In the food packaging industry, maintaining product freshness, preventing microbial contamination, and extending shelf life are not just desirable—they’re mandatory. Modern packaging lines must meet increasingly strict standards for anti-oxidation, anti-corrosion, and explosion protection, especially in the handling of oily, powdered, or perishable products.
Nitrogen plays a critical role as an inert protective gas in food production. By replacing reactive oxygen in packaging, nitrogen helps slow spoilage, inhibit mold or bacteria growth, and prevent package collapse due to vacuum loss. It is also essential for preventing fires or dust explosions in facilities that handle fine particles or high-risk ingredients.
This article explores how industrial nitrogen generators—especially PSA-based on-site systems—serve as a stable and controllable nitrogen source for packaging environments. We’ll explain their working principles, safety-enhancing features, and application cases, helping food manufacturers understand why these systems are increasingly seen as must-have infrastructure for a safe, efficient, and compliant production line.
I. The Central Role of Nitrogen in Food Packaging
The primary objectives of food packaging are to extend shelf-life, ensure product hygiene and safety, and prevent the risk of ingredient spoilage or explosiveness. As an inert gas, nitrogen is widely used in a variety of packaging scenarios due to its chemical stability, colorless, odorless and non-toxic properties. Its core role is mainly reflected in the following aspects:
1. Inhibit oxidation reaction and prolong shelf life
Most food products will undergo oxidation reaction after being exposed to air, especially products containing oils and fats, vitamins, and nuts, which are highly susceptible to hallucinogenic taste or nutrient loss.
✅ Nitrogen replacement packaging can effectively drive out oxygen, forming a low-oxygen or oxygen-free environment to prevent oxidation of fats and oils, discoloration and flavor changes.
Case in point: the residual oxygen in canned nuts is reduced from 18% to 1%, and the shelf life is extended for more than 3 months.
2. Inhibit the growth of microorganisms (e.g. mold, bacteria)
The reproduction of microorganisms depends on oxygen, especially aerobic bacteria such as Salmonella, E. coli, etc., the more oxygen the faster their reproduction.
Nitrogen encapsulation can reduce the residual oxygen to <1%, forming an anti-bacterial environment, which can effectively improve the microbiological safety of food in combination with the cold chain. 3.
3. Filling gas for Modified Atmosphere Packaging (MAP)
MAP (Modified Atmosphere Packaging) is one of the core technologies for modern food preservation.
Nitrogen is often used in combination with carbon dioxide and oxygen, for example:
Bread: 60% nitrogen + 40% carbon dioxide
Bakery cake: 99% nitrogen (to maintain the fluffy structure)
Cooked food: 70% nitrogen + 30% CO₂ (to slow down the rotting)
⏩ Nitrogen’s inertness guarantees the stability of the overall gas-conditioning system, to avoid the “gas-phase inequality Avoiding “uneven gas phase” triggering condensation or collapse.
4. Protective gas for frying and powder products
such as puffed food, seasoning powder, protein powder, etc. Residual oxygen content in the package is controlled to <3%, which can significantly reduce:
caking, moisture problems
grease rancidity and flavor
risk of static adsorption contamination
Technology extension: Nitrogen can be used as a conveying gas to provide an inert environment for the automatic filling and weighing system of powder material. 5.
5. Explosion-proof protective gas layer for food products with explosive dust or alcohol
Certain food products such as flavors, wine heart candies, powdered drinks contain alcohol or fine dust, which has the risk of ignition and explosion if exposed to high temperature/electrical sparks.
The use of nitrogen as a filling gas in the canning or mixing process can isolate the air and the ignition source, and significantly improve the intrinsic safety of the production line.
