Environmental temperature and pressure play a pivotal role in the efficiency of gas separation processes. Specifically, in PSA (Pressure Swing Adsorption) technology, the impact of varying temperature and pressure conditions directly influences the performance of the oxygen generation system. These environmental factors are integral to optimizing system performance and ensuring the steady production of high-purity oxygen.
This article explores how temperature and pressure affect PSA oxygen systems and how they can be optimized to maintain stable, high-efficiency performance. By providing precise methods for calculating and optimizing these factors, it will help engineers understand the intricate balance necessary for reliable and cost-effective oxygen production.
Understanding the influence of temperature and pressure is crucial for optimizing PSA systems. This article will delve deeper into the calculation methods used to evaluate these effects, providing actionable insights for enhancing system efficiency. Whether you are an engineer, technician, or industry professional, this guide will help you achieve better control over system design and operations, improving both productivity and cost-effectiveness.
I. The Basic Impact of Environmental Temperature and Pressure on PSA Oxygen Generation
1. Temperature’s Impact on PSA Oxygen Generation
High temperature: At higher temperatures, the physical properties of gases change, such as gas density and viscosity, leading to significant impacts on PSA (Pressure Swing Adsorption) oxygen generation. As the temperature rises, the density of the gas decreases, which can result in a reduction in the efficiency of the adsorption process.
Effect on adsorption efficiency: High temperatures may lead to a faster desorption rate, which means the adsorbent material (e.g., molecular sieve) will release gas at a faster rate than required. This reduces the capacity to separate oxygen and nitrogen, lowering the purity of the oxygen produced.
Equipment adjustments: Higher temperatures may require the equipment to work harder to maintain the desired output, potentially putting extra strain on the system. Additionally, the system may require more frequent maintenance as a result of wear and tear due to temperature fluctuations.
Conclusion: In high-temperature environments, it may be necessary to either adjust the cycle time or use more advanced cooling systems to compensate for the decreased gas density and prevent efficiency losses in the oxygen separation process.
2. Pressure’s Impact on PSA Oxygen Generation
Pressure has a direct relationship with the efficiency of gas separation in PSA systems. As the pressure in the adsorption tower increases, the ability to adsorb gases like oxygen improves, leading to more effective separation.
Low pressure environments: When the pressure decreases, the ability of the system to adsorb oxygen decreases. This reduction can lead to a lower purity of the oxygen produced as nitrogen is less effectively separated from the oxygen. Low pressure also reduces the overall efficiency of the system.
High pressure environments: Conversely, higher pressure improves the adsorption rate, allowing for more effective separation of oxygen from nitrogen. However, higher pressures can also increase energy consumption due to the need for more powerful compressors and other equipment to maintain such high pressure levels.
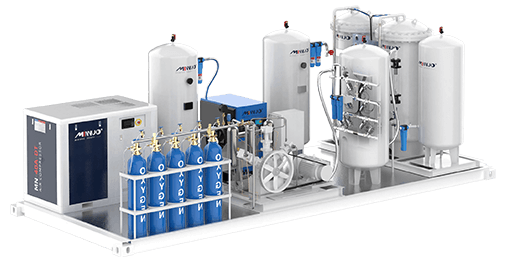
II. Temperature and Pressure Impact on PSA Oxygen Generation Efficiency Calculations
1. Temperature’s Impact on Oxygen Generation Efficiency
When calculating the impact of temperature on PSA oxygen generation, several factors must be considered:
Gas Behavior and Temperature: Gas molecules behave differently at various temperatures. As temperature increases, the gas molecules move faster, leading to a lower gas density and a reduction in the overall efficiency of the PSA system. This temperature variation can cause an imbalance in the adsorption process, where the molecular sieve adsorbs less oxygen, reducing the purity and output of the generated oxygen.
Effect on Oxygen Production: High temperatures reduce the efficiency of the adsorption process by making oxygen molecules harder to retain on the molecular sieve. The result is a decrease in the overall production of high-purity oxygen. In extreme cases, prolonged exposure to high temperatures may cause damage to the molecular sieve, further degrading the system’s efficiency.
Practical Application: To mitigate the adverse effects of temperature, cooling mechanisms or advanced materials that can withstand higher temperatures should be considered in the PSA system design. Additionally, adjusting cycle times to optimize the adsorption phase can help compensate for the reduced efficiency caused by temperature fluctuations.
Calculation Considerations:
Formula to calculate temperature’s impact on gas density:

where ρ is the gas density, P is the pressure, R is the universal gas constant, and T is the temperature in Kelvin.
Optimizing Process: By adjusting the operating conditions, such as increasing the flow rate to account for lower gas density, oxygen production can be maintained at an acceptable level.
2. Pressure’s Impact on Oxygen Generation Efficiency
Pressure plays a key role in controlling the efficiency of PSA systems, with direct consequences for both oxygen purity and overall production rates.
