In the evolving landscape of industrial gas applications—ranging from steel manufacturing and electronics to medical oxygen and hydrogen energy—efficient on-site gas separation is becoming increasingly crucial. Among the various gas generation technologies, two have emerged as mainstream choices: Cryogenic Air Separation Units (ASU) and Pressure Swing Adsorption (PSA) systems. Each offers distinct technical strengths and fits different operational contexts, particularly when it comes to separating oxygen and nitrogen.
This article aims to demystify the question: Which technology is right for your gas needs? By comparing cryogenic ASUs and PSA systems across five core dimensions—purity, capacity, energy efficiency, footprint, and flexibility—we address the core concerns of engineering teams, project investors, and industrial gas planners. Readers will gain actionable insights into how these two systems align with different production scenarios, gas purity targets, and operational constraints.
Whether you’re operating a steel plant requiring 99.999% oxygen or managing a packaging line that needs flexible mid-purity nitrogen, understanding the trade-offs between PSA and cryogenic separation can help you avoid overinvestment, underperformance, or design mismatch. Let’s break down the science, economics, and real-world fit of both technologies to guide your next decision.
I. Overview of the Two Technologies
In modern industrial gas supply, choosing the right separation technology is crucial for controlling costs, ensuring gas quality and system stability. The two mainstream oxygen/nitrogen technologies are Cryogenic Air Separation (ASU) and Pressure Swing Adsorption (PSA). They are based on different physical principles and are suitable for different application scenarios.
1. Cryogenic Air Separation
Working Principle:
Cryogenic Air Separation technology relies on the difference in the boiling points of different gases in the air, and separates high purity gases such as oxygen, nitrogen, argon, and other gases by cooling down the air to about -180°C or less, and then liquefying the air to enter into the distillation column for fractionation.
Core features:
Oxygen purity can be up to ≥ 99.5%, nitrogen can be up to ≥ 99.999%, argon can be co-produced
The system has a complex structure, which usually includes a compressor, a cold box, a heat exchanger, a distillation tower, a liquid storage tank, etc.
It is suitable for large-scale and continuity gas demand scenarios.
Typical application scenarios:
Iron and Steel Metallurgy (Oxygen blowing and refining)
Large-scale Chemical Industry (Raw material gas, protective gas)
Power plant (Oxygen fueling from Air Separation)
Gas company (Bottled or Gas company (bottled or liquid gas sales)
✅ Technical highlights: high output, high purity, can be co-produced with a variety of gases
❌ Limitations: high initial investment, high operating energy consumption, long start-up time, not suitable for flexible load adjustment
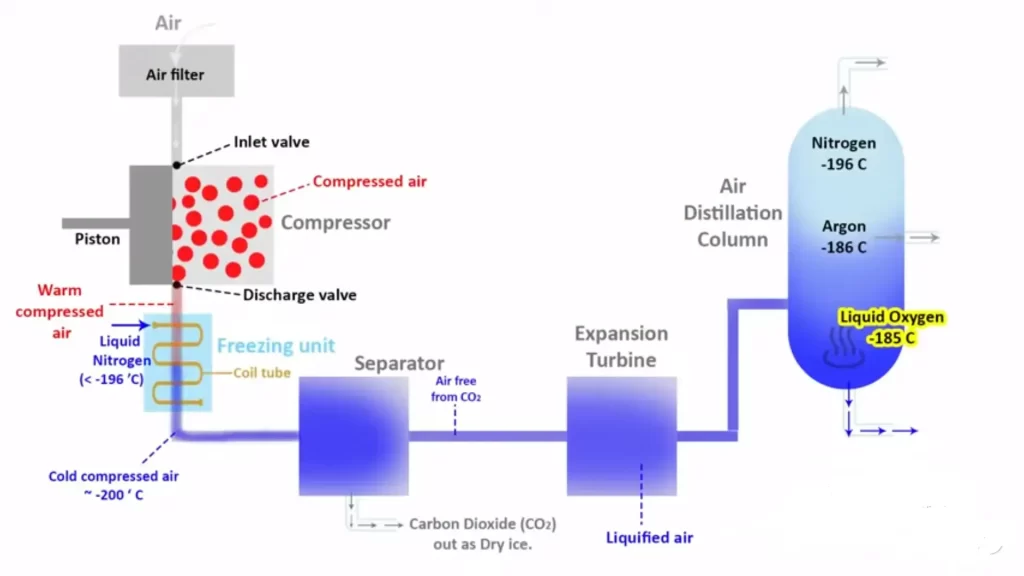
2. PSA (Pressure Swing Adsorption)
Working Principle:
PSA utilizes the adsorption of different gases under high pressure by molecular sieve materials (e.g., Carbon molecular sieve, Zeolite 13X), which can be adsorbed under high pressure by different gases. PSA utilizes the difference in adsorption capacity of molecular sieve materials (e.g. carbon molecular sieve, Zeolite 13X) on different gases under high pressure to adsorb a certain component in the air (e.g. nitrogen or oxygen) in a directional manner, while other gases are outputted through it, thus realizing the gas separation. When the pressure decreases, the adsorbed gas is released and the molecular sieve is regenerated.