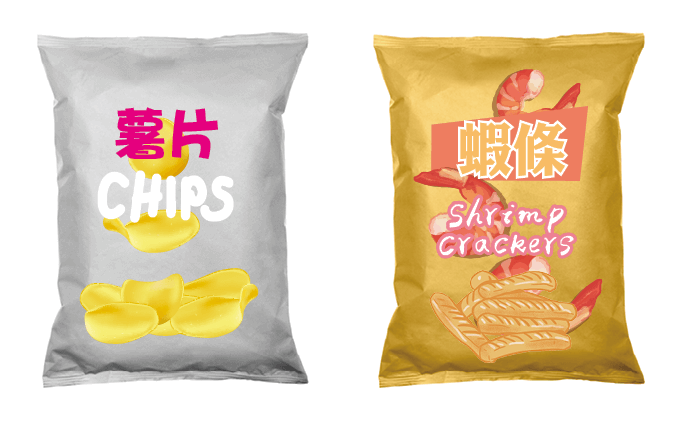
II. How Industrial Nitrogen Generators Work
Industrial nitrogen generator is a kind of equipment system that realizes continuous and automated nitrogen supply by selectively separating nitrogen and oxygen components in the air. Its core technology is divided into two categories: PSA (Pressure Swing Adsorption) and Membrane Separation, which is widely used in food, medicine, electronics, metal processing and other scenarios requiring high purity and stability of nitrogen.
1. Brief introduction of technology types
✅ PSA (Pressure Swing Adsorption)
Principle: Utilizing carbon molecular sieve (CMS) with different adsorption capacities for oxygen and nitrogen molecules under different pressures to realize nitrogen separation.
The process is divided into two towers running alternately: one tower adsorbs oxygen, the other desorbs and regenerates, realizing continuous nitrogen supply.
System features: mature structure, stable operation, nitrogen purity **95%~99.999%** range adjustment.
✅ Membrane Separation Technolog
Principle: Separation of different gases with the help of hollow fiber membrane on the difference of diffusion speed, nitrogen passes slowly, oxygen passes quickly.
Suitable for small, low purity requirements (90% ~ 99%) of the scene.
Advantages: fast startup, small footprint, suitable for portable or mobile systems.
2. Suitability of Nitrogen Purity Range and Food Packaging
According to the actual needs of the food packaging industry, nitrogen purity is usually categorized into the following levels:
Nitrogen purity | Suitable Applications |
95% | Modified Atmosphere Packaging (MAP), General Snacks, Beverage Can Sealing |
99% | Oxidizable Products (e.g. Nuts, Vegetable Oils), Bakery Products Freshness |
99.9%+ | Fermented Products, Precision Powders, High-end Freeze-Dried Foods, Export Grade |
Industrial PSA systems can usually achieve customized nitrogen purity output by adjusting the adsorption/regeneration cycle, pressure setting and carbon molecular sieve filling amount, and monitor the stability in real time through online nitrogen analyzer to guarantee the food quality.
3. Advantages Compared with Liquid Nitrogen or Bottled Nitrogen
Compared with traditional liquid nitrogen/bottled nitrogen distribution, industrial nitrogen generator has the following significant advantages in food packaging production line:
Comparison Items | Industrial Nitrogen Generator | Liquid Nitrogen/Bottled Nitrogen |
Gas Sources | Self-produced and self-supplied, stable output | Sourced externally, subject to transportation and weather |
Safety | No high-pressure storage, operating pressure lower than 0.6MPa | Liquid Nitrogen is extremely cold, and bottles are prone to explosions at high pressures |
Cost Structure | Low long-term operating cost after initial investment | High cycle cost of distribution, high fluctuations in annual costs |
O&M Efficiency | Remote monitoring, automatic pressure and purity adjustment | Frequent bottle changes, manual control required |
✅ Safety Emphasis: The use of nitrogen generator in food workshop can avoid the potential accidents caused by mechanical shock, leakage or wrong access to air brought about by the handling of high-pressure cylinders, and improve the overall safety level of the production environment.
