The natural conditions of high-altitude regions, such as low oxygen levels, low atmospheric pressure, and extreme climates, pose severe challenges to oxygen supply for medical, industrial, and residential needs. Ordinary oxygen equipment often struggles with low efficiency and frequent malfunctions, making it difficult to ensure stable oxygen supply during critical times. This article analyzes the specific requirements of oxygen generation in high-altitude environments and illustrates how advanced technologies in the oxygen generator for high altitude regions enable high-performance systems to tackle complex conditions efficiently and reliably.
In high-altitude areas, ordinary oxygen generators struggle to function reliably due to low atmospheric pressure, reduced oxygen content, and extreme temperature variations. Issues like low compression efficiency and unstable oxygen concentration are common. The oxygen generator for high altitude regions should employ advanced compressors, utilize nano-coated molecular sieve technology, and include intelligent pressure compensation, pre-heating, and multi-stage filtration systems to withstand low oxygen, low temperatures, and harsh environments. Through customized design and remote monitoring technology, MINNUO provides efficient, stable, and low-maintenance oxygen solutions, making it an ideal supplier for high-altitude equipment.
Differences in Oxygen Content at Various Altitudes and Their Effects
Oxygen Content at Different Altitudes
The primary problem faced at high altitudes is the reduction in oxygen concentration. As altitude increases, atmospheric pressure gradually decreases, leading to a significant reduction in the partial pressure of oxygen:
Altitude | Oxygen Partial Pressure (in Air) | Change in Oxygen Content (Compared to Sea Level) |
---|---|---|
0 m (Sea Level) | 101 kPa | 21% (Standard) |
2000 m | 80 kPa | Approx. 16.4% (20% reduction) |
4000 m | 60 kPa | Approx. 12.6% (40% reduction) |
5000 m | 50 kPa | Approx. 10.5% (50% reduction) |
Specific impact of high altitude hypoxia on oxygen production equipment
- Reduce oxygen extraction efficiency:The oxygen content in the air at high altitudes is low, and the oxygen production equipment needs to process more air to obtain the same concentration of oxygen, which directly increases the workload of the equipment.
- Equipment negative pressure problem:Ordinary oxygen production equipment is not designed with low pressure environment in mind. Insufficient air pressure will lead to a decrease in the air compression efficiency of the equipment, thereby reducing the oxygen production capacity.
- Unstable oxygen concentration:Under the dual influence of air pressure fluctuations and thin air, ordinary equipment cannot guarantee the stability of oxygen output concentration and flow rate.
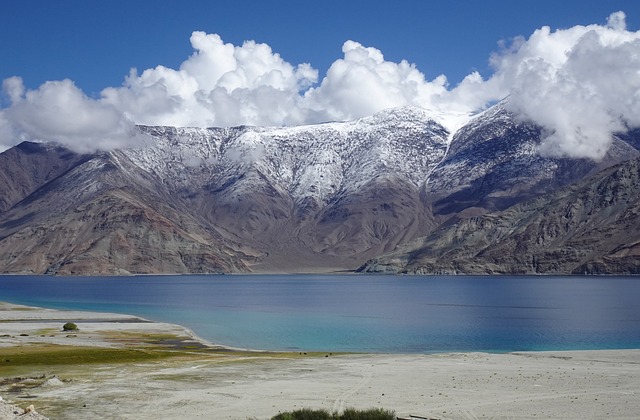
Strict requirements of high-altitude environment on oxygen production equipment
High-altitude areas not only face low-oxygen environments, but also other harsh conditions, which put forward many special requirements for oxygen production equipment:
Extreme temperature difference and low temperature problems
- Large temperature difference between day and night: The temperature difference between day and night in high-altitude areas may be as high as 30℃ or more. Drastic temperature changes may cause condensation inside the equipment and aging of components.
- Low temperature challenge: Winter temperatures can be as low as -30℃ or even lower, which may cause freezing of lubricating oil, icing of pipelines and damage to components.
Wind and sand and impurity problems
- Poor air quality: Wind and sand are frequent in high-altitude areas, and the air contains a large amount of particulate matter. These impurities will clog the filter element of the equipment and affect long-term operation.
High humidity environment problem
- Condensation water impact: Low temperature and high humidity environment easily form condensation water, which may cause internal corrosion of the equipment or short circuit of electrical components.
Stability and reliability requirements
- Continuous operation capability: Medical institutions and industrial production require equipment to operate 24 hours a day, which requires oxygen production equipment to have extremely high stability.
- Low maintenance requirements: Transportation and logistics in high-altitude areas are inconvenient, and equipment must reduce maintenance frequency as much as possible.
Technical solutions for high-altitude needs
For the extreme environment in high-altitude areas, our oxygen generator for high altitude regions adopts a number of advanced technologies, from core components to intelligent control systems, which have been deeply optimized to ensure that the equipment can still operate efficiently and stably under complex working conditions such as low oxygen, low pressure, and low temperature. The following is a detailed description of our technical solutions:
Core technology: high-performance compression system
The core components of our oxygen generator for high altitude regions use Atlas high-performance compressors, whose design and manufacturing strictly follow international standards, such as ISO 8573-1:2010 air purity grade standards. Specific advantages include:
- High-efficiency air compression capacity: In an extremely low pressure environment at an altitude of 5,000 meters, it can still provide a compression capacity of up to 0.7MPa, ensuring sufficient air intake to support efficient oxygen extraction.
