Introduction
The fully automatic compact liquid nitrogen preparation system uses a variable pressure adsorption nitrogen generator (PSA nitrogen generator) to produce nitrogen from the air, which is liquefied into liquid nitrogen by a mixed working medium throttle chiller and stored in a liquid nitrogen Duva. The compact system allows for a continuous and convenient liquid nitrogen supply. This article will focus on the maintenance of the liquid nitrogen machine.
Maintenance instructions for the electronic control system
The goal of this section is to ensure the normal work of the control box. Regular maintenance is divided into general inspection and overhaul inspection.
General inspection (once every half a month)
- Before the maintenance inspection, the control box must be cut off first, and live maintenance is strictly prohibited.
- Remove all dust and dirt inside and outside the box.
- Check whether the fasteners of each electrical element are loose, whether the activation mechanism is flexible, and whether there is arc discharge, flash flipping, and crawling traces between the live parts and the shell. If found, they should be repaired.
- Check whether the metal plating part has a rust phenomenon; if found, it should be replaced.
- When checking the contact of the electrical element, if a delicate melt is found on the contact surface, it should be removed with an oil file, and the contact surface should be made to maintain its original shape and polished with polishing sand to ensure reliable contact with the contact. If the contact oxidation blackening phenomenon can not use for oil file clearance, and the application of gasoline dipped in the gasoline cloth, carefully wipe, and wipe the gasoline at the same time clean.
- Check the contact pressure of the contactor and the relay contact and the excess travel and disconnection distance. Do not meet the requirements and should be repaired and adjusted.
- Check whether the contact spring and non-magnetic gasket of the contactor and relay are intact. If they are damaged or fall off, they should be replaced and repaired. Yet, after the replacement and repair, the element must be adjusted again.
- Check whether the insulation resistance of the control box’s electrical components and the grounding room’s insulation resistance meets the data specified in the technical conditions. If not, it should be repaired.
