In modern industrial systems, industrial gases such as nitrogen (N₂) and oxygen (O₂) play an irreplaceable role in fields such as industrial manufacturing, food processing, and electronics production. However, in practice, many enterprises often fall into the misconception that “the higher the gas purity, the better” and “purity equals quality.” This article will deeply analyze the differences between industrial gas purity and quality, their application logic, and explore how on-site gas generation technology can achieve efficient and economical industrial gas management.
Industrial gas purity refers to the proportion of the target gas in a mixed gas. High purity is suitable for applications like metal processing and electronics manufacturing, while low purity is more cost-effective for scenarios such as food packaging and chemical tank inerting. On-site gas generation allows for purity adjustments to reduce costs. Quality is critical in controlling contaminants such as dust, water, and oil. Industries like pharmaceuticals and food & beverages have strict requirements, as failing to meet quality standards can lead to equipment damage and food safety risks. On-site gas generation ensures quality through multi-stage filtration. The purity and quality of industrial gases should be based on “suitability,” taking into account process requirements and cost-effective configurations to avoid waste caused by blindly pursuing high standards.
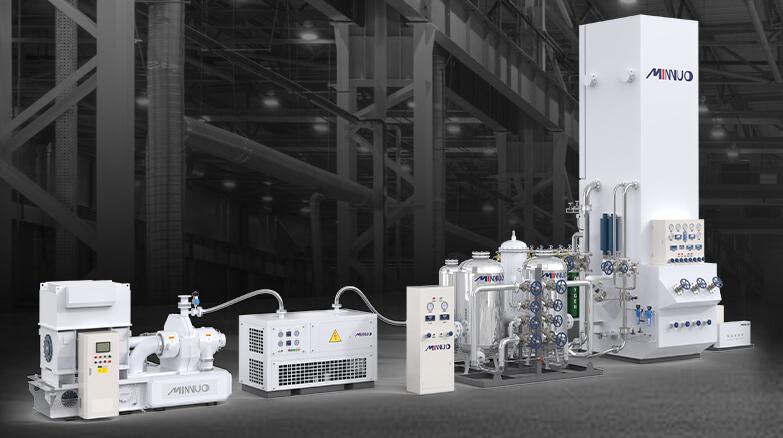
I. Industrial Gas Purity
In the industrial gas field, purity and quality are two distinct concepts. Purity only represents the percentage of the target gas in a mixed gas. For example, nitrogen with 99.9% purity means that 99.9% of the volume or mass of the gas sample is nitrogen molecules, and the remaining 0.1% is other gas impurities. However, “high purity” does not naturally mean “better,” as the key is whether the gas purity matches the specific process requirements.
High Purity Demand Scenarios
In the metal processing field, processes such as laser cutting or annealing have extremely high nitrogen purity requirements. For example, in laser cutting, high temperatures cause rapid oxidation of the metal. Without high-purity nitrogen to isolate oxygen, an oxide layer forms on the metal surface, affecting cutting accuracy and reducing cutting speed and equipment lifespan. Therefore, such processes typically require 99.999% pure nitrogen to ensure that the metal remains in an oxygen-free environment throughout the process, achieving high-quality cutting results.
The electronics manufacturing industry has even stricter gas purity requirements. In semiconductor production, every step of chip manufacturing is extremely precise, and even tiny impurities or gas contaminants can cause the chip’s performance to degrade or fail. Ultra-pure nitrogen (above 99.9995%) is widely used in semiconductor production processes for cleaning, purging, and protection, to prevent contamination of components and ensure the chip’s performance and yield.
Low Purity Applicable Scenarios
In the food packaging industry, nitrogen purity requirements are relatively low. Usually, nitrogen with a purity of 95%-98% is sufficient to block oxygen, inhibit microbial growth, and extend the shelf life of food. Excessively high purity does not add value and only increases production costs. For example, packaging of puffed foods like potato chips and biscuits only requires low-purity nitrogen to meet preservation needs.
In the chemical industry, low-purity nitrogen is commonly used for inerting storage tanks, reducing the concentration of flammable gases inside the tank to prevent explosions. Compared to high-purity nitrogen, low-purity nitrogen has significant cost advantages, allowing for better cost-efficiency while ensuring safety.
On-site Gas Generation Purity Advantage
Traditional purchased bottled gases often use uniform high-purity standards. This “one-size-fits-all” supply method forces enterprises to pay extra for unnecessary high purity in scenarios where gas purity requirements are not high, leading to energy and financial waste. MINNUO’s nitrogen/oxygen generators offer precise control over gas purity, with a wide range of adjustment from 70%-99.9995%. Enterprises can accurately control gas purity according to actual production needs, meeting process requirements while avoiding unnecessary costs and effectively reducing energy consumption and production costs.
II. Industrial Gas Quality
The key to industrial gas quality lies in controlling the content of contaminants such as dust, water, and oil. The international standard ISO 8573-1 provides detailed classifications for compressed air quality, categorizing it according to solid particles, water, and oil content, offering authoritative guidance for enterprises in selecting the appropriate quality of industrial gases.
Stringent Industry Requirements
In the pharmaceutical and biotechnology industries, the quality of gas must meet nearly stringent standards. The drug production process must strictly follow sterile, impurity-free standards, as any small contamination can affect the safety and effectiveness of the drugs. Therefore, the pharmaceutical industry typically requires Class 0 oil-free air to ensure a clean production environment and prevent contamination of the drugs.