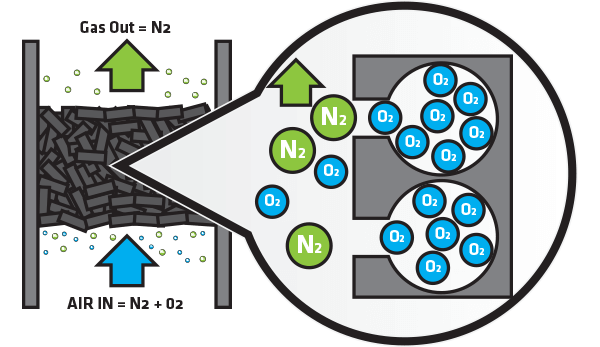
III. How They Improve Packaging Line Safety
Food packaging not only requires product freshness, but also must ensure a high degree of safety in the production line operation process itself. The intervention of industrial nitrogen generator in this process not only provides nitrogen, but also systematically reduces the safety risk, improves the control ability and personnel health protection level through the intelligent gas supply system in many aspects.
1. Eliminate the risk of transportation of high-pressure gas cylinders
Hidden dangers of traditional mode:
Liquid nitrogen or high-pressure nitrogen cylinders in the handling, storage and use of the process of explosion, leakage, pouring tanks and other safety hazards. Especially in high temperature and multi-personnel workplaces, the rupture of high-pressure containers or wrong access will cause serious accidents.
Advantages of industrial nitrogen system:
No need to transport high-pressure cylinders, gas supply is completed within the system
Operating pressure is generally 0.3~0.6MPa, which belongs to the range of low and medium pressure
Adopting fixed mounting structure greatly reduces the risk of leakage of equipment joints and incorrect operation caused by the replacement of cylinders
✅ Applicable to the pursuit of “cylinder-free” modern food factories or intelligent packaging workshops
2. Reducing Oxygen Residue, Reducing the Risk of Product Degradation
Source:
Oxygen is the main factor leading to food oxidation, flavor change and spoilage. During the traditional nitrogen filling process, if the nitrogen concentration is not stable or the system is not switched in time, it is very easy to retain oxygen, which leads to preservation problems.
Industrial nitrogen system solution:
Nitrogen continuous and stable output, avoiding filling fluctuations
Built-in online oxygen analyzer, real-time detection of oxygen residue, to ensure that the purity of filling gas above the set value
Effective oxygen removal, to maintain the oxygen content of the filling chamber <1%, to extend the shelf life of the product
Example of application: ready-to-eat cooked food, nuts, vegetable oil packaging workshop
3. Reduce the risk of flammability and improve the level of explosion-proof
Certain food products contain high fats, alcohols or powders, which is the main factor for the oxidation and spoilage in the confinement of the food products, Some food products contain high fat, alcohol or powder, which may react violently with oxygen or even explode during airtight inflation or transportation. Such as milk powder, coffee powder, flavors and fragrances in the production process, once the control of oxygen concentration is not good, it will form a potentially explosive atmosphere.
Application Countermeasures:
Nitrogen inert gas characteristics, in the packaging, handling, storage links to play the role of oxygen and explosion-proof
Industrial nitrogen generator can adjust the rate of gas supply, to achieve slow charging, micro-positive pressure filling, to prevent dust and improve the uniformity of filling
Alternative to the compressed air filling method, significantly improve the overall fire and explosion-proof level of the production line
4. Enhance the automation control and alarm capabilities
Modern packaging line has changed from the “manned guard type” to the “manned guard type”. Modern packaging lines have transformed from “manned” to “data-driven”, and the automated nitrogen system is the key support for improving the overall safety perception and response efficiency.
System Integration Advantages:
Full-link monitoring of nitrogen flow, purity, pressure, and oxygen content
PLC + human-machine interface (HMI) control interface, real-time alarms and linkage of nitrogen host start/stop
Immediate audible and visual alarms at preset limit values (e.g., oxygen concentration >2%) for quick problem identification
Suggestion: Match with temperature and humidity, seal integrity monitoring, and end-gas quality feedback device to build a multi-dimensional gas safety control system
5. Safeguard Staff operation safety
Human safety prevention and control should not be ignored. Traditional high-pressure gas cylinders need to be operated close to the device frequently, and the cylinder is susceptible to impact, slipping, dumping and other impacts, which directly threaten the safety of operators.