Pressure and Oxygen Adsorption: Higher pressure in the adsorption towers increases the ability of the system to adsorb oxygen, which enhances the efficiency of the separation process. As a result, the purity of the oxygen increases, and more oxygen can be captured for production.
Low Pressure Impact: In contrast, lower pressure can severely reduce the system’s efficiency. The decrease in pressure lowers the adsorption capacity of the molecular sieve, leading to a reduction in the purity of the oxygen and a decrease in production rates.
Optimal Pressure Levels: While higher pressures improve efficiency, they also increase energy consumption, as the compressors must work harder to maintain the required pressure levels. Therefore, it is crucial to balance the pressure to avoid overloading the system and increasing operational costs.
Practical Application:
Pressure Control: The pressure must be carefully managed to optimize oxygen production without incurring excessive energy costs. For example, adjusting the switching time in the PSA cycle to accommodate variations in pressure can help balance purity and yield while ensuring energy efficiency.
Calculation Considerations:
Pressure and Flow Rate Relationship: The pressure is directly proportional to the ability of the system to produce oxygen. A pressure drop calculation should consider the energy costs and balance them with the desired oxygen production rate.
III. PSA Oxygen System Optimization Strategies
1. Optimization Based on Temperature and Pressure
How to Optimize PSA System Based on Temperature and Pressure
The optimization of a PSA systems based on temperature and pressure primarily revolves around ensuring that the system operates efficiently under variable conditions. Temperature and pressure significantly influence the adsorption capacity and efficiency of the molecular sieve, which ultimately determines the purity and yield of the oxygen produced.
Temperature Control: By adjusting the temperature within a suitable range, the adsorption capacity of the molecular sieve can be optimized, which in turn enhances the overall oxygen production rate and purity. A well-controlled temperature ensures that the molecular sieve remains efficient over extended operating periods.
Pressure Control: The optimization of the PSA cycle should account for pressure variations to ensure that the system operates at an optimal pressure range. This includes adjusting the cycle times or making system design adjustments that take into account both temperature and pressure variations.
Practical Implementation
Material Selection: Select molecular sieves that are best suited for varying temperatures and pressures. High-temperature-resistant sieves should be used in high-temperature environments to maintain optimal performance.
System Design: Design the system to handle fluctuations in both temperature and pressure. This includes proper heat management, pressure controls, and the use of advanced sensors to monitor and adjust operational conditions dynamically.
Energy Efficiency: Ensuring that the temperature and pressure are optimized not only boosts production but also reduces energy consumption. By reducing the strain on compressors and temperature control systems, businesses can lower operational costs.
2. Reducing External Environmental Impact on System Performance
Minimizing Environmental Impact
Optimized Environment: It is essential to ensure that the operating environment of the PSA system remains stable. This involves designing the system to withstand external temperature and pressure variations that can affect gas separation efficiency.
System Adjustments: Ensuring optimal air conditioning, cooling, or heating in the plant will reduce any negative effects from fluctuating environmental conditions. The PSA system should be capable of adjusting to environmental factors that may arise, such as temperature swings or pressure changes.
Practical Approach to Environmental Considerations
Space and Equipment Configuration: Ensure that the equipment is placed in a well-ventilated and temperature-controlled area to protect it from external environmental influences. Regular maintenance of HVAC systems, air filters, and seals around the system also helps to create a stable operating environment.
Smart Controls: Using smart control systems that adjust both pressure and temperature automatically based on real-time data ensures that the PSA system operates under optimal conditions regardless of external fluctuations.
Proactive Planning: Before system installation, conducting a thorough environmental study to understand local temperature fluctuations and pressures can guide more informed design decisions, ensuring the PSA system performs optimally under any condition.
IV. Practical Application Cases and Optimization Suggestions
1. Temperature and Pressure Optimization in Industrial Applications
Impact of Temperature and Pressure on PSA Systems
In various industrial applications, such as pharmaceuticals, chemical manufacturing, and food packaging, temperature and pressure play a critical role in the efficiency and performance of PSA systems. These systems are particularly sensitive to changes in temperature, which can affect the adsorption capacity and, consequently, the output purity and flow rate of nitrogen or oxygen.
Optimization Approach: Adjusting the operating temperature and pressure within an optimal range can help achieve higher purity and more efficient production. By fine-tuning the conditions under which the PSA system operates, the system’s energy consumption can be minimized, and the overall performance can be maximized. A well-designed system will account for variations in environmental conditions and adapt to them effectively.
Example of Application: In high-temperature environments such as industrial boiler rooms, the temperature of the inlet gas may rise, which could lower the efficiency of the PSA process. In such cases, integrating a cooling system or utilizing temperature-controlled adsorption materials can help maintain stable operations.