- Low energy consumption technology: Through the built-in variable frequency regulation system (in compliance with the IEC 61800-9 energy efficiency standard), the compressor automatically adjusts the power output according to the real-time load, saving about 30% energy compared to traditional fixed-speed compressors.
- High durability design: The compressor components are made of special alloy materials, which are resistant to high temperatures and corrosion, and can operate for a long time at ambient temperatures of -40℃ to 50℃.
Molecular sieve adsorption technology upgrade
Our equipment uses the internationally leading nano-coated molecular sieve adsorption technology, and its performance and life far exceed traditional molecular sieves. This technology has achieved the following technical indicators:
- Adsorption efficiency increased by 25%: Even in an environment where the oxygen content in the air is less than 15%, the oxygen extraction efficiency can still be maintained at more than 85%.
- Long-life design: The service life of the molecular sieve exceeds 10 years, which is more than 50% higher than the industry standard, reducing the frequency of replacement and reducing user costs.
- High-purity oxygen output: The oxygen concentration is stable at 93%±3%, which fully complies with international medical-grade oxygen standards (such as ISO 7396-1:2016 and EN ISO 80601-2-12).
- The coating technology of the molecular sieve also significantly enhances the moisture resistance, and can maintain long-term adsorption efficiency in high humidity environments, avoiding the failure of traditional molecular sieves due to moisture absorption.
Intelligent pressure compensation system
In order to cope with the problem of low air pressure and large pressure fluctuations in high altitude areas, we have developed an intelligent pressure compensation system (IPC, Intelligent Pressure Compensation), which automatically optimizes the equipment operating parameters by real-time monitoring of ambient air pressure and oxygen output status:
- Real-time adjustment: The IPC system has a built-in high-precision pressure sensor (accuracy ±0.01MPa), which can respond to air pressure changes in milliseconds and dynamically adjust the compressor output power and adsorption time.
- High-efficiency adaptability: The system can always maintain the stability of oxygen flow and concentration at altitudes above 5,000 meters, with a fluctuation range of no more than ±2%.
- Standard compliance: The IPC system design meets the IEC 60601-1-11 medical environment suitability requirements and can be used in harsh medical environments.
Multi-stage air filtration and purification system
The air in high-altitude areas has high particulate matter and humidity. Our equipment is equipped with an industry-leading four-stage air filtration and purification system:
- Coarse filter: Filters particles ≥5 microns to ensure initial purification.
- High-efficiency air filter (HEPA grade): Removes ≥99.97% of particulate matter (in accordance with EN 1822 standards), including fine PM2.5 particles.
- Dehumidification module: A dual dehumidification system combining condensation technology and adsorption technology is used to reduce air humidity to ≤10%, effectively protecting the molecular sieve from moisture.
- Activated carbon adsorption module: Removes odors and harmful gases in the air to ensure that the oxygen is pure and free of impurities.
This system effectively extends the operating life of the equipment while reducing maintenance requirements.
Low temperature environment adaptation: intelligent preheating system
In order to cope with the extremely cold climate in high altitude areas, we have integrated an intelligent preheating system into the equipment, and its design complies with the requirements of EU standard EN 60079-7 (increased safety equipment):
- Fast preheating: In an environment of -40℃, the equipment can complete the preheating of key components within 10 minutes, including the compressor, molecular sieve cabin and pipeline, to ensure the normal startup of the system.
- Uniform heating technology: Nano-scale PTC ceramic heating plate is used to uniformly heat the core components to avoid damage caused by local temperature differences.
- Dynamic temperature control: The intelligent control system monitors the ambient temperature in real time and automatically adjusts the heating power as needed, which not only ensures the startup efficiency but also avoids energy waste.
Intelligent control and remote monitoring system
The control system of our equipment is based on Industrial Internet of Things (IIoT) technology, with a built-in intelligent monitoring module, providing the following functions:
- Real-time data monitoring: Key operating data such as temperature, pressure, and oxygen concentration are collected through multi-channel sensors, and the system is refreshed once every second.
- Fault prediction and alarm: The system has built-in AI algorithm, which can predict possible faults in advance and issue alarms through the analysis of historical operation data to avoid equipment downtime.
- Remote management: Users can remotely monitor the operation status of the equipment and adjust the operation parameters through mobile phones or computers; the technical team can also remotely diagnose and respond quickly.
- The control system complies with the IEC 62443 industrial network security standard to ensure safe and reliable data transmission.
Energy efficiency optimization and environmental protection design
In high-altitude areas, energy consumption is a major cost of equipment operation. Our oxygen production equipment is designed with full consideration of energy efficiency optimization:
- Frequency conversion control technology: By dynamically adjusting the operating frequency of the compressor, the output power is output according to actual needs, reducing unnecessary energy consumption, and the energy efficiency ratio (COP) reaches the international leading level.