Advantages of industrial nitrogen system:
Remote monitoring and control, no need to change the bottle manually
No risk of accidents such as cold burns, high-pressure spraying, falling bottle and so on.
IV. Case Study: Industrial Impact
Case Study: Industrial Impact
Through the following real cases, we can clearly see the specific application value of industrial nitrogen generator in food production line, from oxidation control, cost optimization, shelf-life extension to fire risk prevention and control, which comprehensively reflects its role in the triple objective of “safety + quality + benefit”. It fully reflects its practical role in the triple objective of “safety + quality + efficiency”.
Case 1: Potato Chip Company Imported PSA Nitrogen System, Significantly Reducing Product Oxidation Risks
Background:
A large puffed food factory originally used bottled nitrogen for potato chip packaging, but the frequent replacement of cylinders under high-speed production lines affected efficiency and caused large fluctuations in oxygen residue.
System Deployment:
Introduced a 30Nm³/h PSA nitrogen generator
Equipped with a purity analyzer, flow regulating valve, and PLC linkage control
Docked with the packaging machine automation interface to achieve accurate nitrogen filling and residual oxygen control
Improvement Results:
The average value of oxygen residue in packaging was reduced from 3.8% to 2.1%, and the oxidation rate dropped by 30%.
Due to the reduced frequency of nitrogen replacement in bottles and the reduction of manual duty, the monthly operating cost saved is about 20%. Promotion Suggestion: Applicable to medium and high speed potato, puffed and nut packaging lines
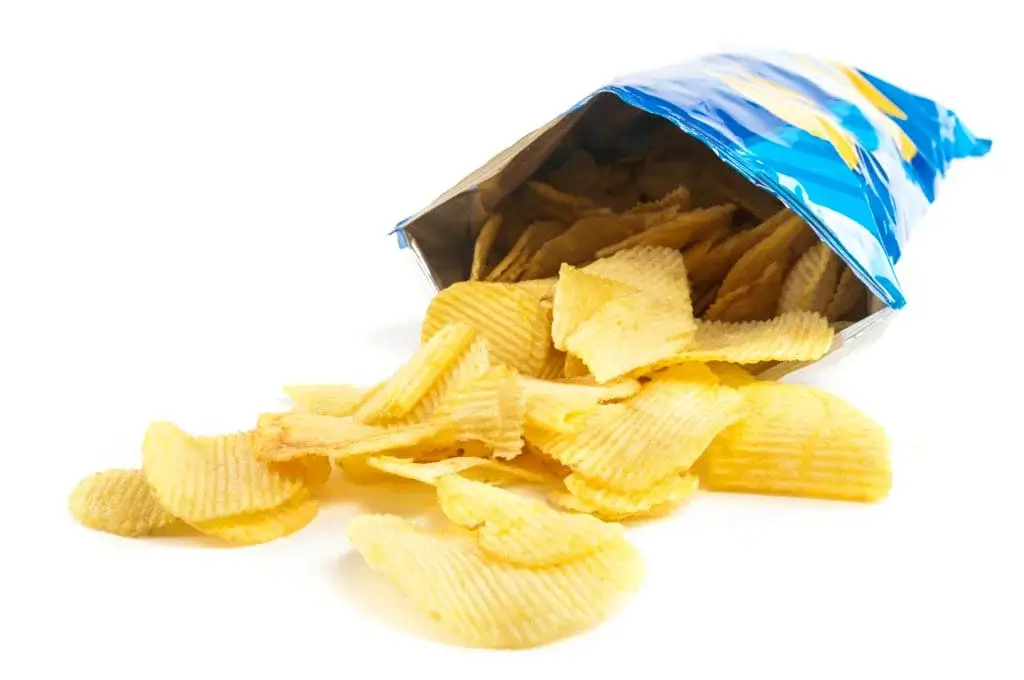
Case 2: Optimize gas management in kiwifruit gas-conditioned preservation center to extend shelf life and reduce loss
Scenario:
Fruit and vegetable wholesalers’ cold-chain distribution warehouses, where kiwifruit is prone to ripening prematurely due to high oxygen content during transportation, affecting the taste of the end-retailer and the wastage rate.