Core features:
Oxygen purity is usually in the range of 90% to 95%; nitrogen purity 95% to 99.5%
Adopting dual-tower alternating operation: adsorption and regeneration cycle switching is stable
Modular structure, easy for rapid deployment and expansion
Typical application scenarios:
Food industry (nitrogen preservation and packaging)
Medical oxygen station and emergency ambulance oxygen supply system
Metal processing (laser cutting oxygen)
Laboratory, breeding, ozone generator, and other small and medium flow sites Oxygen/nitrogen demand
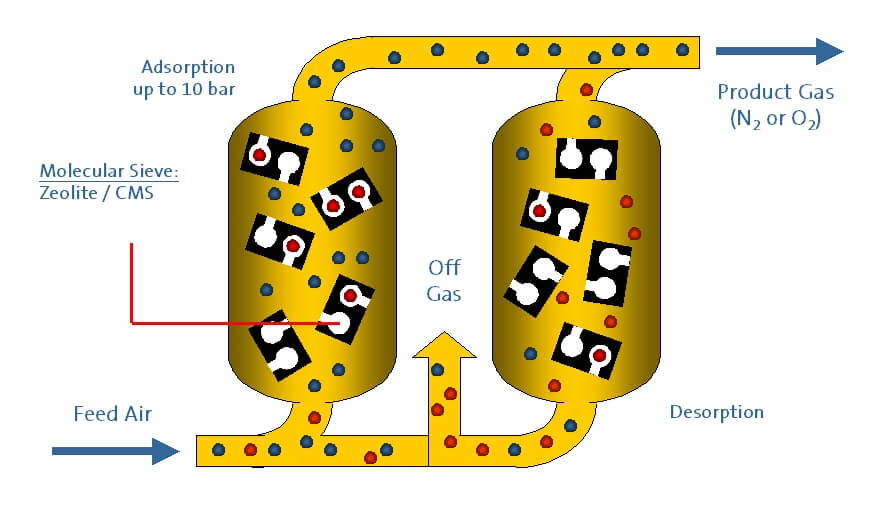
✅ Technology highlights: fast startup, low energy consumption, adaptable, small footprint
❌ Limitations: unable to produce high-purity argon, gas purity is limited by adsorption selectivity
Technology Direction | Gas Type | Oxygen/Nitrogen Purity | Start-up time | Applicable Scenarios | Scalability | Energy consumption |
Cryogenic Air Separation | Oxygen, Nitrogen, Argon | ≥99.5% (oxygen) ≥99.999% (nitrogen) | number of hours | Large industrial sites | One-time design | high |
PSA Adsorption | Oxygen, Nitrogen | 90-95% (oxygen) 95-99.5% (nitrogen) | number of minutes | Distributed/small and medium-sized factories | Modularity | low |
II. Comparison Criteria
The process of choosing a gas separation technology is essentially a weighing of multi-dimensional factors such as purity requirements, production scale, operation and maintenance difficulties and economics. The following is a comparative analysis of Cryogenic Air Separation (Cryogenic Air Separation) and PSA (Pressure Swing Adsorption) from the five core dimensions, which will help industrial users to accurately select the right gas separation technology.
1. Gas Purity & Type of Gases Produced
Cryogenic Air Separation:
The technical advantage lies in the high purity separation, which can realize:
Oxygen ≥99.5%
Nitrogen ≥99.999%
can also co-produce argon (commonly used in welding, rare gas recovery)
Applicable to the scenarios with very high requirements on purity and multi-gas co-production, such as electronic grade, high-end manufacturing, steel and iron. Refining
PSA Adsorption:
Oxygen purity is usually 90-95%, nitrogen can reach 95-99.5%, but argon can not be separated
Suitable for industries with medium purity requirements but high stability requirements, such as food encapsulation, medical oxygen supply, ozone systems
To summarize:
If you need ultra-high purity gases or co-production of argon, choose Cryogenic
If the goal is a single medium to high purity gas for a sustained period of time. If the goal is continuous supply of a single medium to high purity gas, PSA is more cost-effective.
