PSA (Pressure Swing Adsorption) nitrogen generators have gained significant prominence in nitrogen production, gas separation, and numerous industrial gas treatment applications due to their ease of operation and cost-effectiveness. However, with the arrival of summer, high temperatures not only trigger equipment failures and shorten the lifespan of the system but also cause severe disruption to the entire production process. Therefore, an in-depth analysis of the causes and solutions for high temperatures in PSA nitrogen generators is crucial for ensuring stable equipment operation.
The primary causes of high temperatures in PSA nitrogen generators include heat accumulation in the adsorption tower, excessive compressor load, cooling system malfunctions or inadequate design, molecular sieve performance degradation, and the impact of external environmental temperatures. To address these issues, solutions include improving the heat management efficiency of the adsorption tower, optimizing compressor operating methods, enhancing the cooling system, regularly replacing molecular sieves, controlling the working environment temperature, and implementing intelligent temperature control systems.
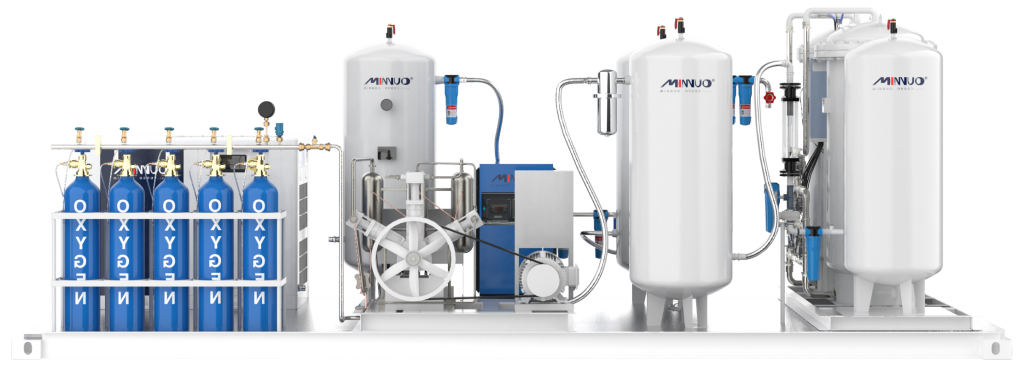
I. Main Causes of High Temperatures in PSA Nitrogen Generators
1. Heat Accumulation in the Adsorption Tower
The adsorption tower, as the core component of the PSA nitrogen generator for gas separation, undergoes complex thermal changes during operation. During the adsorption stage, gas pressure changes and molecular interactions release a significant amount of heat; during the desorption stage, heat absorption is required. When the nitrogen generator is operating under high load or continuous running for extended periods, heat within the adsorption tower is difficult to dissipate quickly, resembling a “small furnace” that constantly accumulates heat, causing the system’s temperature to rise.
According to actual monitoring data, under certain high-load conditions, the temperature inside the adsorption tower can increase by 15 – 20°C within hours. Excessive temperatures can significantly reduce the adsorption efficiency of molecular sieves. Research has shown that for every 10°C increase in temperature, the adsorption capacity for oxygen may decrease by 8% – 12%. Additionally, energy consumption increases, and the quality of gas production and operational performance are notably affected.
2. Excessive Compressor Load
The compressor is responsible for compressing atmospheric air to high pressure and delivering it to the adsorption tower, serving as the “power heart” of the nitrogen generator. During operation, the mechanical movement of the compressor and the violent collisions of gas molecules during air compression generate significant heat. If the compressor operates in an overloaded state for an extended period, especially with frequent starts and stops or high-load operation, excessive heat accumulates rapidly.
A chemical enterprise once faced a surge in production demand, causing the compressor to operate under overload for an extended period. In just one week, the compressor’s temperature soared from a normal 40°C to 75°C, severely affecting nitrogen production efficiency and leading to wear on certain components. Furthermore, unstable compressor operation or improper load matching can exacerbate the thermal effect, further increasing the equipment’s temperature.
3. Cooling System Malfunctions or Inadequate Design
The cooling system acts as the “heat dissipation guardian” of the nitrogen generator, removing the heat generated during equipment operation through cooling water or air. Once the cooling system is poorly designed or malfunctions—such as insufficient cooling water flow, clogging, or scaling—the heat dissipation effect is compromised, preventing heat from being released in a timely manner, and the equipment’s temperature inevitably rises.
In practice, some enterprises neglect cooling system maintenance, leading to severe scaling in coolers, which reduces heat exchange efficiency by 30% – 40%. Furthermore, long-term lack of cleaning and maintenance of the cooling system decreases heat dissipation efficiency and seriously threatens the stable operation of the PSA nitrogen generator.
4. Molecular Sieve Performance Degradation
As the “core brain” of the PSA nitrogen generator that separates oxygen and nitrogen, the molecular sieve’s adsorption capacity gradually degrades with increasing usage. The time required for adsorption and desorption increases, leading to the continuous accumulation of heat in the adsorption tower. After aging, the gas separation process becomes slower, generating more heat and driving the equipment’s temperature upwards.
Statistics show that after 3 – 5 years of use, if the molecular sieve is not replaced in time, the nitrogen generator’s operating temperature may rise by 10 – 15°C, nitrogen production efficiency could decrease by 15% – 20%, and energy consumption could increase by 10% – 15%, severely affecting enterprise production efficiency.
