With the arrival of winter and the sharp drop in temperatures, the stable operation of PSA air separation systems faces a severe challenge. Low-temperature environments not only affect the normal functioning of several devices in the system but may also trigger a series of issues that are rare at normal temperatures, potentially leading to significant economic losses for enterprises. Therefore, we will take you through an in-depth analysis and devise effective winter operation and maintenance strategies to ensure the smooth running of your production.
To ensure the stable operation of PSA air separation systems in winter, key measures include: monitoring the performance of molecular sieves to prevent low temperatures from reducing their adsorption capacity; sealing exhaust outlets and using insulation materials to prevent freezing of drainage valves and pipelines; regularly checking equipment such as air compressors, dryers, air storage tanks, and filters to ensure they function normally in low-temperature environments. These measures effectively reduce operational risks posed by low temperatures and ensure the stability of the system.
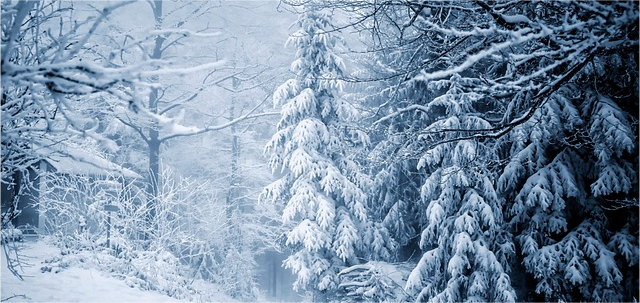
Analysis of Key Components Affected by Low Temperatures
In general, the key components of PSA air separation systems that may be affected in low-temperature environments include the air compressor, dryer, molecular sieve, drain valve, piping system, air storage tank, and filter. Among these, the molecular sieve, drain valve and piping system, air storage tank, and filter of PSA air separation systems may experience the following issues under low-temperature conditions:
Molecular Sieve
Under low-temperature conditions, the adsorption capacity of the molecular sieve significantly decreases. This is because the adsorption process of the molecular sieve relies on intermolecular van der Waals forces, and low temperatures reduce the activity of the molecules, weakening the interaction between the adsorbates and the molecular sieve surface. As a result, the adsorption capacity for target gases is reduced, directly impacting the oxygen or nitrogen production performance of the PSA oxygen or nitrogen generator.
Drain Valve and Piping System
When cold air enters the air compressor and mixes with the high-temperature gas, the water vapor content increases rapidly. When these water vapor-rich gases flow through the drain valve and piping system, the external low-temperature environment causes the water vapor to condense into liquid water or even freeze. This not only obstructs drainage and causes water accumulation in the pipes but also may result in pipe rupture due to the expansion of ice.
Air Storage Tank
In a low-temperature environment, the temperature of the gas in the air storage tank decreases, and the solubility of water vapor also decreases, leading to the precipitation of a large amount of condensate. If the condensate is not drained promptly, it will freeze at low temperatures, affecting the air storage tank’s drainage function. Over time, the accumulation of ice can lead to increased corrosion inside the tank, reducing its service life and even causing safety accidents.
Filters
When the system is shut down, any residual moisture in the filter is highly likely to freeze in low temperatures. The expansion of the ice volume can damage the filter’s core and other components, reducing its filtering precision and making it ineffective at removing impurities from the gas. This can have a severe impact on the normal operation of subsequent equipment, such as causing valve seal failures or instrument malfunctions.
