In modern industrial production systems, industrial oxygen generators are critical equipment widely used in metallurgy, chemical, medical, and many other fields, providing an indispensable source of oxygen for various production processes. However, any equipment may experience faults during long-term operation. Understanding common faults and their solutions is crucial for ensuring production continuity.
Common faults in industrial oxygen generators include insufficient oxygen concentration, abnormal oxygen output flow, compressor malfunctions, control system failures, frequent safety valve activation, insufficient air intake, and excessive equipment vibration. Solutions include timely replacement of molecular sieves, checking for pipeline leaks, calibrating oxygen analyzers, cleaning flow meters, inspecting compressor power and cooling issues, and more. Additionally, regular cleaning, maintenance of wear-prone parts, replacement of filters and lubricants, and ensuring a suitable operating environment can effectively extend equipment life and reduce fault occurrences.
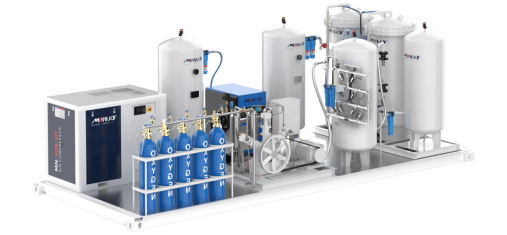
1. Common Faults and Solutions for MINNUO Industrial Oxygen Generators
1.1 Insufficient Oxygen Concentration
1.1.1 Phenomenon
Oxygen purity is found to be below industry standards (typically 90%, below which the concentration is considered insufficient), as detected by a professional oxygen concentration analyzer.
1.1.2 Causes and Solutions
(a) Molecular Sieve Failure
The molecular sieve is the core adsorption material of the oxygen generator, directly affecting oxygen purity. After prolonged use, the molecular sieve may gradually lose its adsorption capacity due to aging. Moreover, improper protection of the intake system, allowing moisture or oil to enter the molecular sieve bed, can rapidly destroy its adsorption structure, significantly reducing its efficiency.
Although MINNUO has implemented strict controls in both the selection of molecular sieves and the overall design of the equipment to achieve optimal performance and the longest service life, the working principle of the molecular sieve relies on a complex process of physical adsorption and desorption, which may be subtly affected by various external factors. For example, prolonged exposure to extreme humidity, the presence of special impurities in the treated gas, or operating conditions that exceed the rated parameters of the equipment may lead to molecular sieve failure.
In such cases, the molecular sieve should be replaced with one that meets the equipment specifications and performance requirements. During replacement, ensure that the sieve is packed evenly and tightly, following the equipment’s operating procedures to avoid gaps that could affect the adsorption efficiency. Additionally, regular pre-treatment of intake air, including the installation of efficient water and oil removal systems, is essential to extend the molecular sieve’s life. To further extend the sieve’s service life, MINNUO uses an adsorption-type dryer to reduce the air source dew point to -70°C, significantly reducing moisture in the air, paired with MINNUO’s exclusive CTAXH five-stage filtration system that effectively reduces oil and dust impurities.
(b) System Leakage or Abnormal Pressure
Long-term exposure of the oxygen system’s pipelines and valves to high-pressure conditions may cause leakage due to aging seals, corrosion, or mechanical vibration. Additionally, regulator valve malfunctions may lead to unstable system pressure, affecting the separation and purification of oxygen.
MINNUO ensures strict material selection for the pipes and valves, focusing on high sealing performance and durability. If a fault occurs, technicians should use professional leak detectors, such as a helium mass spectrometer, to thoroughly inspect the entire pipeline system and precisely locate the leak points. For leaking pipes or valves, seals or relevant components should be promptly replaced. When adjusting the regulator valve, use a high-precision pressure gauge to stabilize the system pressure at 0.04MPa, ensuring stability in the oxygen production process. Regular anti-corrosion treatments for pipes and valves and checking the tightness of connections are also necessary. All pipes and valves at MINNUO are made from 304 stainless steel to reduce purity degradation caused by pipe corrosion.
(c) Solenoid Valve / Pneumatic Valve Malfunction
In pressure swing adsorption oxygen production processes, the alternating operation of the A/B towers relies on precise control by solenoid or pneumatic valves. If the valve core wears out, gets stuck, or if the solenoid coil burns out or the air circuit becomes blocked, the A/B towers may fail to switch properly, affecting oxygen concentration.