5. External Environmental Temperature Influence
The installation environment of the PSA nitrogen generator directly impacts its operating temperature. In high-temperature environments, heat dissipation is significantly limited, and the efficiency of the cooling system also declines. For example, in the hot outdoor environment during summer, the air temperature around the equipment may be too high, causing the cooling air to fail to effectively carry away heat, and the cooling water’s effectiveness also decreases. Data indicates that when the ambient temperature rises from 25°C to 40°C, the operating temperature of the nitrogen generator may increase by 5 – 8°C.
II. Solutions for High Temperatures in PSA Nitrogen Generators
To address the high-temperature problem in PSA nitrogen generators, we can adopt a series of effective solutions from multiple dimensions, including equipment design, operational management, environmental control, and maintenance management.
1. Improve Heat Management Efficiency in the Adsorption Tower
- Increase Heat Exchanger Efficiency: The heat exchanger plays a critical role in the heat dissipation process of the nitrogen generator. By selecting high-efficiency heat exchangers, such as those made from new heat pipe technology or high-performance composite materials, the heat transfer efficiency between the adsorption tower and heat exchanger can be greatly improved. After a company replaced its heat exchanger with a new model, the temperature fluctuation range inside the adsorption tower reduced from ±10°C to ±5°C.
- Control Adsorption Temperature in Phases: During adsorption, use advanced temperature control systems to finely adjust the adsorption temperature and reduce the temperature rise. During desorption, reasonably adjust the desorption time and gas flow rate to reduce temperature fluctuations. This method has been proven to lower the average temperature of the adsorption tower by 8 – 10°C.
- Reasonable Set Adsorption and Desorption Cycles: Based on the equipment’s actual operating conditions, optimize the coordination of adsorption and desorption cycles. For high-load operation of the nitrogen generator, appropriately shorten the adsorption cycle and extend the desorption cycle to effectively avoid long periods of high-temperature operation in the adsorption tower and reduce the overall system temperature.
2. Optimize Compressor Operating Methods
- Use Variable Frequency Drive Technology: A variable frequency drive (VFD) can automatically adjust the compressor’s speed according to the load changes. When the load is low, the speed is reduced to save energy and reduce heat generation; at the same time, smooth starts avoid thermal shock caused by frequent starts and stops. A food processing enterprise that adopted VFD technology saw its compressor energy consumption reduce by 18%, with temperature remaining within normal ranges.
- Regular Compressor Maintenance: Establish a complete compressor maintenance system, regularly check its operating status, clean coolers, filters, and other components, and ensure they are in optimal working condition. Also, focus on the lubrication system to ensure adequate oil levels and reduce friction-generated heat.
- Properly Select Compressors: Based on the actual gas demand of the enterprise, accurately select suitable compressors and flexibly adjust working parameters. For high-load conditions, configure high-power compressors to prevent overload operation of a single compressor.
3. Improve the Cooling System
- Choose Appropriate Cooling Methods: Based on nitrogen generator load requirements, select the proper cooling methods. For large-load equipment, prioritize high-efficiency liquid cooling systems or add auxiliary cooling devices, such as air coolers and external cooling units, to improve cooling effectiveness.
- Regularly Clean the Cooling System: Implement a cleaning plan for the cooling system, regularly remove dirt and impurities. For water cooling systems, ensure smooth water flow and control the temperature and flow of cooling water.
- Increase Cooling Water Flow: By increasing the cooling water flow, heat exchange speed is accelerated, and internal heat of the equipment is quickly removed. Experimental data shows that increasing the cooling water flow by 20% – 30% can lower the equipment temperature by 5 – 8°C.
4. Replace and Optimize Molecular Sieves
- Regularly Replace Molecular Sieves: Establish a regular inspection system for molecular sieves. Once performance degradation is detected, replace them in time. It is recommended to conduct comprehensive testing of molecular sieves every 2 – 3 years to ensure efficient operation of the system.
- Select High-Temperature Resistant Molecular Sieves: Use high-performance molecular sieve materials that are resistant to high temperatures and pollution, maintaining stable performance in high-temperature environments and reducing the temperature rise caused by molecular sieve performance degradation.
5. Control Working Environment Temperature
- Select a Well-Ventilated Installation Location: Install the PSA nitrogen generator in a well-ventilated and shaded area to avoid direct sunlight and the impact of high-temperature environments, creating favorable heat dissipation conditions for the equipment.
- Install Air Conditioning or Cooling Devices: In high-temperature areas, equip the system with air conditioning or other cooling devices to maintain a suitable environment temperature and reduce the burden on the temperature control system.
6. Implement an Intelligent Temperature Control System
Leverage automation technology to deploy an intelligent temperature control system. By using high-precision sensors to monitor the equipment temperature in real-time, the intelligent control system can automatically adjust the cooling system’s operational status based on temperature changes, ensuring that the equipment remains within the optimal temperature range. After a large enterprise implemented the intelligent temperature control system, the nitrogen generator’s temperature fluctuation range was controlled within ±3°C, significantly improving the equipment’s stability and reliability.
III. Conclusion
High temperatures in nitrogen generators are a critical factor limiting stable operation. As a professional PSA nitrogen generator manufacturer, MINNUO is always customer-oriented and committed to providing efficient and stable nitrogen generation solutions worldwide. We will continue to provide customers with more efficient, safe, and reliable nitrogen generation equipment, ensuring stable and efficient operation in various complex working environments.