- Modular design: The core components adopt a modular layout, which is convenient for users to expand the equipment capacity according to needs and avoid resource waste.
- Use of environmentally friendly materials: The equipment shell and internal components are made of recyclable environmentally friendly materials, and at the same time, they have passed RoHS and REACH certification to reduce the impact on the environment.
Standards and certification guarantees
Our oxygen generators not only have leading advantages in technology, but also have passed a number of international authoritative certifications to ensure product quality and performance:
- ISO 13485: Medical device quality management system certification to ensure the safety and reliability of the equipment in medical scenarios.
- CE certification (medical device category): complies with the relevant requirements of the EU Medical Device Directive (MDR) and is applicable to the global market.
- UL certification: The electrical part of the equipment has passed the US UL certification to ensure the electrical safety of the equipment in high humidity, high pressure and low temperature environments.
Through the above technical solutions, the oxygen generator for high altitude regions not only performs well in challenging environments but also gains wide recognition for its high efficiency, low maintenance, and long lifespan. Choosing our products means choosing a reliable, advanced, and long-lasting solution for high-altitude oxygen generation.
Case sharing: Customized solutions for high-altitude hospitals in Tibet
Background
In March last year, we received a customer from a Tibetan tertiary hospital located at an altitude of 4,500 meters. The hospital needs to provide a stable oxygen supply for ICU, operating room and hyperbaric oxygen chamber. Due to the inconvenient local transportation, the stability and low maintenance requirements of the equipment are very high.
MINNUO solution
Equipment configuration
Two Atlas high-performance compressor-driven oxygen generators are provided, with an oxygen production capacity of up to 50Nm3 per hour, equipped with:
- Intelligent preheating system to ensure normal startup in winter;
- Multi-stage air filtration module to effectively deal with plateau wind and sand problems;
- Intelligent pressure compensation system to adapt to 4500 meters of air pressure conditions.
Additional design
- Backup power supply module: Provide stable power supply when the local power grid fluctuates frequently.
- Remote monitoring system: The equipment operation data is uploaded in real time, and the technical team can monitor remotely and provide timely support.
Results
- Operation efficiency increased by 30%: Meet the hospital’s all-weather high-intensity oxygen demand.
- Maintenance cycle extended by 50%: From the original monthly maintenance, it was extended to once a quarter, significantly reducing operating costs.
- Improved user satisfaction: The hospital highly praised the stability and intelligent control functions of the equipment and purchased the same model of equipment at the beginning of this year.
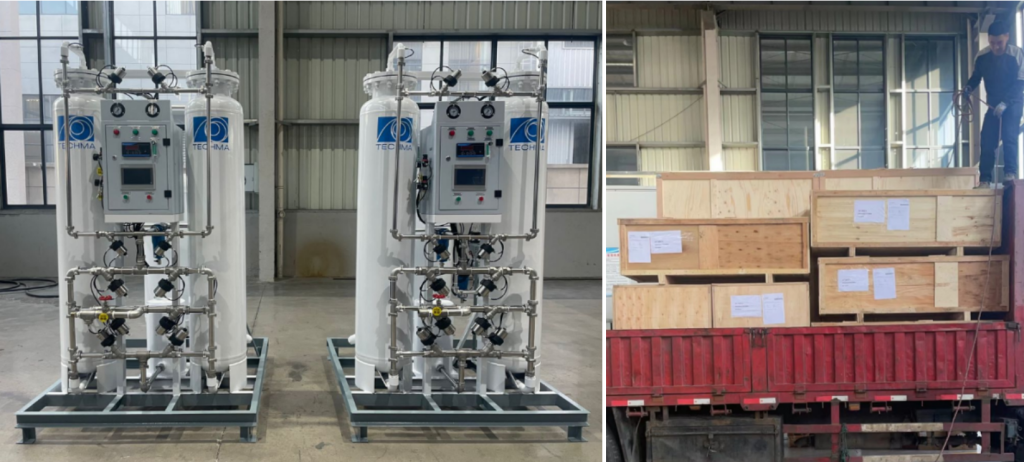
Reasons to choose MINNUO
Technological leadership
We use a number of core technologies such as Atlas compressors, high-efficiency molecular sieves, and intelligent pressure compensation to ensure that the equipment always maintains high-performance operation in high-altitude environments.
Professional design
The equipment structure is optimized for extreme working conditions at high altitudes, including preheating systems, antifreeze lubricants, and multi-stage filtration designs.
Customized services
Provide tailored air solutions based on customer needs, covering medical, industrial, and household fields.
All-round support
From equipment selection, solution design to installation and commissioning and after-sales service, we provide customers with full-process support to ensure long-term and stable operation of the equipment.
Conclusion
High-altitude environments demand robust the oxygen generator for high altitude regions. With advanced technology and professional design, we provide efficient, stable solutions. For high-altitude oxygen production or air solutions, choose MINNUO. We are committed to adding power to your career and life with excellent products and services. For more information, please feel free to contact our professional team.