In today’s industrial applications, PSA technology is widely used for its efficiency and reliability in separating nitrogen and oxygen Variable Pressure Adsorption (PSA) Cycle Times and Their Effect on Nitrogen and Oxygen Generator, especially in gas production and purification processes.PSA technology controls the adsorption and desorption processes to enable the efficient separation of nitrogen and oxygen to meet the purity and flow requirements of industrial production. With the change of industrial demand, the application of PSA technology is also expanding and deepening, thus promoting the progress and innovation of gas separation technology.
In the process of nitrogen and oxygen separation, the adjustment of PSA cycle time is crucial. The length of the cycle time directly affects the purity and yield of nitrogen and the energy efficiency of the equipment. In this paper, we will deeply analyze how the PSA cycle time affects the separation of nitrogen and oxygen, and discuss how to improve the stability and efficiency of gas production by optimizing the cycle time. We will also focus on how to adjust the PSA system settings according to different industrial needs to ensure long-term stable operation and efficient gas supply.
The aim of this paper is to answer the question of how to maximize the effect of nitrogen and oxygen separation through reasonable PSA cycle time control to further improve production efficiency. Through an in-depth analysis of the technical details of PSA, you will learn how to optimize the system settings to cope with different gas demands, while improving the economy and energy efficiency of the equipment. In this article you will receive expert guidance on PSA technology optimization and equipment selection to help you increase productivity and reduce operating costs.
Ⅰ.PSA Technology Basic Principle and Cycle Time Concept
1. Introduction to PSA Technology
Definition: PSA (Pressure Swing Adsorption) technology is a kind of technology that utilizes the adsorption and desorption process of adsorbent material (e.g., molecular sieve) on gases at different pressures to realize the separation of nitrogen and oxygen through the change of pressures. PSA technology is widely used in industrial gas separation, especially in the production of nitrogen and oxygen. PSA technology is widely used in industrial gas separation, especially in the production of nitrogen and oxygen. The basic principle is to separate oxygen and nitrogen in the air by adsorption material, remove oxygen from the air, so as to get high purity nitrogen.
PSA Technology Flow:
PSA systems typically consist of two main steps: adsorption and desorption. In the adsorption stage, air passes through the adsorption tower under high pressure, the molecular sieve adsorbs the oxygen and moisture, and the remaining nitrogen is separated and exported. In the desorption stage, the adsorbed oxygen and moisture are released by lowering the pressure and recycled again, thus maintaining the long-term adsorption capacity of the molecular sieve.PSA systems typically consist of two adsorption towers working in alternation, with each tower alternating between adsorption and desorption operations, to ensure continuous and stable nitrogen production.
Advantages:
High efficiency nitrogen separation: PSA systems are capable of delivering high purity nitrogen, typically in the range of 95% to 99.9%, depending on the actual demand.
Continuous operation: PSA technology is capable of 24/7 continuous operation, making it suitable for industrial environments that require a constant supply of nitrogen.
Energy-efficient and cost-effective: PSA systems greatly reduce transportation and storage costs by producing nitrogen on-site compared to traditional liquid nitrogen transportation methods.
2. Definition and Impact of PSA Cycle Time
Definition of PSA Cycle Time: PSA cycle time is the time interval from the beginning of the adsorption process in one adsorption tower to the beginning of the next desorption process. This time directly affects the adsorption and desorption efficiency of the molecular sieve, which in turn affects the purity and yield of nitrogen as well as the stability of the system.
Factors affecting the cycle time:
Selection of adsorption material: different types of molecular sieves (e.g., type 4A, type 5A, etc.) have different adsorption capacity and working characteristics, which will directly affect the cycle efficiency of PSA.
Gas flow rate: too high or too low gas flow rate may affect the gas separation effect. Changes in flow rate need to be coordinated with the cycle time to ensure that the molecular sieve can effectively adsorb and release the gas.
Rate of pressure change: The rate of compression and decompression determines the efficiency of adsorption and desorption and affects the overall performance of the PSA system.
Relationship between cycle time and nitrogen purity:
Lengthening the cycle time: improves the purity of the nitrogen because the molecular sieve has more time to adsorb oxygen and moisture, but this can also lead to a decrease in gas production.
Shorten the cycle time: increase the gas yield, but it may lead to a decrease in the purity of nitrogen, because the molecular sieve fails to adsorb oxygen sufficiently.
Effect of cycle time on oxygen yield:
A long adsorption phase helps to release more oxygen and increase the oxygen yield. However, attention also needs to be paid to the pressure and flow rate control when oxygen is released to avoid unnecessary waste.