- Check whether the grounding device is in good condition, the grounding resistance should not be more excellent than 0.1 euros, and whether the grounding screw is loose and corroded; if found, it should be repaired immediately.
Overhaul inspection(at least once every three months)
- After cutting off the input power of the control box before the overhaul inspection, the external wire connected with the outer box should be removed.
- All items required for general inspection
- Thoroughly remove the internal and external dust and dirt of electrical components, check whether there is a local overheating phenomenon if there is found to measure the coil DC resistance, check whether there is an inter-turn short circuit phenomenon if there is a short circuit, should be replaced.
- Check whether the magnetic short-circuit ring of the contactor and the relay electromagnet core has open welding or fracture phenomenon. If found, it should be repaired or replaced. At the same time, remove the oil on the suction surface of the iron core, to prevent hot adhesion so and can not be disconnected.
- Check and adjust the operating current of the thermal relay.
Liquid nitrogen machine maintenance instructions
This part includes several replacements and maintenance tables.
Air compressor filter element replacement
(This operation shall close the air compressor and confirm that the air pressure of the air compressor pipeline is unloaded)
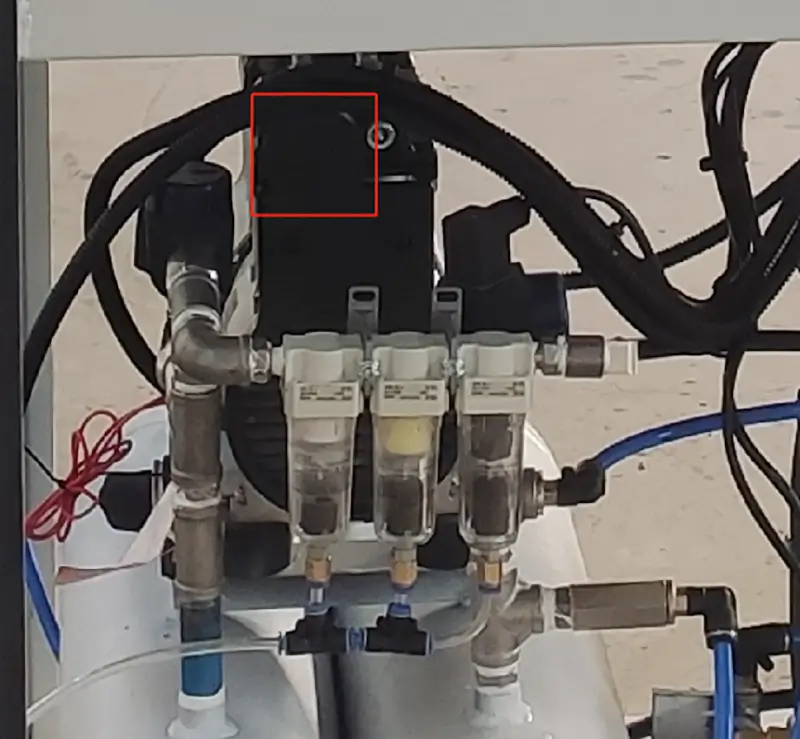
Note: Replace the air compressor and the air filter element
- Close the air compressor and liquid nitrogen machine and confirm that the system pressure has been released
- Open the left cover of the liquefier
- Remove the filter housing
- Rotate and remove the used filter element and tighten the new filter element
- Install the filter housing completely
- Replace the other filter elements in turn
- Reset the upper cover and tighten the bolts
Filter element replacement
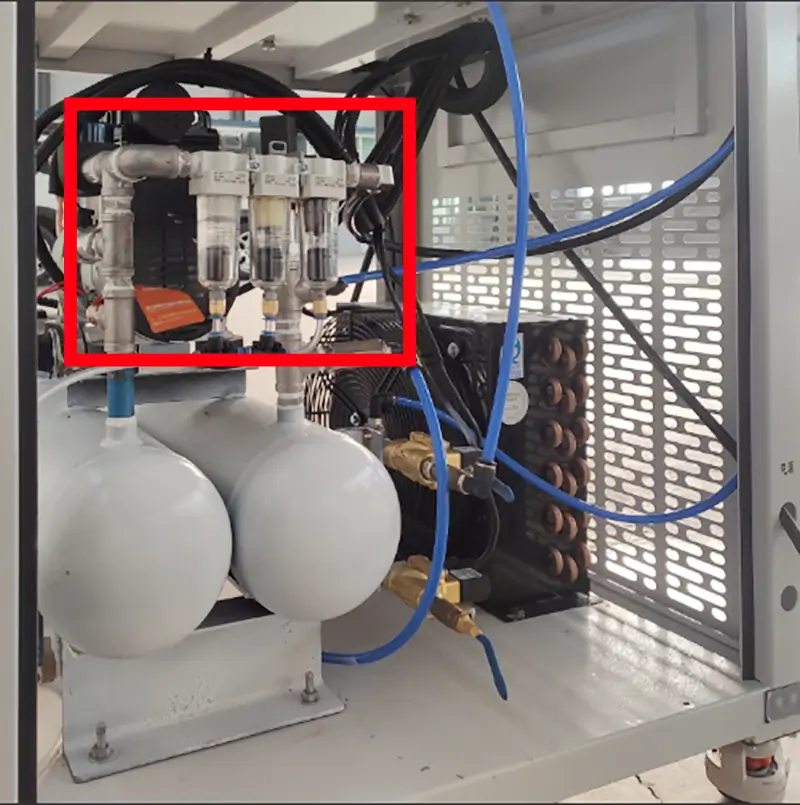
- Turn off the nitrogen generator and see clause 3 to confirm that the system pressure has been released
- See the side cover plate
- Replace the filter element between the middle partition plate of the nitrogen generator in turn.