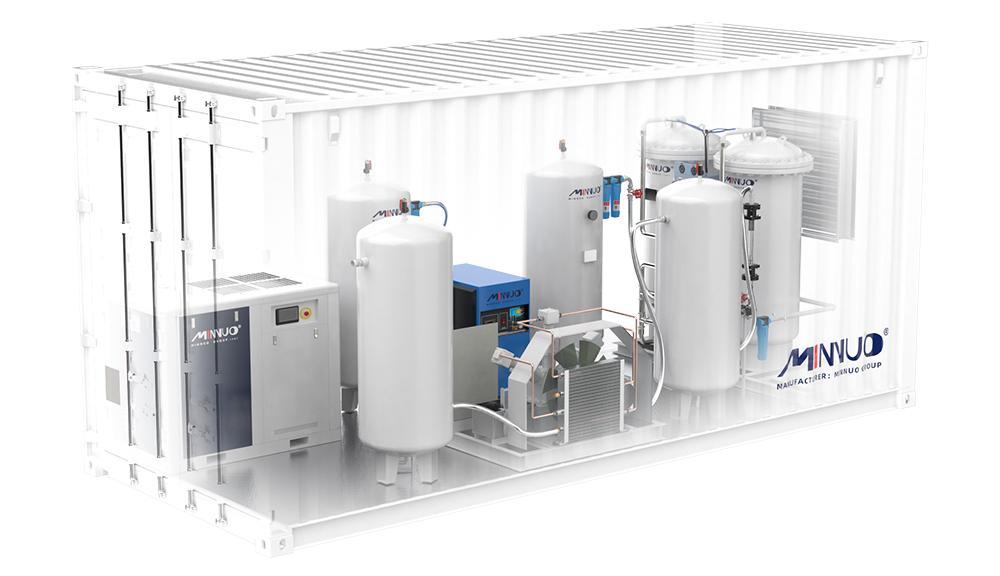
General Measures to Address the Impact of Low Temperatures
Control of Machine Room Temperature
Sealing Ventilation Outlets
During winter, cold outdoor air enters the equipment room through ventilation outlets, causing the room temperature to drop quickly. Closing the ventilation outlets can effectively reduce the heat exchange between indoor and outdoor air, blocking air convection as a path for heat transfer. This helps reduce indoor heat loss, prevents physical damage such as thermal expansion and contraction due to rapid temperature changes, and ensures the normal operation of equipment.
Application of Insulation Materials
Wrapping drainage valves and pipes with suitable insulation materials is an important measure to prevent moisture from freezing. For example, polyurethane foam, with a thermal conductivity as low as 0.02 – 0.025 W/(m·K), can form an efficient thermal insulation layer on the outside of pipes. Rock wool insulation materials combine both thermal insulation and fireproof properties, making them suitable for environments with high fire protection requirements. When wrapping, it is necessary to ensure that the material is completely sealed to prevent cold air from seeping in, reduce the heat transfer between the pipes and the outside, and maintain the moisture inside the pipes to avoid freezing.
Installation of Heating Devices
Installing heating equipment in the equipment room can directly raise and maintain the temperature. Electric heaters and fan heaters warm up quickly and are suitable for raising local temperatures. They should be arranged according to the room’s area and layout. For critical pipelines, installing heating tapes can convert electrical energy into heat energy to directly heat the pipelines. Different power models can be chosen based on pipeline length and environmental temperature needs, ensuring smooth operation of the pipeline system.
Equipment Protective Coatings
Applying protective coatings to the surfaces of metal components such as storage tanks and drain valves can form a protective film on the metal surface in low-temperature, high-humidity environments. This film isolates moisture and oxygen from the air, slowing down the corrosion process. For example, a composite coating system with an epoxy zinc-rich primer base, followed by a polyurethane topcoat, provides strong adhesion and corrosion resistance. When applying this system, the equipment surface should first be sandblasted to remove rust and impurities, and then the coating should be evenly applied to the specified thickness. This helps extend the service life of the equipment and reduces the risk of failures due to corrosion.
Emergency Plan Development
To address extreme low temperatures, companies should develop a comprehensive emergency plan that includes processes for handling equipment failures, starting backup equipment, and personnel division of labor. For instance, the plan should clearly define the time to start backup air compressors in case of failure due to low temperatures, the method for switching equipment, and the troubleshooting and repair processes for the faulty equipment. Additionally, regular drills should be conducted to ensure that operators can quickly and accurately execute emergency procedures when an emergency occurs, thus reducing production losses caused by equipment failures.
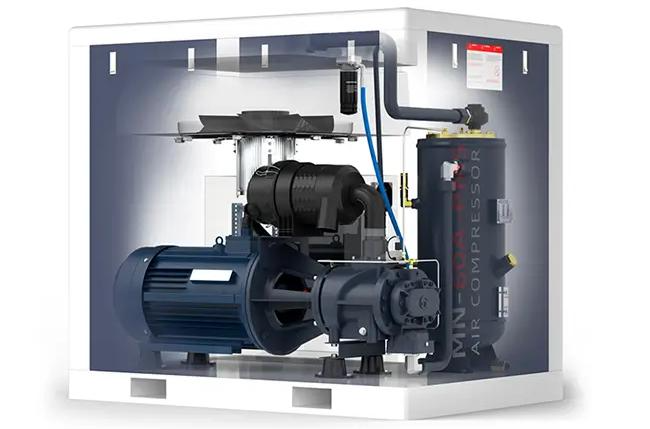
Winter Operation Management and Maintenance of Air Compressors
Impact of Low Temperatures on Air Compressors
Increased Load on Moisture Treatment
When cold air enters the air compressor, water vapor is rapidly generated due to the high internal temperature. This significantly increases the burden on the compressor’s post-treatment system for filtering water vapor. If the moisture is not expelled in time, it can lead to water accumulation in the post-treatment equipment, which affects its performance. For example, in a mechanical manufacturing company, the air compressor’s post-treatment filters frequently clogged due to excessive moisture, with the frequency of replacing filter elements being three times that of normal conditions.