Solution:
Deploy 15Nm³/h PSA nitrogen units + air-conditioned cling film nitrogen filling system
Control the oxygen content in the storage area to maintain it at 2%-3%, and monitor CO₂ and humidity in real time at the same time.
Improvement effect:
Kiwifruit’s transportation wastage rate is reduced by more than 60%, from 8.6% to 3.4%.
Shelf-life is extended by 3-4 weeks on average, which improves customer satisfaction.
Suggestions for promotion: High-value-added fruits such as fresh fruits, avocado, blueberry, strawberry, and so on. Promotion Suggestion: Fresh fruits, avocados, blueberries, strawberries and other high value-added fruits can refer to this configuration
Case 3: Alcoholic fruit-flavored beverage filling line through the nitrogen system to achieve explosion-proof upgrades
Background:
The beverage factory packaged fruit-flavored beverages contain a certain amount of alcohol, and the sugar content is high, belonging to highly inflammable and easy to oxidize materials, according to the new safety standards need to improve the explosion-proof measures.
System Deployment:
Continuous nitrogen filling in the filling head and liquid storage tank headspace to maintain an inert atmosphere.
Linkage with the overall gas monitoring system in the workshop to realize the purity alarm and automatic switching of nitrogen source.
Implementation Results:
Oxygen concentration is controlled in real time at less than 3%, and the evaporation of alcohol is significantly slowed down.
Explosion-proof level of the workshop has been upgraded from the original Zone 2 to Zone 1, which is in line with the new version of the safety auditing standards.
Applicable Industries: Fruit juice, flavors and fragrances, and protein drinks, which require anti-oxygenation, Liquid packaging lines that require oxygen and explosion protection.
Indicator Dimension | Average Improvement Results | Processes Involved | Technology |
Oxidation Control | 30~45% reduction in residual oxygen | Air-conditioned Packaging | PSA + Oxygen Analyzer |
Shelf Life Extension | Extension of 3~4 weeks | Fruit and Vegetable Refrigeration | Regulated Nitrogen Supply + Micro Oxygen Environment |
Safety Level Enhancement | Improvement of the overall explosion protection level of the plant by one grade | Packaging of Alcohol-containing Materials | Inert Protection + Online Alarms |
V. System Selection Suggestions and Configuration Strategies
System Design & Safety Optimization Tips
In order to ensure the efficient and safe operation of the food packaging line in the process of nitrogen preservation, anti-oxidation, explosion control, etc., the enterprises need to fully consider the following four aspects when selecting the industrial nitrogen generator:
1 Recommended Nitrogen Purity Standards
According to the sensitivity of food categories and the demand for anti-oxidation, it is recommended to match the following purity levels. According to the sensitivity of the food category and the demand of anti-oxidation, it is recommended to match the following purity level:
Type of application | Recommended Nitrogen Purity Range | Package Suggestions |
General food packaging (cookies, chips) | ≥99% | PSA Standard Model |
High fat/high water activity food | ≥99.5%~99.99% | Precision PSA High Purity Module |
Alcoholic beverages/explosive powder protection | ≥99.99 | Dual Stage Fine Extraction, Purity Monitoring Recommended |
✅ Note: Nitrogen purity is directly related to residual oxygen control, the higher the purity, the lower the residual oxygen, the lower the risk of microbial growth and fat oxidation.
2 Gas Output Pressure Matching
Recommended output pressure range: 0.2-0.6 MPa, adapting to the following different gas consumption scenarios:
0.2-0.3 MPa: Suitable for gas-regulated packaging MAP filling, nitrogen filling of inner bags.