MINNUO’s oxygen generators undergo strict valve quality testing to ensure reliability. During routine maintenance, technicians can use a professional resistance measuring instrument to check the solenoid valve’s resistance (normally around 132Ω) to determine if the solenoid coil is functioning. For pneumatic valves, the air circuit connections should be checked for looseness, air source pressure should be verified, and the air circuit should be cleared of impurities and moisture. Severely damaged valves should be replaced with the same model and specification. Regular valve maintenance, including proper lubrication to prevent rust and wear, is also recommended.
(d) Oxygen Analyzer Error
As a critical device for monitoring oxygen concentration, the accuracy of the oxygen analyzer is essential. Over time, the oxygen electrode may experience measurement errors due to aging or contamination.
The oxygen analyzer provided is of high precision and stability but requires regular calibration. The solution is to periodically calibrate the analyzer using a standard oxygen cylinder to ensure accurate readings. If the oxygen electrode is severely damaged, it should be replaced with a new one and recalibrated. Additionally, ensure that sample gas flows smoothly and accurately into the detection device to avoid measurement errors caused by clogged or leaking gas lines. The analyzer should be placed in an appropriate environment, avoiding high temperatures or humidity that may affect its performance.
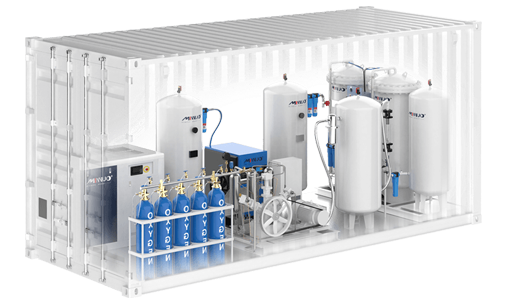
1.2 Abnormal Oxygen Output Flow
1.2.1 Phenomenon
The flowmeter’s float is either stationary or the displayed flow is significantly lower than the rated flow.
1.2.2 Causes and Solutions
(a) Flowmeter Failure
The flowmeter’s adjustment knob may become stuck due to prolonged use, rendering the flow regulation ineffective. Additionally, internal sensors or mechanical parts of the flowmeter may be damaged, affecting the accuracy of the flow readings.MINNUO selects flowmeters from suppliers known for their exceptional quality control, ensuring they perform reliably and stably under strict performance tests, providing accurate and stable flow measurements for numerous clients.
However, due to the complexity of industrial environments, factors such as extreme temperature changes, abnormal pressure fluctuations, and improper installation or operation can affect the flowmeter’s performance. If the flowmeter malfunctions, technicians should first check the knob’s flexibility. If it is stuck, lubricate it with an appropriate amount of lubricant. If the flowmeter is damaged, replace it with one of the same precision and range, and calibrate and adjust it after installation. Regular cleaning and maintenance of the flowmeter are also necessary to prevent internal contaminants from affecting its performance.
(b) Pipeline Blockage or Leakage
The oxygen generator’s supply air pipeline may become blocked or leak due to the accumulation of impurities, freezing, or mechanical damage. MINNUO oxygen generators are designed with high-quality 304 stainless steel pipelines, providing excellent resistance to clogging and leakage, and demonstrating superior performance in various practical applications.
However, the operating environment of the oxygen generator can vary greatly. Factors such as high levels of gas impurities, extreme temperature or humidity changes, or improper operation by untrained personnel may place additional stress on the pipeline system. Technicians should inspect the supply air pipeline thoroughly, using tools such as pipe endoscopes and pressure testing devices. Blocked pipelines can be cleared using high-pressure gas purging or chemical cleaning methods. For leaking pipelines, repair leaks promptly and replace damaged pipes or seals. In colder regions, heat insulation should be applied to prevent freezing.
(c) Regulator Valve Abnormalities
Regulator valve malfunctions can lead to unstable system pressure, affecting oxygen output flow.
In most cases, MINNUO’s regulator valves perform excellently due to advanced technology and strict manufacturing processes. However, industrial environments are complex and dynamic, and factors like extreme operating conditions or unforeseen events may affect valve performance. Operators should use high-precision pressure gauges to monitor the system pressure in real time, adjusting the regulator valve slowly to stabilize the pressure at 0.04MPa, ensuring consistent oxygen output. Regular calibration and maintenance of the regulator valve are also essential for reliable performance.
1.3 Compressor Operation Abnormalities
1.3.1 Phenomenon
The compressor fails to start, produces excessive noise during operation, or automatically shuts down due to overheating.
1.3.2 Causes and Solutions
(a) Power Supply Issues
Check whether the power socket is loose or not making proper contact, if the fuse is blown, or if the power line is damaged or short-circuited. Use a multimeter to check if the supply voltage is normal. If the voltage deviates from the equipment’s allowable range, contact the power supply department for repairs. For loose sockets, tighten them; replace any blown fuses with the correct specifications; and replace any damaged power cables. Ensure the power supply capacity meets the compressor’s power requirements to avoid overloading the circuit.