Abnormalities in the Oil Circuit System
For oil-circuit systems that require cooling, although low temperatures help dissipate heat to some extent, for backup or intermittently operating compressors, the low temperature increases the viscosity of the lubricating oil, even causing it to solidify. This can prevent the oil pump from properly supplying lubricating oil during startup, leaving the friction parts of the compressor inadequately lubricated, which accelerates wear and tear.
Winter Measures for Air Compressors
Increase Indoor Temperature
Install air conditioners or industrial heaters in the compressor room to maintain an indoor temperature above 5°C. A stable indoor temperature effectively prevents equipment failures caused by low temperatures, ensuring the normal operation of the air compressor.
Preheat Lubricating Oil
Equip the air compressor with a dedicated lubricating oil heating device to preheat the lubricating oil before startup, allowing it to reach the appropriate viscosity. This ensures that all parts of the air compressor receive proper lubrication during startup, reducing wear and tear.
Compressor Shutdown Management
Cutting off Power and Discharging Debris
When shutting down, first cut off the power supply to the compressor unit and all downstream equipment to ensure the devices are in a safe state. Then, open the drain valves at the bottom of the air storage tank, air dryer, and filter to completely discharge any water and debris inside, preventing moisture from freezing within the equipment.
Releasing Pressure and Cleaning the Equipment
Slowly open the exhaust valves of the compressor unit and downstream equipment to release the internal air pressure to zero. Afterward, use clean compressed air to blow out the internal components of the unit, removing dust and impurities, and wipe the equipment with a clean cloth. Finally, close all the cabinet doors to prevent dust from entering.
Compressor Maintenance
When the compressor needs to be shut down for an extended period, it should be started once a week and run for over 3 hours. During operation, check the equipment parameters to ensure they are within normal ranges, such as oil pressure, oil temperature, and air pressure. After operation, repeat the shutdown management steps to maintain the equipment’s good performance.
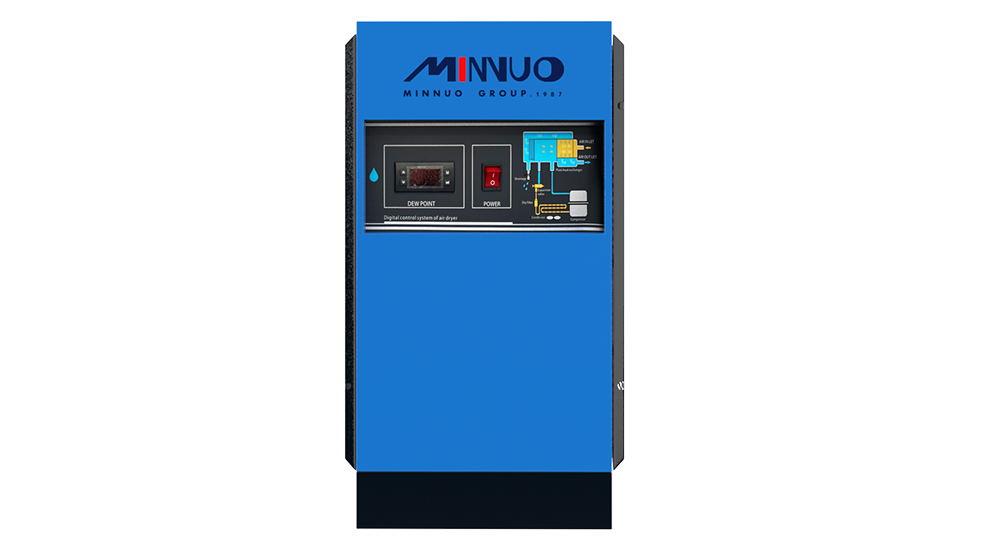
Winter Operation Management and Maintenance of Refrigerated Dryers
Temperature Management
Environmental Temperature Adjustment
Ensure that the environment temperature around the refrigerated dryer is between 5°C and 35°C. This can be achieved by installing temperature control devices around the dryer to monitor the ambient temperature in real time. When the temperature falls below the set value, heating devices such as electric heating plates or warm air blowers should be automatically activated to raise the environment temperature.