0.4-0.5 MPa: suitable for medium-sized continuous packaging line or multi-station synchronized gas supply
≥0.6 MPa: suitable for workshop layout that requires medium and long-distance delivery of nitrogen (can be matched with pressure regulating valve)
It is recommended to match with buffer tank (≥100L) to absorb load fluctuations and avoid impact drift of residual oxygen.
3 Key Supporting System Suggestions
In order to ensure stable operation, safety and reliability of the nitrogen system, the following components should be configured:
On-line Oxygen Purity Analyzer (>24 hours real-time monitoring)
→ Installed in the outlet pipeline to ensure that the residual oxygen of each batch of products is controlled within the standard
Oxygen Buffer Tank + Safety Valve Reducing Valve Set
→ Pressure stabilizing flow rate, protection of downstream equipments
Safety Pressure Unloading Valve, Check Valve, Blow-back Circuit Design
→ Preventing back-up, adapting to the Shutdown protection
PLC control module linked with packaging line
→ Realize “start-up is gas supply, shutdown is gas stop”, reduce waste
✅ For automatic high-speed line, it is recommended to deploy remote communication interface to realize the integration of the gas source system and the production line system regulation and control.
4 Multi-point gas supply station (applicable to assembly line or composite packaging plant)
If there are multiple packaging stations, different product lines, or independent workstations in the factory, it is recommended to adopt:
Branch pipeline network + manifolds supplying gas in separate zones: set up pressure reducing and stabilizing modules in zones, and independently regulate the air pressure of different workstations
Loop pipeline structure + parallel branch: avoid the fluctuation of the air consumption of a workstation affecting the whole situation
Main station + branch configuration (mother and child type) Centralized nitrogen production at the main station and buffer relay unit at the branch station, which can expand the radius of gas supply as needed.
Application Scenario: Food enterprises have multiple packaging lines, bottle blowing lines, beverage filling lines and other shared nitrogen, and it is recommended to adopt the “Centralized Nitrogen Production + Multi-point Gas Distribution” program to avoid repeated purchases and waste of energy consumption.
✅ Summary of configuration strategy
Configuration Dimensions | Suggested Options | Practical value |
Nitrogen Purity | 99-99.99% (depending on category) | Ensure the effect of oxygen suppression and prolong the shelf life |
Output Pressure | 0.2-0.6 MPa | Match with different packaging nitrogen filling stations |
Safety and Monitoring Components | Purity analyzer + buffer tanks + safety valves, etc. | Ensure the stability of operation and safety of personnel and equipment |
Automation | PLC module for linkage to packaging line | Reduce energy consumption and improve the operational efficiency |
Multi-station Solutions | Zoned gas supply + piping loop + auxiliary and main systems | Meet the needs of flexible deployment and scale expansion |
VI. Economic and Long-Term Value Analysis
Cost Efficiency and Long-Term Value
In the food packaging industry, nitrogen is not only an auxiliary gas for production, but also an important factor that directly affects freshness cycle, product quality, brand reputation and export standards. The decision to purchase an industrial nitrogen generator should go beyond short-term pricing to evaluate its economics, stability and strategic value.
1️⃣ Initial Investment vs. Liquid Nitrogen/Bottled Nitrogen Long Term Cost Comparison
Cost items | Nitrogen Cylinder / Liquid Nitrogen Purchase | Industrial Nitrogen Generator |
Price per unit of gas | ¥4-8/Nm³, fluctuates widely | ¥0.8-2.5/Nm³ (depending on the price of electricity and efficiency of the equipment) |
Cost structure | Includes logistics transportation + deposit + storage | Electricity only + maintenance |
Initial investment | Low (no equipment needed) | Medium (from 80-180,000) |
Annual costs (small and medium production lines) | 15-50 million | 50-15,000 |
Payback: Most mid-sized food manufacturers can recover their PSA equipment investment in 8-18 months.