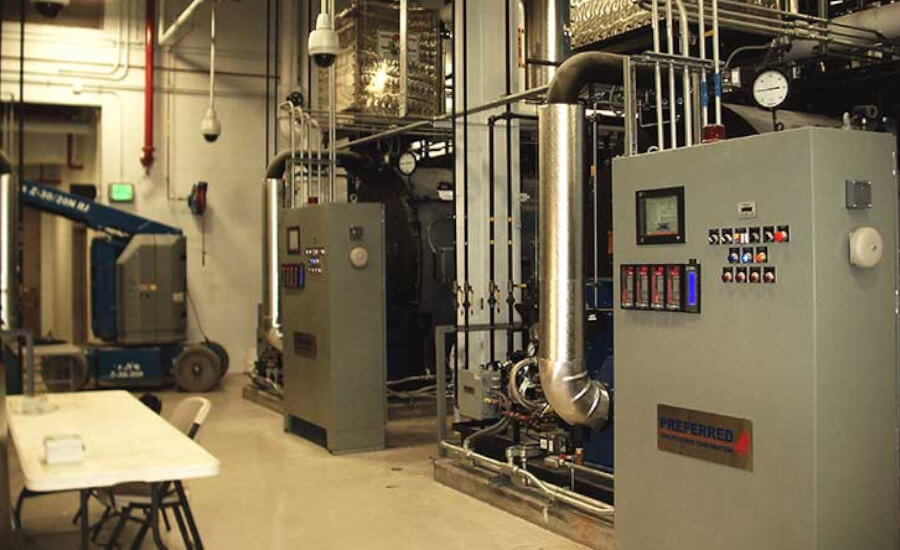
2. MINNUO’s PSA System Equipment Optimization
MINNUO’s Approach to PSA System Optimization
MINNUO understands the importance of precise temperature and pressure management in optimizing the performance of PSA systems. By offering systems that automatically adjust to varying temperatures and pressure conditions, MINNUO ensures that the equipment maintains high efficiency and stability, regardless of environmental fluctuations.
Design Optimization: MINNUO optimizes the design of its PSA equipment to ensure that the system performs effectively even under extreme temperature and pressure conditions. This includes selecting high-quality materials, incorporating effective thermal regulation, and ensuring that the system’s components are capable of handling varying operational loads.
Energy Efficiency: Through MINNUO’s design improvements, the energy consumption of the PSA system is minimized, which reduces operational costs. This is achieved by optimizing the energy transfer and recovery within the system, making sure that the gas supply remains stable and efficient without excess energy consumption.
Practical Examples:
High-Purity Oxygen Generation: For a large pharmaceutical plant requiring high-purity oxygen, MINNUO’s PSA system was optimized to handle fluctuating temperatures and pressures while maintaining consistent output. The system was equipped with real-time sensors to adjust its operation, ensuring that the plant received a constant supply of oxygen at the required purity level.
Energy Saving in Industrial Applications: In an industrial manufacturing plant where consistent nitrogen supply is critical, MINNUO’s PSA system was adjusted to optimize the pressure settings, reducing the overall energy consumption by 15%. This system adjustment ensured that nitrogen was generated efficiently while also extending the life of the equipment.
3. Recommendations for Improving PSA Systems in Practical Applications
Optimizing System Design
The efficiency of a PSA system can be improved by selecting the most appropriate components, including the adsorption material, system layout, and control systems. To ensure a more energy-efficient operation, regular system analysis and adjustments based on real-time data are essential.
Proactive Monitoring: Implementing advanced monitoring systems helps detect any inefficiencies in the system. Regular maintenance and optimization checks can ensure that the system continues to perform at its best, with reduced energy consumption and stable output.
Tailored Solutions: Each industrial application has unique requirements. Whether it’s for nitrogen generation or oxygen production, the system should be tailored to meet the specific needs of the client. This includes modifying the cycle times, adjusting flow rates, and even integrating energy recovery systems to make the operation more sustainable.
Conclusion
The environmental temperature and pressure play a crucial role in the performance of PSA oxygen systems, directly influencing both efficiency and stability. Accurate calculations and effective optimization of these parameters are essential to ensure that the PSA system operates at peak performance, delivering high-purity oxygen while minimizing energy consumption.
By understanding the intricate relationship between temperature, pressure, and PSA system efficiency, engineers can fine-tune the system’s design and operational parameters to maintain optimal conditions. Through careful temperature and pressure management, the overall system performance can be enhanced, contributing to greater economic savings and more reliable operations.
As industrial demands evolve, PSA technology continues to advance, with ongoing improvements driving higher levels of automation and greater control over temperature and pressure fluctuations. These advancements pave the way for further optimization of oxygen and nitrogen production, ensuring that companies can maintain high production standards and reduce costs.
MINNUO, with the state-of-the-art PSA oxygen and nitrogen systems, leverages advanced technology to provide reliable, energy-efficient, and cost-effective solutions. With a commitment to delivering optimal gas production, MINNUO’s systems are designed to adjust seamlessly to varying environmental conditions, ensuring stable operation and meeting the diverse needs of industries worldwide.