3. Optimization and application of PSA cycle time
How to optimize the cycle time:
Improvement of nitrogen purity: In order to improve nitrogen purity, it is usually necessary to extend the time of adsorption phase. This ensures that more oxygen is adsorbed and less oxygen enters the nitrogen stream, improving the quality of the gas produced.
Increase oxygen production: Optimizing the time and pressure control of the desorption stage ensures efficient release of oxygen and avoids waste of insufficient or excessive oxygen.
Balance cycle time and equipment energy efficiency: Reasonable adjustment of cycle time can not only meet the purity requirements of nitrogen and oxygen, but also effectively reduce the energy consumption of the system, improve the economy and sustainability of the equipment.
Application examples:
Medical industry: In the nitrogen generators used in hospitals, it is necessary to ensure that the purity of nitrogen reaches 99.9% or more, so in the PSA system, extending the adsorption phase is the key to ensure the purity.
Industrial gas production: In areas such as chemical and food packaging, PSA systems can adjust the cycle time according to production demand, ensuring both nitrogen production and a stable gas supply.
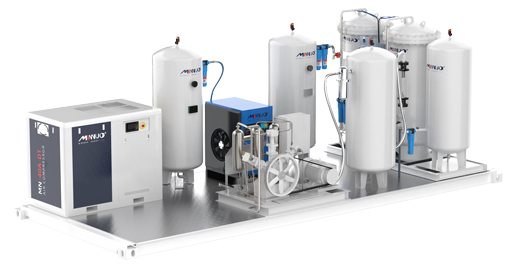
II.Effect of PSA Cycle Time on Nitrogen and Oxygen
1. Changes in Nitrogen Yield and Purity
Nitrogen Purity versus Cycle Time:
When the cycle time is longer: when the PSA system has a longer cycle time, the molecular sieves have more time to carry out the adsorption process of the gas. The increased time for molecular sieve adsorption contributes to the purity of the nitrogen because more oxygen and moisture are effectively removed. However, extending the adsorption time may result in some decrease in the nitrogen output. At this point, the output flow rate of nitrogen is relatively low, but the purity of nitrogen is higher.
When the cycle time is short: If the cycle time is short, the adsorption time of the molecular sieve becomes shorter, the adsorption process may be incomplete, and the oxygen is not sufficiently separated, which leads to a decrease in the purity of the nitrogen. However, a short cycle time can increase the nitrogen yield because the molecular sieve is able to release more nitrogen in a shorter period of time. This is very effective in applications where higher nitrogen yields are needed but purity requirements are low.
Examples of practical applications:
In the petrochemical and metallurgical industries, where there are high requirements for nitrogen purity, it is usually necessary to extend the cycle time to obtain the required purity and ensure the effectiveness of gas separation.
In the food packaging industry, although high yields of nitrogen are required to ensure a continuous production process, the purity of the nitrogen can be appropriately reduced to allow shorter cycle times to be used to improve the overall efficiency of the gas supply.
2. Variation in Oxygen Yield
Oxygen yield as a function of cycle time:
When the cycle time is extended: the molecular sieve is able to adsorb oxygen more efficiently due to the prolonged adsorption phase, which means that more oxygen can be released during the desorption phase. However, a long adsorption and desorption cycle reduces the nitrogen yield because more time is spent releasing oxygen.
When the cycle time is shortened: while a shorter cycle time increases the nitrogen yield, the release of oxygen may be incomplete, thus affecting the yield and purity of oxygen. Especially in some occasions where high purity nitrogen is required, such a fast cycle may result in a less than desired separation between oxygen and nitrogen.
3. Interaction of Nitrogen and Oxygen
Competitive Adsorption of Nitrogen and Oxygen:
Influence of Adsorbent Material: In PSA systems, the adsorption of nitrogen and oxygen by molecular sieves is competitive. Nitrogen and oxygen molecules are similar and have similar dimensions and physical properties, which causes their adsorption processes in the molecular sieve to interfere with each other. When the cycle time is too long, the molecular sieve has a better chance to adsorb oxygen, resulting in an increase in the concentration of nitrogen but a decrease in the concentration of oxygen.
Influence of flow rate: The higher the gas flow rate, the relative decrease in the adsorption time of the molecular sieve, and the decrease in the separation efficiency of nitrogen and oxygen, which may lead to a decrease in the purity of nitrogen and an increase in the emission of oxygen at the same time.
Balance and optimization:
Reasonable design of cycle time: Reasonable design of cycle time can ensure the balanced output of nitrogen and oxygen. For industries requiring high purity nitrogen, appropriately extending the adsorption stage can improve the separation effect; while in cases requiring high output, shortening the cycle time can improve the output, but it is still necessary to ensure that the efficiency of the equipment is not affected.