2. Production Capacity
Cryogenic Air Separation:
Starting capacity is high, usually from 500 Nm³/h, and the scale can reach 10,000 plants.
Most of the projects are customized EPC projects, which are suitable for oxygen stations, iron and steel mills, and large chemical parks.
PSA Adsorption:
Starting capacity is flexible, from 10 Nm³/h, commonly used in hospitals, laboratories, ozone systems, and other industries. PSA adsorption: flexible start-up, as small as 10 Nm³/h, commonly used in hospitals, laboratories, mobile oxygen trucks
Modular structure supports multi-point distribution, on-demand deployment, suitable for small and medium-sized enterprises or scenario-based gas production
Summary:
Cryogenic for large gas production and centralized gas supply
PSA for flexible capacity expansion and point-to-point application
3. Energy Efficiency & Operational Costs
Cryogenic Air Separation:
High initial investment (over one million), deep cooling system required for operation, high power consumption
However, under large-scale operation, the energy consumption per unit of gas (kWh/Nm³) gradually decreases, which is economically advantageous
PSA Adsorption:
Low operating cost, often equipped with inverter compressors
Simple system, easy maintenance, low failure rate, suitable for “less manned” scenarios
However, under the demand of large gas production, the energy consumption per unit is not as high as that of air compressor. However, under large gas production demand, the unit energy consumption is not as good as that of air separation.
Summary:
Focus on long-term bulk gas supply cost, choose Cryogenic
Focus on flexible energy consumption control, low maintenance, choose PSA
4. Footprint & Installation Complexity
Cryogenic Air Separation:
The system includes a cold box, a distillation tower, and liquid oxygen storage tanks, and occupies a large area.
Infrastructure construction cycle is long, and construction is complicated. Complexity
PSA Adsorption:
Usually adopts integrated cabinet or skid-mounted module, compact footprint
Short installation cycle (can be put into operation within 1 week), no need for special foundation
Summary:
If the project has a fixed plant and infrastructure, it can be considered as a Cryogenic
If the site is restricted, and it is desirable to have rapid deployment and mobile deployment, PSA has obvious advantages
5. System Flexibility & Scalability Cryogenic Air Separation
The system includes cold box, distillation tower, liquid oxygen storage tanks, large footprint. Scalability
Cryogenic Air Separation:
Slow response to load changes, not conducive to frequent start/stop or flow adjustment
Usually requires ≥24 hours of stable operation to be efficient
PSA Adsorption:
Supports automatic frequency conversion and graded operation
Flexible capacity expansion by adding modules
Easy to intelligently connect to SCADA/remote control system
PSA is more adaptable if the gas load fluctuates a lot or needs to be operated in stages. If gas consumption is stable, continuous operation and long-term projects, air separation is preferred.
Technology Comparison Table
Comparison dimensions | Cryogenic Air Separation | PSA Pressure Swing Adsorption |
Gas purity | Oxygen ≥99.5%, Nitrogen ≥99.999%, can be co-produced argon | Oxygen 90-95%, Nitrogen 95-99.5%, no argon |
Individual unit capacity | ≥500 Nm³/h up | 10-500 Nm³/h Flexible configurations |
Initial investment | High, equipment + civil + cold box system | Medium, skid-mounted and delivered ready to use |
Operational energy consumption | Low unit cost for large production | More energy efficient at small and medium capacities |
Footprint and construction | Large system, long cycle | Modular, small footprint, rapidly deployable |
Control and expansion | High stability, but slow response | Supports dynamic operation and AI control |
III. Application Scenarios and Industry Fit
When choosing oxygen/nitrogen separation technology, industrial users not only need to consider the performance parameters of the equipment, but also need to combine the actual application scenarios and industry characteristics to make a judgment. The following summarizes the typical industry suitability of Cryogenic and PSA technologies from the perspective of different usage environments and process requirements, and provides a comparative explanation of the scenarios.
Industries Suitable for Cryogenic Air Separation (Cryogenic Separation) Technology
Cryogenic air separation is often used in heavy industries that require large-scale stable gas supply or extremely high purity requirements due to its high purity, high output and multi-gas cogeneration capability:
Industry Scenarios | Application Notes | Core requirements |
Iron and steel smelters | Blast furnace blast, converter oxygen blowing, steel decarburization | Continuous supply of high-flow oxygen (≥5000Nm³/h) |
Liquid gas suppliers | Liquid oxygen, liquid nitrogen, liquid argon filling, transportation and sales | Need to produce liquid gas storage and transportation |
Aerospace | Oxygen combustion, ultra-high purity nitrogen encapsulation | Nitrogen purity ≥99.999% |
Petrochemicals | Refinery cracker, hydrogen and oxygen combustion | Stable co-production of multiple gases |
Large chemical parks | Regional centralized gas supply | Uniform connection of gas for multiple users, cost-sensitive |
Cryogenic is better suited for centralized supply scenarios of “high purity, multiple gas types, high flow rates, and continuity”, and its deep-cooling liquefaction capability makes it irreplaceable in the liquid gas supply chain.