(b) Compressor Damage
If the starting capacitor is normal (check with a capacitor tester) but the compressor still fails to start, internal mechanical components such as the rotor or bearings may be damaged. MINNUO selects compressors from high-quality suppliers that undergo strict quality control, ensuring stable and reliable performance.
However, over time, mechanical components may wear out due to factors like the operating environment, running time, and adherence to operational standards. If such issues occur, it’s recommended to contact a professional technician. They will disassemble and inspect the compressor in detail, identify damaged components, and replace them with original or reliable replacement parts, following proper assembly procedures. Regular maintenance, including oil changes and belt tension checks, is also important.
(c) Poor Heat Dissipation
Compressors generate substantial heat during operation. If the heat dissipation system fails, the compressor may overheat and shut down. In MINNUO’s design and manufacturing process, the importance of heat dissipation was fully considered, and an efficient heat dissipation system has been carefully tested and optimized to ensure the oxygen generator remains within the ideal temperature range.
However, the system’s cooling efficiency may be influenced by various external factors, such as placing the machine in poorly ventilated spaces, surrounding high temperatures, or continuous operation without proper maintenance. Technicians should check if the axial fan is functioning, the fan blades are undamaged, and if dust or debris is clogging the cooling system. Regular cleaning of the heat exchanger and ensuring proper airflow is essential. MINNUO also considers site conditions when selecting auxiliary cooling devices such as cooling fans or water cooling systems to enhance heat dissipation. Regular checks of the coolant levels and quality should also be performed.
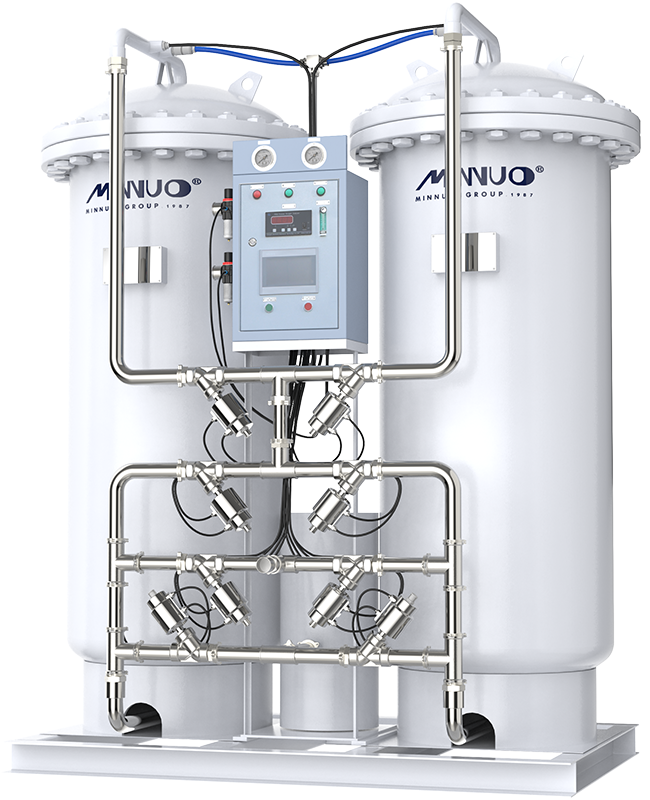
1.4 Control System Failure
1.4.1 Symptoms
The indicator lights on the equipment control panel flicker abnormally or display error codes (such as “H.P.” indicating high-pressure alarm, “L.P.” indicating low-pressure alarm), and the equipment cannot automatically switch between working states as per the preset program.
1.4.2 Causes and Solutions
(a) Damaged Control Board
The control board is the core component of the oxygen generator’s control system, and its failure can lead to a malfunction of the equipment. Use professional circuit board testing instruments to check the voltage at the valve socket (it should be DC12V during normal switching). If no voltage output is detected, the control board may be faulty, such as damage to electronic components or a short circuit on the board.
MINNUO’s control boards are rigorously tested for strong stability. Technicians should perform detailed checks on the control board using the circuit diagram, replacing damaged components like resistors, capacitors, and integrated circuits. If the control board is severely damaged and cannot be repaired, it should be promptly replaced with a new control board of the same model, followed by programming and debugging. Additionally, regular cleaning and maintenance of the control board should be carried out to prevent damage caused by dust and moisture.
(b) Sensor Failure
The oxygen concentration sensor and pressure sensor are key components for the control system to obtain operational parameters. If these sensors fail, the control system may misinterpret the data.