III. Strategies for Optimizing PSA Cycle Time
1. Adjusting the Cycle Time to Improve Nitrogen Purity
Extending the Adsorption Phase to Improve Nitrogen Purity:
In PSA systems, extending the adsorption phase increases the adsorption time of the molecular sieve for oxygen and moisture, which can help to improve the purity of the nitrogen gas. Especially in applications where high purity nitrogen is required, such as in electronics manufacturing, the chemical industry or the pharmaceutical industry, a longer adsorption time ensures that oxygen and moisture are completely adsorbed, thus avoiding any impact on the purity of the nitrogen.
Optimizing the switchover between adsorption and desorption:
In addition to extending the adsorption phase, optimizing the switchover between adsorption and desorption can also further improve nitrogen purity. Adopting intelligent control technology in the system to precisely adjust the ratio of adsorption time and desorption time can ensure the purity of the gas while avoiding unnecessary energy waste.
In applications where high precision is required, such as when nitrogen is used for welding protection, any small residue of oxygen will affect the quality of the final product, so the time of the adsorption phase must be strictly controlled.
Optimization suggestions:
Continuously monitor the gas purity through data analysis and equipment feedback, and dynamically adjust the cycle time according to the demand, in order to adapt to the requirements of different production processes.
2. Strategies to increase nitrogen production
Shorten the adsorption stage to increase nitrogen production:
In order to increase nitrogen production, you can shorten the time of adsorption stage to allow the molecular sieve to complete the adsorption process in a shorter period of time, so as to increase the production of nitrogen. This strategy is suitable for application scenarios that do not require high purity of nitrogen, but need high yield, such as food packaging, metal processing, etc.
It should be noted that shortening the adsorption time may result in oxygen not being fully adsorbed, thus reducing the purity of the nitrogen. Therefore, when implementing this strategy, the purity requirements of the nitrogen must be evaluated to avoid quality issues due to high throughput.
Optimize Desorption Stage Control:
By optimizing the pressure and time settings of the desorption stage, it is possible to increase the efficiency of the gas separation while maintaining the nitrogen yield. For example, efficient compressor technology and intelligent control systems are utilized to regulate the desorption process and ensure the timely release of oxygen, thus reducing contamination of the nitrogen and oxygen with each other.
In production lines with high flow demands, such as large-scale chemical production, adjusting the strategy of the desorption phase ensures that the system resumes operation quickly and maintains a stable nitrogen output.
Optimization suggestions:
Monitor the fluctuation of nitrogen output by analyzing historical data, and dynamically adjust the adsorption and desorption time of the PSA system in combination with the gas production demand to ensure a stable nitrogen supply.
3. Best practices for balancing nitrogen purity and production
Flexible adjustment according to demand:
For some application scenarios that require both high purity nitrogen and high production, adjusting the cycle time of PSA system requires fine management. In such cases, multi-stage optimization strategies, such as multi-stage adsorption, can be used to ensure high gas purity while gradually increasing throughput.
For example, in the field of oil and gas extraction or deep-cooled gas processing, where the balance between purity and yield is particularly important, flexible cycle time adjustment in PSA systems can optimize gas separation while ensuring safety and efficiency.
Improve energy efficiency and stability:
By reducing unnecessary cycles and optimizing the adsorption/desorption changeover cycle, the energy efficiency of PSA systems can be significantly improved, thus reducing energy consumption while maintaining nitrogen purity. This is important for remote operations and applications with low energy requirements, especially in remote areas or high energy consumption environments.
Optimization advice:
uses intelligent algorithms to analyze changes in gas demand during different processes and accurately adjusts the PSA system’s cycle time, avoiding unnecessary energy waste while maximizing productivity.
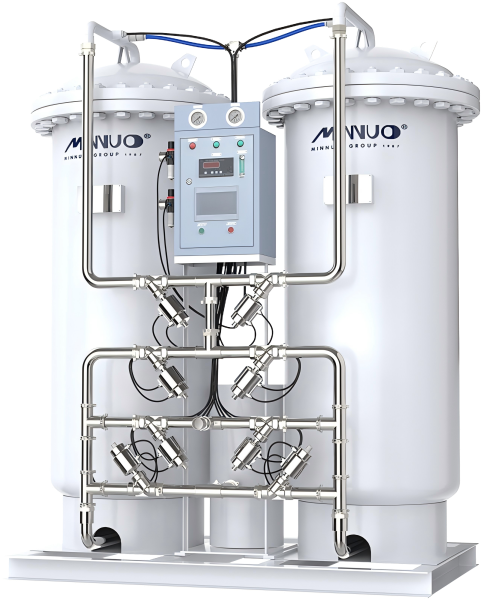
Ⅳ.The relationship between PSA cycle time and equipment performance
1. The effect of cycle time on equipment life
The effect of longer cycle time on equipment:
Increase in equipment load: although longer cycle time can improve the purity of nitrogen, it may also increase the load of equipment. For example, the molecular sieve tends to accumulate more contaminants (such as moisture and oil) during the long adsorption process, which will accelerate its aging and lead to more frequent maintenance and replacement of the equipment. Especially in the case of high purity requirements, too long a cycle time will make the service life of the equipment much shorter, increasing the operating costs of the equipment.