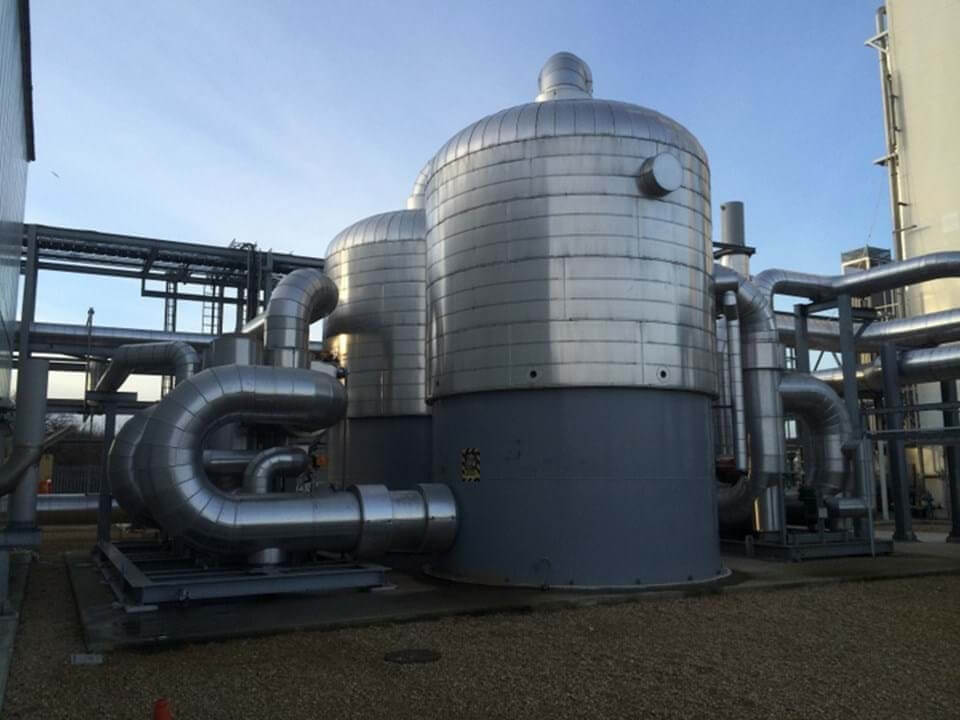
Industries suitable for PSA (Pressure Swing Adsorption) technology
PSA technology is widely used in small and medium-sized enterprises, experimental scenarios, or for flexible deployments due to its modularity, miniaturization, and low energy consumption:
Industry Scenarios | Application Notes | Core requirements |
Medical institutions, ICU wards | Medical grade oxygen supply, oxygen stations, oxygen tanks | Stable oxygen supply, high safety, continuous operation |
Nitrogen-filled food packaging | Nitrogen filling to prevent oxidation, corrosion and freshness | Nitrogen purity ≥99%, excellent stability |
Laser cutting, welding workshop | Oxygen for high-precision metal processing | Oxygen flow rate is medium, fast response and stable purity are required |
Aquaculture, ozone generator | Oxygen supply for water or ozone reaction source | Oxygen ≥93%, small size, continuous operation |
Laboratory, colleges and universities, scientific research | Nitrogen/oxygen for experimental analysis reaction | Medium-low flow rate, control accuracy, compact footprint |
Summary: PSA is suitable for users with “medium purity + medium-low traffic + distributed deployment”, especially for industrial customers with comprehensive requirements for response speed, energy consumption and space.