The food and beverage industry also has strict requirements for gas quality. To prevent microbial growth and ensure food safety and quality, dry gases of Class 2 or higher are necessary. If the gas contains excessive moisture, it can cause food spoilage; if it contains oil, it can affect the taste and quality of the food.
Risks of Insufficient Quality
Using industrial gases that do not meet quality standards can bring numerous risks to enterprises. Oil-laden gases entering equipment may cause oil to accumulate inside, leading to equipment corrosion and reduced lifespan. Water in the gas can condense into ice in low-temperature environments, causing pipe blockages, affecting gas delivery, and even damaging equipment. In the food processing industry, poor-quality gas may lead to food spoilage and food safety issues, resulting in significant economic losses and reputational damage.
MINNUO On-site Gas Quality Assurance
MINNUO’s on-site gas generation equipment comes with a built-in multi-stage filtration system to ensure gas quality at the source. Its default configuration meets the ISO 8573-1 Class [1:2:1] standard, controlling dust particles to ≤0.1μm and lowering the pressure dew point to ≤-40℃, ensuring oil-free gas. For industries such as semiconductors and laboratories with high gas quality requirements, MINNUO also offers optional high-efficiency filters that can upgrade gas quality to Class [1:1:0] to meet the most stringent usage demands.
III. Balancing Purity and Quality
System Matching Principle
The effectiveness of industrial gas use not only depends on the gas’s purity and quality but also on the delivery, storage, and usage stages. Even if an enterprise purchases high-purity, high-quality gases, if the delivery pipeline is rusted, seals are not tight, or packaging materials are highly permeable, the gas may be contaminated during transportation, affecting its end-use performance. Therefore, enterprises need to establish a comprehensive quality management system to ensure that every link—from production and storage to transportation—meets relevant standards, ensuring stable gas quality.
Maximizing Cost Efficiency
While purchased bottled gases offer flexible supply, they have notable drawbacks. The purity and quality of bottled gases are typically fixed, and enterprises often have to buy expensive high-purity, high-quality gases to meet the needs of a few high-demand processes. However, in other processes where gas requirements are low, the performance of these high-cost gases cannot be fully utilized, leading to significant cost wastage.
MINNUO’s on-site gas generation system offers a better solution. The system supports differentiated gas supply according to the needs of different production processes. For example, in an electronics factory, nitrogen purity requirements for the welding process are relatively low, while for chip packaging, high-purity nitrogen is required. MINNUO’s on-site gas system can meet both of these demands. Additionally, the system can dynamically adjust filtration levels according to actual production conditions, reducing filtration costs in low-demand scenarios, achieving maximum cost efficiency.
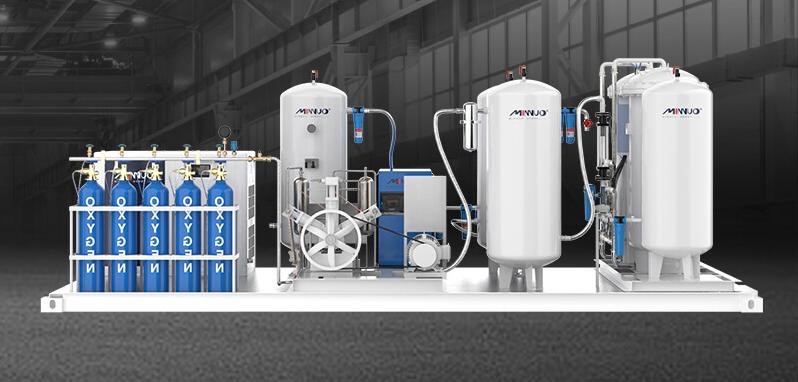
IV. Why Choose MINNUO On-site Gas Generation System?
Customized on Demand
MINNUO’s on-site gas generation system is highly flexible and can adjust gas purity and quality according to diverse production needs. Whether for the highly demanding electronics manufacturing industry or the cost-sensitive food processing industry, MINNUO can provide personalized solutions to meet the special needs of different enterprises and production processes.
Direct Cost Reduction
Compared to traditional purchased gases, MINNUO’s on-site gas generation system offers significant cost advantages. Enterprises no longer need to pay extra for unnecessary high-purity gases and avoid the costs of transporting and storing bottled gases. Statistics show that using MINNUO’s on-site gas generation system can reduce overall costs by 30%-50%, with a return on investment as short as 6-12 months, providing tangible economic benefits to enterprises.
Stable Supply
For continuous production enterprises, a stable gas supply is crucial. Purchased bottled gases may be affected by transportation and inventory issues, posing a risk of gas shortages. Once the gas supply is interrupted, production will halt, leading to significant losses for enterprises. MINNUO’s on-site gas generation system ensures 24-hour uninterrupted gas supply, ensuring continuous production and effectively preventing production losses due to gas interruptions.
Green and Low Carbon
With increasing environmental awareness, sustainable development has become an important goal for enterprises. MINNUO’s on-site gas generation system helps enterprises achieve green production by reducing carbon emissions in the gas transportation process. Compared to traditional bottled gas transportation, on-site gas generation significantly reduces energy consumption and environmental pollution, aligning with national energy-saving and emission-reduction policies, and enhancing the enterprise’s social image.
V. Conclusion
The purity and quality of industrial gases are not necessarily better when higher but should focus on “applicability,” scientifically configuring gas purity and quality based on process requirements and cost structure. Blindly pursuing high purity and high quality not only increases enterprise costs but also leads to resource wastage.
If you are struggling with industrial gas supply and management issues, consult MINNUO experts now to obtain a customized gas supply solution and start a new journey of efficient, economical, and green industrial gas management!