Regular material replacement: Excessively long cycle times also mean that adsorption materials, such as molecular sieves, need to be replaced regularly to maintain high nitrogen purity. After a long period of operation, the adsorption capacity of the molecular sieve will be reduced, and the material needs to be replaced with a new one to ensure system efficiency. As a result, the maintenance intervals of the equipment will be shorter, resulting in higher maintenance costs.
Impact of short cycles:
Increased yield but reduced stability: shorter cycle times can increase nitrogen yield, but may affect the long-term stability of the equipment. The equipment is prone to malfunctions and system fluctuations due to frequent switching operations and high loads in a short period of time, thus affecting the reliability of the equipment.
Decrease in energy efficiency: During short cycle operation, the molecular sieve fails to release oxygen and moisture effectively, which may lead to energy waste. Frequent starting and stopping of the equipment will also increase energy consumption and operating costs.
2. Factors affecting the life cycle of the equipment
How to choose the right cycle time to ensure long-term stable operation of the equipment:
Matching the equipment design with the application requirements: The design of the equipment must match its application requirements. Too long or too short a cycle time may lead to increased load on the equipment, affecting its long-term stability. Therefore, a reasonable selection of cycle time should not only consider productivity, but also the design of the equipment and the environment in which it is used.
Regular maintenance and inspection: PSA systems require regular maintenance and inspection to ensure the long-term stable operation of the equipment. The preventive maintenance program of the equipment should include the inspection of molecular sieve, compressor, pressure sensors and valves, and timely replacement of aging parts to avoid equipment failure due to improper cycle time.
Environmental Adaptability: How the equipment performs in different environments can also affect its life cycle. High temperatures, high humidity or extreme environmental conditions require that the pressure control and temperature regulation capabilities of the equipment be specifically designed to ensure that the equipment is able to adapt to long cycles of continuous operation.
Regular inspection of equipment:
Regular inspection and maintenance of the PSA system, especially molecular sieve, compressor and other key components, to ensure the efficient operation of the equipment. Intelligent monitoring system is adopted to monitor the status of the equipment in real time, so that potential problems can be detected early and dealt with in time to avoid damage to the equipment due to delayed maintenance.
3. Influence of cycle time on equipment energy efficiency
Comparison of energy efficiency between long and short cycles:
Advantage of long cycle time: Long adsorption and desorption process helps to reduce the energy consumption of the equipment, as the equipment is able to utilize adsorbent materials more efficiently in a longer cycle time, reducing unnecessary energy consumption. By extending the cycle time, the gas separation is enhanced and the stability of the equipment operation is increased, thus improving the overall energy efficiency of the system.
Disadvantages of short cycles: Although short cycles increase the gas yield, they are also accompanied by higher energy consumption. During frequent switching, the PSA system needs to start and stop constantly, which is energy inefficient. Long-term operation will lead to energy waste, affecting the economy and operational efficiency of the equipment.
Conclusion
Reasonable adjustment of the PSA cycle time is critical to the separation efficiency of nitrogen and oxygen. Extending the cycle time can improve the purity of nitrogen, but may lead to a decrease in yield, while shortening the cycle time can help improve the yield of nitrogen, but will affect the purity of the gas and the stability of the equipment. Therefore, it is critical to choose the right cycle time for different industrial application needs, which can ensure high purity nitrogen and high yield while improving the energy efficiency and stability of the system.
In order to achieve this goal, enterprises should consider the impact of cycle time on the separation efficiency of nitrogen and oxygen according to their own gas demand, equipment specifications and environmental conditions, and ensure the efficient operation and long-term stability of the equipment through optimized equipment design and regular maintenance.MINNUO oxygen and nitrogen plants, with advanced PSA technology and high-quality design concepts, provide highly efficient, stable and cost-effective With advanced PSA technology and quality design concepts, MINNUO oxygen and nitrogen plants provide efficient, stable and economical nitrogen solutions, helping enterprises to improve production efficiency while saving energy and reducing consumption.