Comparison Table of Technology and Scenario Matching
Industry Type | Recommended Technologies | Reason analysis |
Steel/Chemical/Power | Cryogenic Air Separation | High purity + high flow rate + multi-gas co-production |
Medical Oxygen | PSA | ≥93% oxygen stable supply, no need for liquid oxygen transportation |
Food Packaging | PSA | Flexible deployment, fast start-up, energy saving |
Gas Filling | Cryogenic | Liquid gas can be produced, suitable for filling, storage and transportation |
Laboratory | PSA | High control precision, small footprint, easy to maintain |
Gas Suppliers | Cryogenic | Oxygen / Nitrogen / Argon triple production, suitable for bulk marketing |
IV. Hybrid Solutions and Emerging Trends
As industrial scenarios place greater demands on gas supply in terms of purity + flexibility + cost, it is becoming increasingly difficult for a single technology model (e.g. Cryogenic or PSA only) to meet all the requirements. More and more gas systems are evolving towards a ‘hybrid model’, integrating the benefits of different technologies to provide a more adaptable solution. Here are the three main trends:
1. Cryogenic + PSA Combined Gas Supply System: Combining High Purity and Flexibility
Application Background:
In large-scale parks such as steel and power plants, some equipment (e.g., converters and blast furnaces) requires high-purity oxygen, while other production processes only require 90-93% medium-purity oxygen.
Technical Solution:
Cryogenic air separation mainframe produces high purity oxygen, which is used for key production;
PSA is used as a “distributed auxiliary unit”, which flexibly supplements regional or medium purity demand;
Both of them are managed by PLC, and the pipeline network scheduling completes the “ladder oxygen supply”.
Advantages:
Significantly reduce the load and energy consumption of cryogenic mainframe;
PSA quick-start and quick-stop, adapt to fluctuating gas consumption;
single system to meet multiple levels of purity, improve the overall energy utilization rate.
Typical applications: metallurgical parks, regional gas centers, urban centralized oxygen supply pipeline network
2. PSA + Membrane Separation/TSA Technology Combination Trend
Technology Integration Logic:
Membrane Separation + PSA:
Membrane system first initially enriches nitrogen or oxygen (purity up to 90-95%), and then PSA is purified in-depth to 99.5%-99.999%; it can be used in the following applications: Nitrogen or Oxygen (99.5%-99.999%). 99.999%;
can be used in electronics industry, bottled gas station.
TSA + PSA (Temperature Swing Adsorption + Pressure Swing Adsorption):
TSA stage focuses on drying/removing impurities;
PSA completes gas separation;
is more suitable for humid, high dust, heavy corrosion and other harsh environments.
Advantageous analysis:
Multi-stage separation, reduce PSA load;
Enhance the separation efficiency and gas purity;
Improve the system adaptability and extend the life of core components.
✅ Suitable for users: fine chemicals, semiconductor plants, bottled gas processing enterprises
3. Evolution of small air separation modular equipment: providing “high purity solutions” for small and medium-sized gas consumption scenarios
Market pain points: traditional air separation system equipment is large, long cycle time, and it is difficult to enter the medium-sized industrial sites (e.g., glass factories and fertilizer factories that consume <2,000 tons of oxygen per year).
Development trend:
Highly integrated modular Skid design;
Overall frame occupies <10m2, realizing continuous output of 95-99.5% oxygen;
Modules can be connected in parallel to expand capacity, easy to maintain and replace.
Practical value:
Expanding the scope of high purity oxygen in medium-sized users;
Reducing the time of civil construction and deployment;
Reducing the threshold of preliminary investment and later maintenance.
Typical applications: Medium-sized glass plants, ozone generating equipment manufacturers, precision welding sites
Mixed Trend Value Overview
Hybrid Technology Path | Solving Pain Points | Scenarios |
Cryogenic + PSA | High Purity + Flexible Adjustment | District gas supply, steel parks |
Membrane + PSA / TSA + PSA | High Efficiency Purification, Resistance to Moisture Rot | Semiconductors, bottled oxygen, tropical humid zones |
Modular Air Separation + PSA | Lack of Pipeline Networks, High Purity Requirements | Medium-sized manufacturing plants, remote sites |
Conclusion
When selecting between cryogenic air separation and PSA technology, the decision ultimately depends on your gas purity requirements, consumption scale, operating flexibility, and project budget. Cryogenic ASU is unmatched in ultra-high purity (>99.5%) and large-volume output, making it the ideal solution for steel plants, industrial parks, and air separation units that serve multiple gas users. PSA, on the other hand, is favored for its cost-efficiency, compact footprint, quick start-up, and ease of automation—perfectly suited for small-to-medium-scale users in food packaging, laser cutting, oxygen bottling, and decentralized gas supply.
For businesses seeking a tailored oxygen or nitrogen generation system, MINNUO offers a full portfolio of PSA-based and hybrid gas solutions that balance performance and cost. Our systems feature modular design, PLC-based intelligent control, and high-efficiency components for 24/7 reliable operation. Whether you need high-purity oxygen for metallurgy or energy-saving PSA for packaging lines, MINNUO’s engineering team is ready to help you deploy the right technology—securely, sustainably, and at scale.