Safety valve replacement
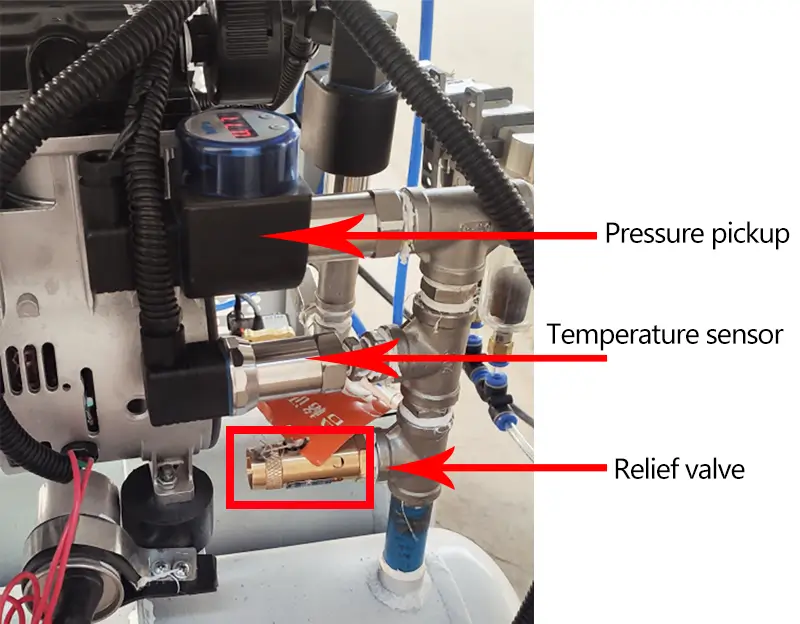
The safety valve needs to be checked regularly and replaced once a year.
Automatic drain device replacement
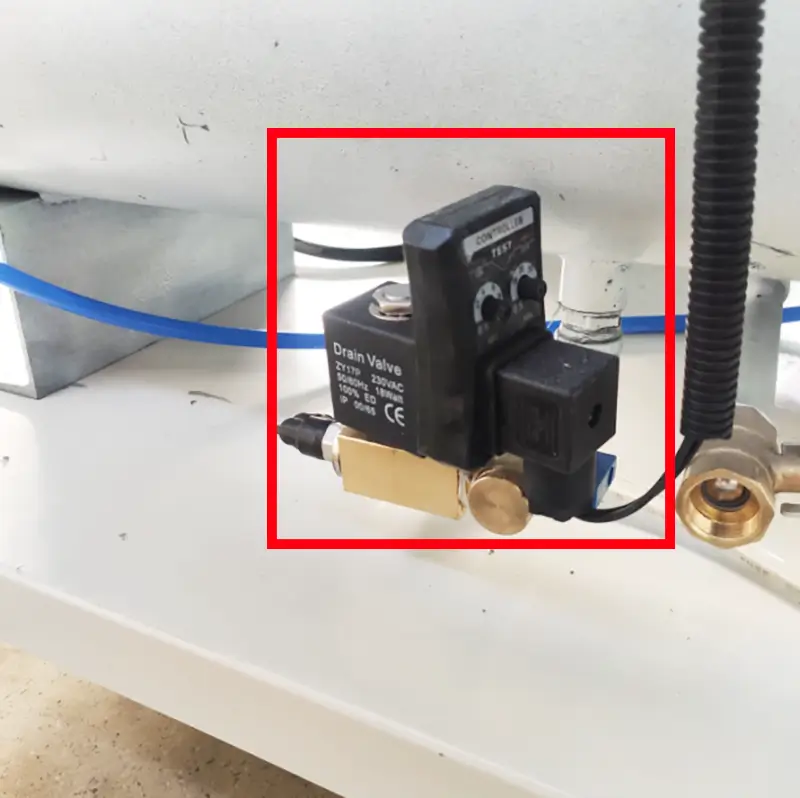
The automatic drain device needs to be checked regularly and replaced every 2-3 years.
Maintenance
Equipment maintenance is on every 3000 hours to prompt the equipment maintenance. According to the different environmental cleanliness and load degrees of temperature and humidity meter, it is recommended to replace the air compressor intake filter element and air filter element according to Table.
Maintenance instructions for the liquid nitrogen machine
Air-cooled condenser debris cleaning: we need to ensure that the environment is clean, if the environment is harsh, it is necessary to clean the debris in the fin tube of the air-cooled condenser regularly.
Conclusion
Liquid nitrogen generators are essential in producing high-purity nitrogen in many industries. Liquid nitrogen generators are widely used in medical research, food processing, and manufacturing.
Regular maintenance of liquid nitrogen generators is essential to ensure the safe and efficient operation of the equipment. Failure to properly maintain a liquid nitrogen generator can lead to equipment failure. This results in costly downtime, reduced productivity, and potential hazards to workers. So, following the manufacturer’s maintenance guidelines and scheduling regular inspections and repairs with a qualified technician is critical.