2️⃣ Reduce product scrap rate and worker training cost
The introduction of nitrogen generator helps to stabilize nitrogen concentration and package residual oxygen control, reduce the following loss potential:
peroxide caused by fried food tastes bad → scrap / return
low concentration of nitrogen caused by the protein, cheese packaging distortion of swelling packages
due to the abnormal residual oxygen repeated stoppages, rework, replacement of packages
Empirical data show that: after the use of industrial nitrogen generator, the average food scrap rate decreased by 20-40%, packaging stability increased by about 30%. Evidence data shows that: after the use of industrial nitrogen generator, the average food scrap rate is reduced by 20-40%, and the stability of packaging is improved by about 30%.
At the same time, the stable operation of the system reduces the problem of frequent retraining due to equipment replacement / cylinder expiration and reduces the rate of operator misuse.
3️⃣ Enhance brand consistency and international export standard responsiveness
Nitrogen concentration consistency is an important indicator of food packaging safety, which is directly related to whether the brand has sustainable supply power and export qualification.
Quality Standards or Export Requirements | Nitrogen / Residual Oxygen Requirements | Industrial Nitrogen Generator Advantages |
HACCP | Fully traceable, residual oxygen control <1% | Equipped with online purity monitoring for stable operation |
ISO22000 | Safe and secure + systematic control | Supports PLC + logging module |
EU/Middle East Export Certification | Specified requirements for food atmosphere gases to be industrial grade | Continuous reporting and validation documentation support available |
As a gas source equipment, industrial nitrogen system can be regarded as one of the control points of HACCP process, which can help to pass the factory audit of customers or overseas factory inspection.
4️⃣ Long-term strategic value: brand reputation and environmental protection goals at the same time
Reduce cylinder transportation → Reduce carbon emission
Avoid leakage risk → Enhance the safety rating of factories
Form self-supply gas source system → Reduce external dependence, stabilize operation capability
Dimensions | Liquid Nitrogen/Bottled Nitrogen | Industrial Nitrogen Generator |
Purchasing Costs | High unit price, transportation and storage costs | High up-front investment, low operating costs |
Gas Quality Consistency | Constrained by logistics and frequency of replacement | Online monitoring, accurate control of residual oxygen |
System Reliability and Safety | Frequent replacement, risk of explosion/pouring of bottles | All-weather operation, automatic alarm and protection |
Ability to Support Brands and Auditors | Untraceable/lack of data | Meet export standards, with compliance record capability |
The system’s life cycle is up to 8-10 years, which can be regarded as a long-term depreciation of assets, and bring stable cash flow return.
With a system life cycle of 8-10 years, it can be considered as a long-term asset depreciation, bringing stable cash flow returns
Recommendation: For food manufacturers with annual nitrogen consumption ≥ 500,000Nm³ or export requirements, the introduction of a PSA nitrogen system is not only a form of cost optimization, but also a core foundation for branding strategy.
Conclusion
Industrial nitrogen generators have proven to be indispensable tools in modern food packaging lines, providing continuous, stable, and clean nitrogen supply that enhances both product quality and operational safety. By minimizing oxidation, inhibiting microbial growth, and replacing explosive or unstable gases in sensitive environments, they help manufacturers meet increasingly strict hygiene, shelf-life, and export standards. Moreover, their integration with real-time monitoring and automation systems contributes to greater energy efficiency and reduced human error, making them a strategic asset for any forward-looking production facility.
As food companies move toward higher levels of standardization and intelligent production, incorporating nitrogen systems should no longer be an afterthought, but a core part of facility upgrades. MINNUO offers high-performance PSA nitrogen generators designed for the food industry, featuring modular installation, 24/7 reliability, and precision control. Whether you’re building a new plant or upgrading an existing line, MINNUO can help you establish a nitrogen solution that enhances product safety, lowers long-term costs, and supports your brand’s sustainability goals.