprises with high CO2 emissions, such as thermal power plants, cement factories, and steel mills. These facilities emit large volumes of exhaust gases with high CO2 concentrations, and the amine scrubbing recovery system can efficiently capture CO2, reducing carbon emissions.
(2) Cryogenic Separation-Based Recovery System
Main equipment includes precoolers, cryogenic liquefiers, distillation columns, and refrigeration units. The precooler initially cools the mixed gas, setting the stage for deeper liquefaction. The cryogenic liquefier turns CO2 into liquid at extremely low temperatures. The distillation column further purifies the liquid CO2, enhancing its purity. The refrigeration unit, crucial for providing the low-temperature environment, directly impacts the performance of the entire recovery system with its efficiency and stability.
- Main Applications: Suitable for industries requiring extremely high purity CO2, such as the food and beverage industry (for carbonated drink production), the electronics industry (for semiconductor manufacturing), and the pharmaceutical industry (as a raw material or protective gas in drug synthesis). Additionally, it is used in some natural gas purification plants to recover CO2 and remove impurities from natural gas.
(3) PSA Adsorption-Based Recovery System
Comprises multiple adsorption towers, valves, and a control system. The adsorption towers are filled with adsorbents, and valves regulate the gas flow and pressure changes. The control system coordinates the operations of the adsorption towers, facilitating the cyclic process of adsorption and desorption to ensure continuous and stable production of high-purity CO2.
- Main Applications: Ideal for small to medium-scale CO2 recovery scenarios, such as small chemical plants and breweries. These enterprises have relatively low exhaust emissions, and the PSA adsorption system, with its simple operation and low energy consumption, can flexibly adapt to their production scale and needs. It is also used in some distributed energy systems to recover CO2 generated during power generation.
(4) Membrane Separation-Based Recovery System
Core equipment includes membrane modules, along with supporting pressure pumps, flow meters, and control systems. Membrane modules can be categorized into flat sheet membranes and hollow fiber membranes based on different materials and structures. Pressure pumps provide the necessary pressure for gas permeation through the membranes, flow meters monitor gas flow rates, and the control system automates the entire membrane separation process to ensure stable and efficient separation.
- Main Applications: Commonly used in locations with high space constraints and the need for rapid deployment of recovery equipment, such as offshore drilling platforms and mobile recovery units. Additionally, in industrial processes with stringent energy consumption requirements, membrane separation systems offer advantages due to their phase-change-free operation and low energy consumption, such as in fine chemical production for CO2 recovery and separation.
To improve the performance of CO₂ capture equipment, MINNUO capture equipment adopts advanced automated control systems, enabling real-time monitoring and precise control of equipment operating parameters. At the same time, we continuously innovate in equipment material selection and manufacturing processes. Using corrosion-resistant, high-strength materials improves equipment reliability and service life. Additionally, we focus on modular design, facilitating installation, debugging, and maintenance, reducing enterprise operating costs.
5. Conclusion
CO₂ capture and utilization technology, as an important means to address global climate change, has broad development prospects and application value.
If you are interested in CO₂ capture and utilization or have related equipment needs, please feel free to contact MINNUO at any time. We have a professional technical team capable of providing comprehensive technical consultation and solutions, helping you take solid steps on the path to green development.