MINNUO uses high-precision sensors with high accuracy and reliability. Use standard gases to calibrate the oxygen concentration sensor and check its response time and measurement accuracy. For the pressure sensor, use a pressure calibration device for calibration and testing. If a sensor is damaged, it should be replaced with a new one, and recalibration and debugging should be performed to ensure the accuracy and reliability of the sensor data. Additionally, sensors should be protected from severe vibrations and electromagnetic interference.
1.5 Frequent Activation of Safety Valve or High System Pressure
1.5.1 Symptoms
The safety valve frequently vents, emitting a regular alarm sound, while the system pressure exceeds the normal operating range.
1.5.2 Causes and Solutions
(a) System Blockage
Parts of the oxygen generation system, such as the radiator and adsorption tower, may become blocked due to accumulated impurities or crystallization, causing the system pressure to rise.
MINNUO oxygen generators are designed with anti-blockage considerations, but regular maintenance is still required. Use professional cleaning equipment to thoroughly clean the radiator and adsorption tower, removing impurities and blockages. When cleaning, choose appropriate cleaning agents and methods to avoid damaging the equipment. Additionally, regularly discharge and clean the system to prevent impurity buildup.
(b) Safety Valve Setpoint Deviation
The set pressure value of the safety valve may deviate due to prolonged use or incorrect operation, causing the valve to activate frequently even when the system pressure has not reached a dangerous level.
Use professional pressure adjustment tools, following the equipment operating procedures, to adjust the safety valve’s activation pressure to 0.25MPa. If the safety valve is damaged or cannot be properly adjusted, replace it with a qualified valve that meets national standards and equipment requirements, and perform pressure calibration and adjustment after replacement. Additionally, avoid arbitrarily adjusting or disassembling the safety valve.
1.6 Insufficient Inlet Air
1.6.1 Symptoms
The amount of air output by the air compressor cannot meet the oxygen generator’s requirements, leading to reduced oxygen production efficiency.
1.6.2 Causes and Solutions
The air compressor may have faults, such as rotor wear or inlet valve blockages. The compressor should be repaired and maintained, with worn parts replaced and the inlet valve cleaned. Also, if the inlet pipeline is blocked or leaking, it should be inspected and repaired.
MINNUO oxygen generators are designed with optimized air flow channels to reduce inlet resistance, but regular inspections and maintenance are still necessary.
1.7 Excessive Vibration of Oxygen Generator
1.7.1 Symptoms
The equipment generates strong vibrations during operation, affecting its stability and service life.
1.7.2 Causes and Solutions
The compressor foundation is unstable and needs reinforcement; internal components of the equipment, such as loose bolts, should be checked and tightened; rotating parts, such as rotor bearings, are unbalanced and should undergo dynamic balancing correction.
We pay great attention to the stability and balance of the equipment during the production of our oxygen generators, but the vibration situation should still be monitored during daily use.
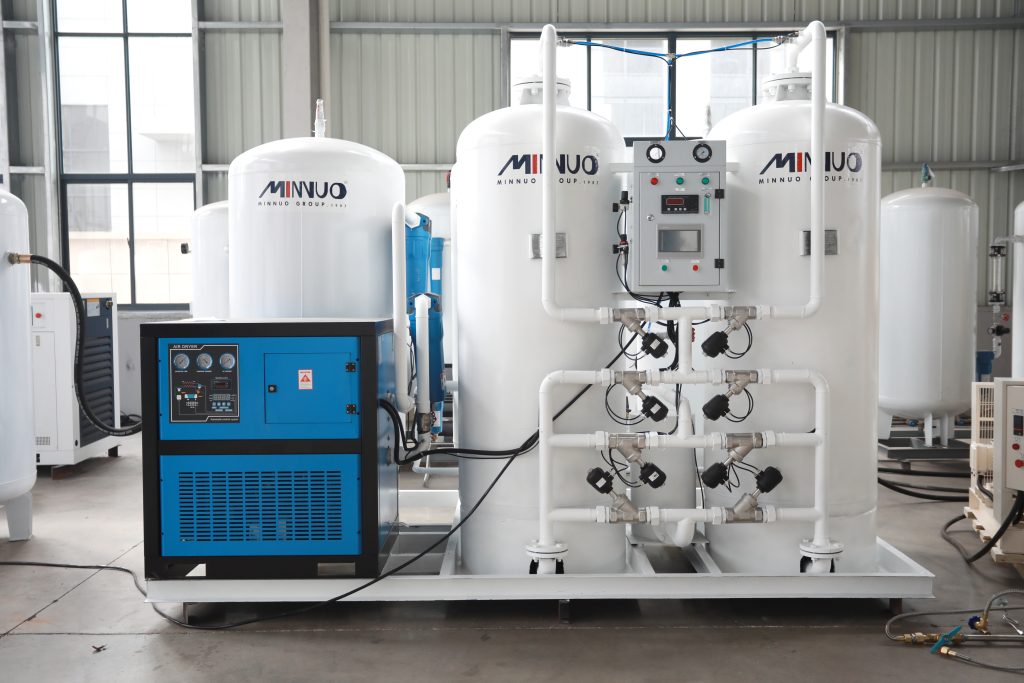
2. MINNUO Diagnostic and Maintenance Recommendations
2.1 Fault Diagnosis Methods
2.1.1 Initial Inspection
Technicians should observe control panel indicators, listen for abnormal noises, and check equipment temperature. For example, flashing indicators may indicate control system faults, while abnormal noises may point to compressor or mechanical issues. Overheating may suggest cooling system problems. Consult operators for pre-fault operation details. MINNUO provides detailed troubleshooting manuals for quick issue identification.