Internal Temperature Control of the Equipment
Install temperature sensors on key components inside the refrigerated dryer, such as the evaporator and condenser, to monitor their temperatures in real time. By adjusting the operation parameters of the refrigeration system, ensure that the temperature of these components remains within the normal range, preventing condensation or icing caused by low temperatures.
Cooling Water Management
Supply and Discharge Control
In winter, appropriately reduce the flow of cooling water to prevent excessive cooling that may lead to the freezing of the condenser. At the same time, ensure smooth discharge of cooling water to prevent water accumulation. Flow control valves and drainage valves can be installed on the cooling water pipelines and adjusted according to actual conditions.
Heating and Anti-Freeze Measures
Install electric heaters in the cooling water system to automatically activate the heater when the water temperature approaches the freezing point, keeping the water temperature above 5°C. Additionally, antifreeze can be added to the cooling water to raise its freezing point and prevent freezing.
Maintenance and Upkeep
Regular Cleaning and Inspection
Clean the condenser and evaporator once a week to remove dust and dirt from the surface, ensuring optimal heat exchange performance. Perform a comprehensive inspection of the air dryer’s internal structure every month, including pipeline connections, valve seals, etc., to promptly detect and address any potential issues.
Compressor Maintenance
Regularly check the quality and level of the compressor’s lubricating oil. If the oil appears degraded or the level is too low, replace or replenish it in a timely manner. Also, check the tension of the compressor’s belts, the motor’s insulation performance, etc., to ensure the compressor operates smoothly.
Load Control
Real-time Load Monitoring
Install compressed air flow sensors and humidity sensors to monitor the air dryer’s intake flow rate and moisture content in real time. Through the control system, automatically adjust the operating parameters of the air dryer based on actual load conditions to ensure it is in optimal working condition.
Optimized Operating Mode
Adjust the operation time and load distribution of the air dryer based on the company’s production patterns. During low-load periods, appropriately reduce the cooling capacity of the air dryer to save energy while maintaining effective drying.
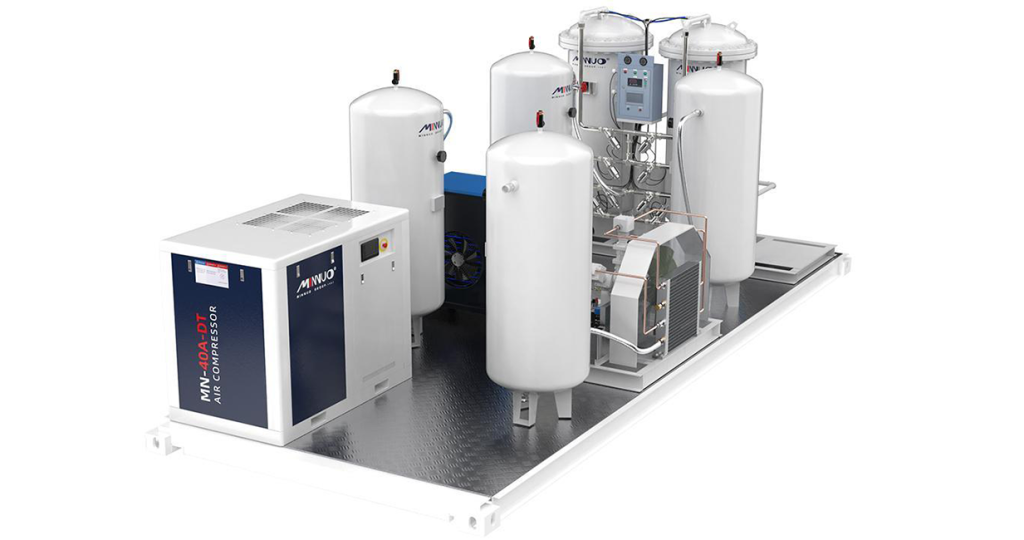
Conclusion
It is very important to protect PSA air separation systems from cold in winter to ensure the normal operation of the equipment. This not only helps to improve production efficiency but also effectively extends the equipment’s service life. Therefore, companies and relevant operators should pay close attention to winterization measures of PSA air separation systems and take effective steps to ensure the equipment runs safely and stably.
MINNUO not only has over 30 years of experience in gas equipment manufacturing, but also has assembled a professional engineering team, always ready to provide service and assistance. We welcome you to consult with us!