2.1.2 Instrument Assistance
Use professional tools like multimeters, capacitor testers, resistance meters, pressure gauges, leak detectors, and borescopes for detailed inspections. Utilize built-in diagnostic systems for additional fault information. MINNUO’s diagnostic systems are intelligent, offering quick and accurate fault diagnosis.
2.2 Preventive Maintenance Measures
2.2.1 Regular Cleaning
Clean air filters weekly with compressed air or specialized tools. Inspect molecular sieves monthly for discoloration or clumping, and perform activation or replacement as needed. Regularly clean internal components to prevent dust and oil buildup. MINNUO provides detailed maintenance plans.
2.2.2 Replacement of Wear-Prone Parts
Replace air filters every three months. Molecular sieves typically last 2-3 years; replace them based on operating conditions. Regularly replace compressor lubricants, belts, and seals. MINNUO offers original high-quality parts for optimal performance.
2.2.3 Environmental Management
Install oxygen generators in dry, well-ventilated areas, avoiding high temperatures, humidity, and dust. Set up protective measures to prevent collisions. Maintain clean surroundings for easy maintenance. MINNUO provides environmental assessments and recommendations during installation.
2.3 Emergency Handling
2.3.1 Overheating or Alarms
Press the emergency stop button immediately, cut power, and allow the equipment to cool. Inspect cooling system components like fans and heat exchangers. Record fault details for analysis. MINNUO’s service team is available for remote or on-site support.
2.3.2 Power Failures
Cut power immediately and inspect power lines, sockets, and fuses with insulated tools. Avoid live operations until faults are resolved. Use backup power or oxygen generators if downtime is prolonged. MINNUO offers backup power solutions for production continuity.
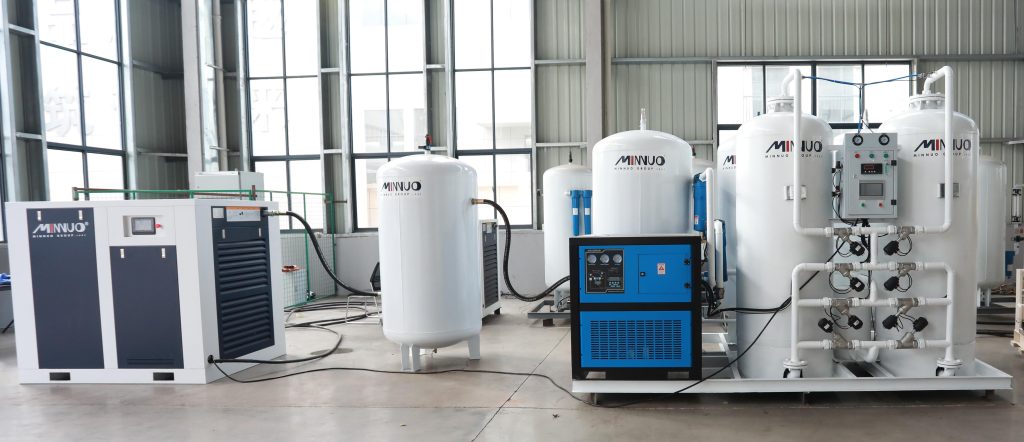
3.Conclusion
Industrial oxygen generators face various faults due to component aging, improper operation, inadequate maintenance, and environmental factors. By following standardized procedures, regular maintenance, and scientific fault diagnosis, fault rates can be reduced, enhancing equipment stability and reliability.
MINNUO industrial oxygen generators excel in stability and reliability, thanks to advanced technology, high-quality materials, and rigorous quality control. Contact us for more information!